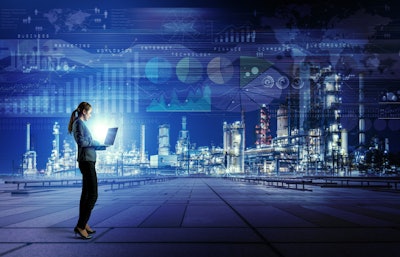
On Feb. 24, President Joe Biden signed an executive order, enforcing a 100-day review on all U.S. supply chains. This includes identifying risks for certain materials, software and pharmaceuticals. This includes reviewing transportation, production of agriculture commodities and food products. This includes assessing current domestic manufacturing workforce skills, climate change and critical goods. It also includes caring for the resilience and capacity of U.S. manufacturing supply chains.
In this 5-part series, industry experts detail the current risk areas in today’s U.S. supply chains, what should be done to address these issues, how this 100-day review will help U.S. imports/exports, address the downfalls of this 100-day review and what all of this means for the future of U.S. supply chains.
CLICK HERE to read Part 2.
Facing supply chain disruption
It was this time last year when the nation shut down as a result of the Coronavirus disease (COVID-19) pandemic. Schools closed. Restaurants closed. Offices closed. DMVs closed. And, consumers flooded the aisles of their local supermarket to stockpile frozen foods and toilet paper, of all things.
At this point, the virus itself created a slew of disruptions beyond the supply chain. We were experiencing every day disruptions, with work, school and life in general.
But, while we adjusted to this “New Normal” by hunkering down in our homes, our nation’s supply chains were in overdrive in order to pivot and eventually overcome these disruptions.
That’s because there are many risk factors consistently keeping U.S. manufacturers on their toes, according to Jim Bureau, CEO of JAGGAER. These risk factors include everything from economic issues and geopolitical tensions to natural disasters, supply and demand fluctuations, supplier financial health, consumer behavior changes and more.
“One of the best ways to secure supply chains in the face of all this uncertainty is to avoid sole source situations,” he adds. “Yet, the pandemic has shined a light on how reliant critical U.S. supply chains are on a small number of supply sources and on foreign suppliers. This vulnerability became clear last spring when the U.S. faced a severe personal protective equipment (PPE) shortage when China needed to divert its supply to address local needs.”
“Biden’s order for a review of vital supply chains should encourage companies across all industries to do the same,” Bureau says. “Today’s globalized supply chains consist of hundreds, even thousands of suppliers, which each rely on their own set of suppliers. One seemingly small issue, even several tiers down in the supply base, can have a tangible impact on an organization’s supply chain performance and ability to deliver. Review your critical points, dependencies and opportunities. Where are your vulnerabilities? What’s your plan for addressing the risk? Resilience starts with having the visibility, transparency and strategies in place to address supply chain risk in all forms, and quickly, effectively pivot when needed.”
COVID-19 also brought inventory control to the forefront of supply chain risk management.
“Some manufacturers have experienced severe demand spikes, supplier limitations or site shutdowns that have led to critical shortages of key parts, contract penalties and missed customer deliveries. Others have faced significant drops in demand that have led to inventory buildup and concerns over working capital,” says Richard Lebovitz, founder and CEO of LeanDNA, and recipient of Supply & Demand Chain Executive’s 2021 Pros to Know award. “One of the biggest contributing factors to these risks is a lack of total visibility into inventory due to disconnected and inconsistent information sources. A complete, global view of supply and demand data is foundational for optimizing inventory, collaborating with suppliers to address issues and making fast, confident decisions to manage inventory and delivery shifts when demand plans change. CLICK HERE to read Part 3.
“While the pandemic shined a spotlight on these inventory risks, any unforeseen event – economic shocks, natural disasters, geopolitical issues and more – can create similar disruption and ultimately negatively impact customer relationships and the bottom line,” he adds. “Business continuity during the health crisis and beyond requires a new inventory management model that combines visibility, accountability and actionability in the factory, which is where disruptions and opportunities come to life.”
During the pandemic, 75% of companies reported significant disruption in their supply chains due to a lack of visibility, says Michael Rabinowitz, founder and CEO, CoEnterprise.
“In fact, new data collected from our recent Twitter poll on supply chain professionals shows that 63% of respondents list ‘getting real-time visibility’ as their No. 1 priority to increase agility and resilience in their supply chain,” Michael Rabinowitz adds. “In today’s supply chain climate, lack of visibility certainly tops the risk list and is hurting the bottom line.”
And, yet, here we are, one year later, and COVID-19 is still impacting supply chains. Manufacturers are still struggling with rising costs, high demand, ensuring on-time delivery, investing in the right technology and continuing to hire, train and re-train employees.
“Traditional supply chain risk management does not monitor the changing risk landscape continuously,” says Atul Vashistha, founder and chairman, Supply Wisdom. “Instead, they rely on point-in-time assessments; the data from which is quickly stale and ineffective in mitigating supply chain risk and enabling resiliency. COVID also proved the need for continuous monitoring, as the rapidly evolving risk landscape made point-in-time data collected years or even months before the crisis virtually worthless in responding effectively to supply chain disruption risks. A lack of a continuous monitoring capability leaves supply chains at significant risk of disruption, as companies are left unaware of when their risk landscape changes, and are therefore, unable to take appropriate and most importantly timely risk mitigation actions.
At the end of the day, it’s what we don’t know that continues to challenge the supply chain. [CLICK HERE to read Part 4].
“We don’t know what we don’t know when it comes to our supply chains, including many for critical products,” says Julie Swann, an Allison distinguished professor and department head of Industrial and Systems Engineering at NC State University. “We have many risk areas in today’s U.S. supply chains. Our supply chains are global and interconnected; they can be vulnerable due to natural disasters like hurricanes, labor disruptions like the closing of a port due to a strike or nationalism.”
[CLICK HERE to read Part 5].