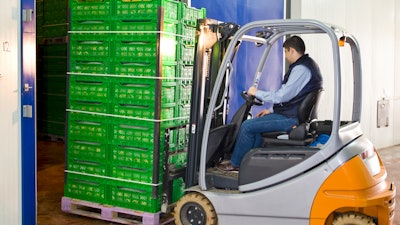
Large technology investments in your operations will almost always improve your efficiency, but if not done wisely, it may limit your flexibility and close doors that are better left open.
Before you open your wallet for that new state-of-the-art integrated picking system or expensive pick-to-light racking, consider simpler solutions first. Do your picking steps follow a “one and done” strategy?
5 Ways to Increase Warehouse Picking Efficiency
Work Flow = Efficiency
When designing a distribution center work flow, companies often profile their inventory based upon a linear pick scheme. They assume the assembly of the orders are processed by one team, through an ideal slotting scheme, based on pure product velocity. Often overlooked are crucial productivity inhibitors that can virtually cripple a work flow and prevent the full throttle of a large scale labor-force.
Consider heavily weighing the raw labor and traffic flow as an integral part of your inventory slotting and racking strategy. Fishbone theories of racking layout suggesting 20 percent improvement based on the labor component fuels the argument for this type of strategy.
Ask yourself key questions before designing a new work flow. Do you want more than one piece of equipment in a pick zone at a time? More than one picker? A picker on foot, in the same aisle simultaneous with a forklift truck? For maximum productivity and flexibility during peak seasons, the answer to these questions is a resounding yes.
Ground Control
Always slot maximum amount of SKUs in ground locations.
Your location velocity codes may say to put that “A” product nearest your docks in a forward upper level location, but think of the limitations that may result for the gain in proximity. Pickers using carts, transporters and hand jacks are immediately removed from the labor pool to draw from the upper level picks.
If you have temporary workers during peak seasons, they likely don’t use vertical equipment either. If you use all four basic pieces of equipment, you have limited 75 percent of labor options. Many times, floor locations, even at peak travel times and in the most remote zone of your facility, are the winning solution.
Consider the boost in raw labor with this strategy:
- Forklifts and their operators (likely your premium labor) become more available in a less congested area;
- Expansion of seasonal labor and temp worker (your most affordable labor) pick assignments;
- Simultaneous pick lines and zone picking, especially for your top products;
- Accelerated pallet to shelf bin replenishment for high velocity products;
- Expanded picking capacity for untrained second and third shift workers;
- Flexible ground level picks when conveyors, forklifts or computer systems go down.
Some operations that are labor intense and require a lot of individual product handling may consider not storing any products in elevated positions. Find what work flow best suits your company’s specific needs.
Always Put Safety First
Ensure forklift operators are sensitive to pedestrian traffic and balance the timing of their picking in these areas. Also consider spreading your velocity codes to a wider range. If you slot products too close, there may be insufficient space to allow simultaneous multiple waves of both workers and equipment.
Consider Conveying System Drawbacks
Beware the conveyor. Too often, large volumes of SKUs are placed in flow rack locations feeding to a conveyor pick, often using standard shelf sizes to maximize the cube. This is a great strategy but often backfires. Once you decide it's a conveyable pick item, you've engaged in linear picking with one order at a time being "throttled" through that pick line. You'll pick only as fast as your slowest picker.
This strategy may cause pick delays through zones, order backups and continual replenishment needs not being met. Often the better solution is a floor pallet pick at the beginning or the end of the pick line modules. This will streamline the work flow and may minimize the overall carton travel time and distance. You may be able to batch certain orders and induct cartons "mid-stream" with a redundant induction station for a select subset of SKUs. It will also minimize "in shift" replenishment.
If floor space locations are at a premium, consider clearing out the old maintenance dumping ground or the front office trans-files archive area. An "A" location is an "A" location in any area. Can you move any warehouse management offices into an elevated mezzanine area? Consider transitioning your most stagnant storage area into a high volume order picking module, or as I like to say, "Make your biggest weakness your strongest strength."
If only 5 percent of your orders can be completed with the top 10 SKUs, consider establishing an entirely redundant pick module for those SKU's. For larger scale operations, can a third redundant pick line work? A fourth?
Even on a seasonal basis, a second team of moderately skilled pickers can really boost your order cycle time performance. Again, avoid a "linear" or single treaded work flow mentality. Imagine major highways in your area during rush hour having only one lane open?
Worried about quality? What are the odds of even a new temporary working picking the wrong SKU when their pool is only 10 SKUs? If the products are seasonal, install some temporary skate wheel conveyors in front of pallets and have a senior picker drive the "speed" of the process by picking in the first zone. You may want a second seasoned person at the end of the pick line for a quick quality check before is goes to packing.
Improve Productivity, Reduce Costs
Here's a top 10 list for boosting your picking speed:
- Use end of the aisle floor space.
- Break floor pallet locations in "two" with a new cross bar or adding a second SKU vertically divided on a single pallet location. This will create a half-pallet floor pick creating more replenishment but will be more than offset by gains in picking productivity.
- Send emptied SKU cartons from the pick bins down the conveyor to avoid clutter. Have someone pulling and breaking those down at the packing or quality merges.
- Avoid re-handling. Pick into the shipping carton—not a plastic tote—and create a "one and done" pick process.
- Use in-line scales to perform quality control checks by product weight.
- Pre-label the ship cartons before you erect the carton or start the pick. They're easier to handle that way and maximize worker productivity while minimizing staging area requirements.
- After each zone is picked in a conveyor pick, continually rotate cartons on conveyors 90 percent to signal the completion of a workers picks within the specific zone picks to the next picker.
- Batch single picked orders to temporarily work zones in an unused or remote corner of the distribution center.
- Consider an in-line carton sealer and erector to boost the pick line speed.
- Maximize the use of casual labor to control costs.
Measure It
Challenge your team with some benchmarks before you start. Ascertain the percentage of SKUs you can now effectively pick with no power equipment. With a little imagination and team collaboration, see if you can't double that percentage. The long-term dividends are an easy payback. With a little teamwork and some simple changes, you'll be amazed at the productivity gains without breaking the bank.
Add Automation
If you're thinking it's time to add automation to your picking process, here are some additional resources as you start the journey.
Moving From Man to Machine
Automation Alleviates Labor PainHow Robots Are Changing the Food Industry And Improving Fulfillment
Wearables/Augmented Reality Software Boost Order Picking 25%, Pilot Test Shows
This article first appeared in Food Logistics in 2006.