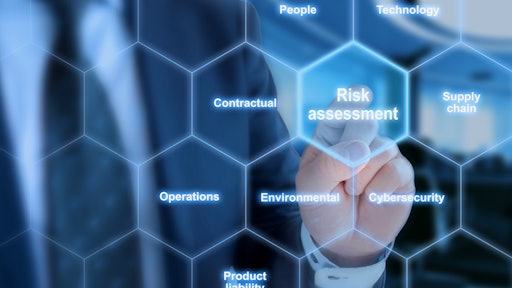
In the understatement of the year, and every year since 2020, supply chains have learned that unexpected situations can disrupt normal operations. Since recent history has proven that no organization can avoid unexpected disruptions, and since it’s well known that hope is not an actionable strategy, it’s vital that organizations—especially critical supply chains—create contingency plans.
What is a Contingency Plan?
A contingency plan spells out the actions to take, such as reallocating money, people, equipment and other resources, when certain triggering events like crises or disruptions occur. Given the varied nature of potential disruptions that can impact supply chains (including, but not limited to, labor shortages, public health concerns, changing government regulations, price hikes, transportation issues and product availability), organizations would be wise to build out a playbook that has more than one scenario for their contingency plans.
Current State of Risk Readiness
In an APQC poll of 166 supply chain professionals, APQC found that 32% were extremely concerned about the future of global supply chains and another 44% were moderately concerned. But worry is not enough. Action is needed.
And that’s where contingency planning comes in. APQC collaborated with BCG on research entitled If Disruption is the New Normal, Operational Resilience is the New Necessity, and contingency playbooks were identified as one piece of building resilience. Figure 1 shows in descending order of maturity, the percentage of research participants at each level of risk and contingency planning.
APQC Fig. 1
Contingency Planning Maturity Levels
Along the spectrum of maturity levels for contingency planning defined in Figure 1, it is alarming to note that almost one quarter (24%) of respondents have no documented plan, playbook or designated risk team. This is the equivalent of jumping off a building without a safety net or bungee cord—not advisable if future survival is desired.
33% of respondents have at least a designated crisis management team, but in those organizations, the team only meets reactively and has limited capabilities. Being reactive means that time is wasted after a disruption before the team can meet, make plans and then execute. This costs valuable time and money as illustrated in “Continuous Global Risk Monitoring” below.
Up one more step on the maturity ladder, 31% have a dedicated crisis management team, a resilience strategy team, and a solid playbook for “common” disasters. This is a definite step in the right direction. It’s important to practice scenarios for disasters via simulations similar to “war games” so that when one happens, the organization has developed muscle memory in its ability to respond.
At the top of the maturity scale, we see that 15% of organizations have a dynamic playbook, with risk and resilience embedded in every function. The dynamic element is important—this means capturing lessons learned as they happen so organizations don’t need to reinvent the wheel each time. And ensuring that all functions possess risk and resilience capabilities means the entire organization can react when a contingency plan needs to be executed, not just a handful of selected team members. Given the complexity of supply chains, it takes a village to be successful, especially when things change.
Even though we see that a sizable chunk of organizations are not particularly mature in terms of contingency plans, the good news is that risk management is top of mind for many. Our research asked respondents to rank risk and resilience levers based on what their organizations are doing today. When asked about “Crisis Response and Contingency Planning - Building resources and processes for rapid crisis response and adopting simulations and scenario planning to improve response,” 68% of 182 respondents ranked this element among their top three priorities.
Strategies for Improving Contingency Planning
To construct a mature contingency playbook, consider adopting approaches or techniques such as a supply chain control tower and a strategy for continuous risk monitoring.
Supply Chain Control Towers
A significant investment for any organization, an effective supply chain control tower can provide organizations with the insight they need to understand how different functions across their supply chain impact each other. For example, a planner’s request to expedite shipment of a delayed customer order might conflict with the logistics team’s goal of reducing operating expenses. Intelligence from the control tower can show the potential loss of profit versus the cost of expedited shipping.
Control towers provide more than visibility. They also offer real-time intelligence needed to change processes and identify opportunities to build resiliency through different sourcing arrangements and contingency plans. Strategically designed dashboards can help procurement professionals compare planned and incoming shipments against consumption and inventory, and signal discrepancies between supply plan projections and current stock levels.
Continuous Global Risk Monitoring
It is also important for supply chain organizations to maintain continuous awareness of potential disruptions in their external environment.
When major disruptions hit, the difference in response time to activate contingency plans and move materials, sites, commodities and products as needed can spell the difference between success and failure for an organization. In line with the classic adage “time is money,” these response times do have a demonstrable impact on the total cost of procurement within organizations. Organizations that report the ability to respond to disruption within minutes spend $19.79 per $1,000 purchases on procurement, while those that take one month or longer to respond spend $23.32 per $1,000 purchases. This means, for example, that for every billion dollars in purchases, the slowest organizations will end up spending more than $3.5 million dollars above what the fastest-to-react organizations spend for procurement.
Next Steps
To improve your organization’s level of preparedness and resilience:
- Assess where you are on the maturity scale in terms of contingency plans, crisis response teams, and resilience strategy.
- Determine ways to move from reactive response to dynamic capabilities and embedded resilience.
- Incorporate tools such as supply chain control towers and active monitoring of global risk into your risk management processes.
By anticipating changes and disruptions and developing a contingency playbook, supply chain organizations can ensure their survival and competitive advantage in a world of ever-increasing risk and change.