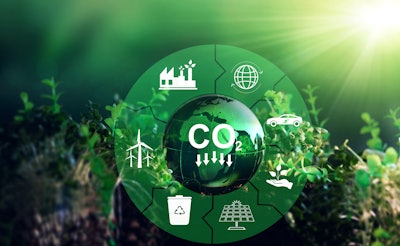
Companies in the cold chain use a lot of energy to keep food safe from farm to fork. Many are thinking about how to reduce their footprint, but food safety and throughput remain paramount.
Modern tools for cold chain facilities are helping some find the holy grail of operational excellence: increasing revenue while reducing costs. Blast freezing optimization, for example, can help companies increase throughput while decreasing energy usage and carbon emissions.
New energy management tools are helping food producers and logistics providers in 4 major ways:
● Optimize refrigeration equipment
● Maintain real-time temperature records
● Measure energy by customer and SKU
● Prepare for the electrification of trucks and TRUs
Optimizing refrigeration equipment
In cold chain facilities, refrigeration equipment is the obvious place to look for savings. Real-time equipment monitoring helps identify issues like overvoltage and compressor short cycling. Problems like these are easily addressed, which helps prevent early equipment failure.
It’s also now possible to continuously optimize coefficient of performance (COP). Some software tools can not only monitor COP in real time, but also send appropriate signals through refrigeration control system integrations to keep each compressor running optimally with minimal human intervention.
Similarly, operations with energy-intensive processes like blast freezing or high-pressure processing can analyze and optimize the amount of energy used relative to throughput. This type of analysis often improves space efficiency and idle time, helping increase throughput by 20% or more while reducing energy costs.
Maintaining detailed temperature records
Reducing energy is worthless without temperature control. Food safety is paramount for any cold chain operation, and any energy project that risks food spoilage is a non-starter. That’s why some operations are keeping detailed records using temperature sensors throughout the facility and at each dock door.
One common cost-saving project in refrigerated facilities known as “thermal flywheeling” involves pre-cooling the facility during off-peak hours and letting the temperature rise back to normal when electric prices are highest. This is only possible with real-time monitoring to alert managers of any temperature anomalies before things get too warm.
Areas closest to the loading docks are of course the most vulnerable to temperature spikes. That’s why some facilities are wirelessly monitoring the status of each dock door and alerting operators when a door is left open for too long. This not only helps maintain food safety, but also begins to create a culture of energy intelligence across the organization.
Measuring energy by customer and SKU
Most companies are now measuring their environmental footprint at the corporate level. Common KPIs for cold chain facilities include energy spend vs. budget as well as space and throughput efficiency.
Some operations are going further by submetering energy usage inside each facility, which makes for much more actionable data. In a few places, an even more useful form of energy management is emerging: understanding consumption at the level of each customer or SKU.
Through integrations with warehouse management systems (WMS) and other production systems, companies can disaggregate their energy and carbon intensity by product, customer, and supplier. This is becoming increasingly important as Scope 3 carbon reporting requirements cause companies to ask for data from others up and down the supply chain.
Relatedly, some food producers are separately measuring the energy and water usage of production, sanitation, and logistics. This helps plant managers and continuous improvement managers understand where to focus their efforts. Detailed, real-time information is simply more useful than a stack of utility bills.
Preparing for electrification of vehicles and TRUs
Another major wave of change is looming in the cold chain: the electrification of vehicles and transport refrigeration units (TRUs). These technologies promise to save money and accelerate decarbonization, but the coordination required between producers, carriers, and storage facilities can be daunting.
The coordination problem is made worse by a classic “chicken or egg” dilemma around infrastructure planning. Carriers don’t want to invest in electric vehicles until they know chargers will be available, and facilities don’t want to invest in chargers until they know they will be utilized.
Fortunately for cold chain operations, eTRUs offer a much easier starting point than electric trucks. And regulations in California and elsewhere are rapidly breaking the logjam by requiring carriers to begin electrifying 15% of their TRU fleet each year starting Dec. 31.
This means facilities in these areas have the certainty they need to begin installing eTRU shore power infrastructure at loading docks. And with the right tools, they can automatically bill carriers for the power they consume, generating new revenue while helping drive down costs and diesel emissions.
Once installed, facilities will need to monitor plug status so they can communicate their availability to carriers. The best way to do that is to integrate their energy management tools with WMS or other production systems. This has the added benefit of helping facilities avoid incurring excessive demand charges from the increased power consumption.
Beyond data: putting energy insights to work in the cold chain
It’s one thing to see real-time data. Experienced energy managers know how to leverage that data for best results, but many companies don’t have that kind of resource in-house. Today’s technology can help facility managers and operators understand exactly what actions to take and when.
For example, how can operators know when to start pre-cool a facility to avoid looming electricity price spikes? Monitoring energy markets in real time is out of scope even for most certified energy managers.
Fortunately, today’s technology can not only monitor grid conditions, but also consider each facility’s temperature profile and production schedule. Then it can alert managers to take appropriate actions that save money without impacting food safety or throughput.
In many cases, software can even automate these actions through refrigeration control system integrations so managers can act with a simple approval. Effective energy management doesn’t get any easier than that.