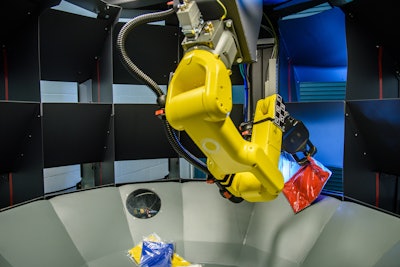
A warehouse is dependent on a smooth, effortless operation. In fact, the picking process can be the difference between success and failure, depending on how efficient it is. If you are worried about declining growth rates or waning productivity, there are a number of steps you can take to make your picking process more effective. Here are five:
Don’t Mix Numbers
If you use large bins for small items, it can be tempting to mix multiple small items in one single bin. Doing this can slow down productivity and lead to shipment errors, especially if the items are similar in size or appearance. It might save you some space, but it will end up lowering your efficiency.
If you have small items, make sure each individual SKU number has its own bin. If space is a concern, consider switching to smaller bins for the small individual pieces. You’ll have fewer errors and a more productive picking crew.
Be Smart About Placement
This is especially important if you’ve got a large warehouse. The last thing you want is to have employees walking from one end of the warehouse to the other to pick two single items. Be smart about how you organize your inventory. It might seem like a good idea to organize everything by SKU number, simply because it makes it easier to restock, but if you have a number of parts that tend to get ordered together, it might be a good idea to organize your inventory by sales rather than by SKU.
Pick the Right Racks
Picking the right racks for your warehouse is something that will depend on the needs of your particular warehouse. Floor racks are easier and faster to access for pickers on foot, while elevated racks might be easier for conveyer belts or automated picking systems. If you are planning to implement automated or robotic picking in the future, it might be a good idea to invest in elevated racks. If that isn’t in your plan, floor racks are a good alternative.
Invest in RFID
Radio Frequently Identification, or RFID, uses chips equipped with small antennas to track inventory location and position within your warehouse. This can help improve picking efficiency by giving your pickers up-to-date location information on the product that needs to be picked. This is extremely useful if you’re warehouse is large or has a lot of inventory that needs to be picked on any given day.
RFID is a useful tool for automated picking but it can also be paired with handheld picking techniques, as long as your pickers have a portable RFID scanner.
Use the Right Storage Medium
Take a look at your sales for the last six months. Do you have items in your primary picking areas that aren’t moving as fast as other items in more remote areas of your warehouse? Slower moving inventory should be used out of prime areas and replaced with items that are moving out faster to increase efficiency.
Picking efficiency is integral to any warehouse that uses manual picking to complete its orders. By changing the way your warehouse is organized, or lowering your picking racks to the floor, you can increase your efficiency and reduce order errors.