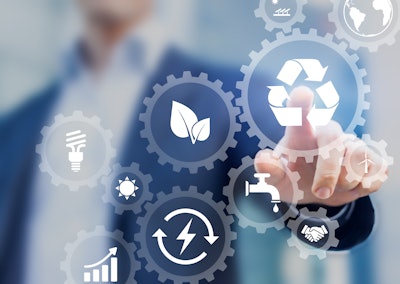
Logistics professionals know that energy represents one of the most significant operating costs. They also understand the importance of taking steps toward doing business in a more sustainable way, one that leaves less of a carbon footprint. What’s less obvious is that many sustainability measures can actually result in a decreased energy spend.
For energy-intensive industries like logistics and manufacturing, it’s important to have a strategic approach toward monitoring, managing, and ultimately, reducing energy usage.
Sustainability and efficiency: Where to start
When the goal is to reduce energy usage for either cost savings or sustainability reasons (or both), efficiency is the place to start. Operating with as little energy as possible should be every business’ priority.
Before investigating sustainability options like renewable or clean energy — including solar, green electricity or carbon-neutral natural gas — the most effective first step is to reduce overall energy usage. This is done primarily through efficiency upgrades and taking specific measures.
In order to get started with efficiency upgrades, you have to first understand your operations’ current energy usage. Before making any improvements, consider an energy audit or real-time monitoring solution to help benchmark usage. With the actuals and data from monitoring, organizations can more intentionally explore other sustainable technologies and options with their energy partner to create an effective sustainable energy strategy. This could mean buying grid power with renewable energy credits (RECs) or exploring solar. These decisions come down to what your logistics organization’s goals may be: operating more sustainably, saving money, placing long-term energy hedges or all of the above.
Understanding your usage
About half of an energy bill is driven by the energy demand — demand being the measurement of the largest interval of power used during the billing period. Meanwhile, consumption is the measurement of the total quantity of power used during the billing period.
The demand an energy customer is billed for is the peak amount of power used at any one time during the billing period in question. Since businesses aren’t charged for demand during the times when they’re using less than the peak amount, efficiency efforts typically result in savings by lowering the demand required to run your facility’s operations.
Start by reviewing a year’s worth of interval meter data to identify if the peak demand your business is being billed for happens often. If peak demand is infrequent, work with your in-house operations and maintenance partners to determine what equipment and processes are causing this demand.
Determining if on-site generation is right for your organization
If your organization is concerned with sustainability or operating with less of an environmental impact, it’s likely you’ve previously considered or discussed solar. However, determining if on-site power generation through solar is right for your business involves a nuanced conversation with various internal partners and ideally, with the support of an energy supplier who takes a holistic approach to the process and can view your business as a whole. There are several key things to consider before making an investment in solar.
First, consider the goals. If the primary goal is cost savings, it’s important to understand your food logistics organization's electric bills in general, specifically your demand charges. Depending on the market, solar may or may not offset all portions of an electric bill, and often the utility’s demand charge won’t go away even if a company is generating power on-site. In some cases, offsetting the energy portion of the bill alone can create savings, especially where there are state incentives or high energy rates. In all cases, think about on-site solar as a long-term hedge against rising energy rates.
Next, there’s site suitability. Is there a relatively new large, flat roof? Are there other spaces available on the property, like a large field or parking lot? Does your business want to own or lease the solar equipment? While a factor like site suitability can sometimes be straightforward, the conversation around owning or leasing equipment is more complex and involves tax incentives — and whether the business can benefit from them – which often makes financing solar through a Power Purchase Agreement (PPA) an attractive option.
If the outcome of the conversation is that on-site generation may not be the right option right now, it often makes sense for a customer to consider a green energy contract through a retail energy agreement bundled with RECs or community solar if it exists in the market. Green energy contracts can help organizations support renewable projects through the purchase of RECs and allow the organization to claim green power. Similar to a green energy contract, community solar enables customers to enroll and buy power directly from solar projects located somewhere else on the grid.
How to best control energy costs
The best energy strategy begins with a conversation around risk and therefore a business’ risk appetite.
In a volatile energy market, having a strategy designed to meet your business’ unique needs is essential for managing risk. It’s important that organizations work with an expert who has enough experience and expertise to truly understand the options available. From there, select the right product or products that align with your facility’s risk appetite and sensitivity to price fluctuations.