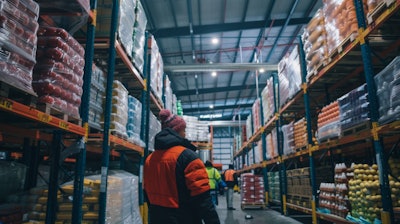
The cold chain is entering a transformative era. A global coalition of food and beverage manufacturers, cold storage leaders, logistics providers, and sustainability advocates have come together under a new banner called The Move to Minus 15°C.
The Move to Minus 15°C is a coalition seeking to update frozen food temperatures to drive efficiency across the cold supply chain and tackle concerns over food waste. Championed by organizations like Maersk, Lineage, Americold, and more, this movement aims to shift the frozen food industry-standard storage temperature from -18°C to -15°C.
These standards have not been updated in over a century and were never based on scientific data, leaving significant room for improvement. Originally, the -18°C benchmark emerged not from rigorous scientific analysis, but from early mechanical refrigeration capabilities and broad attempts to standardize around safety margins that technology of the time could reliably achieve. As equipment evolved, the temperature standard simply persisted, largely unquestioned.
Now, the movement for change is gaining momentum.
Why does a mere three-degree change matter? Because energy efficiency at scale saves significant costs and emissions. In pilot programs led by European retailers, switching to -15°C reduced facility energy loads by over 10%, with zero recorded compromise to product shelf life. These real-world trials underscore the viability of scaling such a change globally.
At its core, The Move to Minus 15°C is not just news of a technical adjustment—it's a bold statement about innovation, environmental responsibility, and the power of collective action. And as with all major transitions, success will depend on data, control, and operational intelligence.
The opportunity: Efficiency, cost savings, and climate impact
Three degrees of change may sound like a small adjustment, but it carries massive potential for energy savings. Research indicates that even 1°C increase in frozen storage temperatures globally can reduce energy consumption by roughly 2%, totaling over 8 terawatt-hours (TWh), more than the annual electricity consumption of many countries.
Consider this: if the cold supply chain adopts -15°C as the new standard across even half of its global footprint, the collective reduction in carbon emissions would be equivalent to removing hundreds of thousands of cars off the road. Lower demand also eases pressure on regional power grids, supporting broader energy resilience.
Additionally, reduced energy consumption directly translates into cost savings for operators. This can amount to hundreds of thousands of dollars annually for large distribution centers, not including the savings from streamlined monitoring, auditing, and reporting.
In an industry with tight margins and rising operational costs, the ability to significantly cut utility bills while supporting sustainability targets is a win-win proposition. At a time when food prices are increasingly volatile, these savings are not just welcome—they’re transformative.
Understanding the risks: Why robust temperature monitoring is non-negotiable
Of course, lowering energy usage by increasing storage temperatures is not without its challenges. As temperatures rise, even by a small margin, the margin for error narrows. What used to be a safe buffer is now tighter, meaning every degree—and every minute of downtime—counts more than ever.
Frozen food safety remains paramount, and any deviation from optimal storage conditions can increase risks to product quality, brand reputation, and regulatory compliance. Moving from -18°C to -15°C introduces an acute need for enhanced temperature monitoring and alerts.
As such, the frozen food logistics industry must invest in more sophisticated tools to track, alert, and respond to any fluctuations in temperature. More rigorous compliance checks will also be necessary to verify that quality standards are consistently met.
Solutions that unlock the move to minus 15
One of the most critical enablers of The Move to Minus 15°C is the transition from manual to automated temperature monitoring. Many cold storage facilities still rely on periodic checks or disconnected systems that can’t provide a holistic view of what's happening moment-to-moment. This is no longer sufficient.
Modern cold storage operations need automated, real-time data collection across multiple points throughout the facility—something traditional refrigeration control systems (RCS) struggle to offer. While RCS platforms are designed to manage setpoints and refrigerant flow, they often lack the granularity, and intelligence to drive decision-making at scale.
Holistic solutions can also integrate with existing warehouse management systems (WMS) to track temperature data not just room-by-room, but product-by-product. This enables seamless data sharing up and down the cold supply chain.
The Move to Minus 15°C is more than an operational tweak—it’s a signal that the frozen food logistics industry is ready to lead on sustainability. This movement is backed by data and supported by a growing, global network of advocates and technology providers.
Summary: Why the move to minus 15 matters for food logistics companies
· Food safety and trust: Tighter monitoring helps safeguard product quality and strengthens brand reputation.
· Energy and cost savings: Even modest temperature increases slash power use and reduce bills.
· Climate benefits: Cutting energy demand helps achieve carbon goals and supports resilience.
· Innovation: Modern platforms make the Move to -15°C feasible, saving time while improving outcomes.