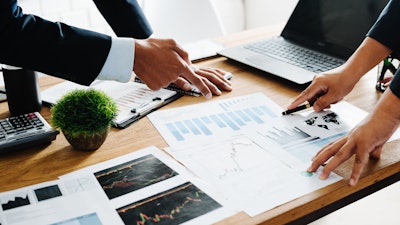
Over the years, executing a risk mitigation plan has transformed from something that’s nice to have to something that every company must have, at all times, in all facets of the organization.
From the influx of cargo theft, cybersecurity threats, food safety and driver shortage to geopolitical tensions, strikes from rail/dock workers, natural disasters and more, even the smallest gap can pose serious threat to people, product and plant.
Liken it to the blind leading the blind, getting lost in a maze or driving while blindfolded.
Not being able to see ahead and predict and plan accordingly is what sometimes plagues many of today’s supply chain companies.
That’s why mitigating supply chain threats is of utmost importance heading into 2024.
Marina Mayer, editor-in-chief of Food Logistics and Supply & Demand Chain Executive, talks exclusively with Stephen Dombroski, director, consumer markets, QAD, Inc., to detail why learning about, understanding and managing some of the lesser-known and publicized issues can contribute to a more resilient cold supply chain.
CLICK HERE to read the article in full.
Food Logistics: What are some of the cold food chains biggest threats to date? And why?
Stephen Dombroski: The process of storing and transporting perishable goods under controlled temperatures is known as the cold food chain. In today’s market, the cold food chain is facing threats that are impacting its operations and efficiency thus causing rippling effects throughout the economy. Here are some examples of those threats.
Compliance requirements and food safety regulations. Stringent regulations govern the transportation and handling of perishable goods to ensure food safety. Non-compliance can result in fines, legal issues, and damage to the reputation of the cold food chain. This can also lead to lost sales, poor customer service and destruction of the brand.
Disruptions and interruptions to the supply chain. Disruptions can occur due to various reasons such as natural disasters, geopolitical events, and pandemics. Interruptions in the supply chain can lead to delays, shortages, and increased costs for logistics and storage.
Temperature fluctuations. Maintaining the required temperature throughout the supply chain is critical for preserving the quality and safety of perishable goods. Temperature fluctuations can lead to spoilage, degradation of product quality, and potential health hazards. One of the toughest points of the supply chain is actually at the manufacturing stage when the product is in the work-in-progress stage. Product tends to be moved in and out of storage facilities for uncalculated amounts of times which can jeopardize cold integrity.
Supply chain disruptions. Disruptions can occur due to various reasons such as natural disasters, geopolitical events, and pandemics. Interruptions in the supply chain can lead to delays, shortages, and increased costs for logistics and storage. In today’s market, things that used to be major disruptions are now turning into more frequent interruptions that manufacturers and distributors need to account for as part of the daily operations.
Cargo theft. Perishable goods are attractive targets for theft due to their high value and demand. Stolen goods result in financial losses, and the compromised supply chain can lead to disruptions in the distribution of cold food products.
Driver and truck shortage. The transportation industry, including cold food logistics, have been facing a shortage of drivers and trucks for some time. Shortages can lead to delays in deliveries, increased transportation costs, and potential challenges in maintaining consistent temperature control. It is harder for transportation companies to find qualified drivers and with the need for next day deliveries of products, more LTL trucks are on the road leaving shortages of vehicles.
Geopolitical events. Wars, political instability, and geopolitical events can disrupt international trade and impact economies and affect how businesses operate. Disruptions in global logistics can affect the timely and reliable transportation of perishable goods.
Labor strikes. Strikes by rail, dock workers or specific industry work stoppages halt manufacturing, transportation and logistics operations. Delays in product distribution and potential spoilage can occur, leading to financial losses. If work stops completely, especially in certain types of cold chain facilities, operational restart is simply more than turning on the lights and starting the machines.
Natural disasters. Events like hurricanes, earthquakes, or floods can damage infrastructure and disrupt transportation networks. These types of instances appear to be more frequent in recent years. Disruptions in the supply chain, damage to storage facilities, and delays in transportation can occur.
Energy costs and sustainability concerns. High energy costs and increasing focus on sustainability may impact the cost-effectiveness of cold food chains. Increased operational costs can affect the overall profitability of cold food transportation and storage.
Technological risks. Reliance on technology for temperature control and logistics poses risks such as system failures or cyberattacks. Technology failures can lead to temperature deviations, data breaches, and disruptions in the supply chain.
Managing these threats is a huge challenge especially as they are fluid and changing. Addressing these threats requires a comprehensive risk management approach involving technology, regulatory compliance, risk management strategies, and contingency planning to ensure the resilience of the cold food chain.
Food Logistics: 2023 saw a lot of instability within the supply chain, such as geopolitical sanctions, natural disasters, inflation, etc. From your vantage point, how do these factors impact/influence the way companies can mitigate supply chain threats?
Dombroski: 2023 saw a number of issues that have made the cold supply chain very unstable. Now that we have the problems, we can begin talking about potential solutions or stop gaps to minimize the impacts of these issues. Some factors are predictable in the sense that there is always a threat for hurricanes, earthquakes and natural phenomena. Others are not predictable. In either case, the key to mitigating these risks is to have a risk management strategy in place with potential “go tos” or potential solutions that have already been worked into a “disaster plan” by rehearsal scenarios or exercises. There are a number of policies, practices and procedures that can be devised to be “at the ready” if need be.
Diversification of suppliers. Many areas of food manufacturing historically relied on the “good ole boy” network of suppliers. Many companies had a reliable set of a few suppliers whose agreements used to be a simple handshake so to speak. Today’s complex world is requiring changes to that philosophy. Disruptions are causing breaks in the reliability of those agreements and manufacturers in many cases need to find emergency supplies. Companies might consider diversifying their supplier base to reduce dependence on a single source. This can involve working with suppliers from different regions or countries to mitigate risks associated with geopolitical issues.
Risk assessment and management. Regular risk assessments are crucial to identify potential threats in the supply chain. This includes evaluating geopolitical stability, assessing the vulnerability of suppliers to natural disasters, and monitoring economic indicators to anticipate inflationary pressures.
The connected worker. There are a number of tools and processes that exist to help with improving machine usage and throughput. But very few of the systems in the areas of manufacturing execution really focus on the empowerment of the line worker. Having systems and processes in place to have the workforce informed and communicating better throughout the plant can seriously improve efficiencies and production as well as protecting the integrity of the cold chain. Building a skilled and adaptable workforce is essential. Employees should be trained in risk management, crisis response, and the use of relevant technologies to ensure a proactive and efficient response to supply chain disruptions.
Technology integration. Leveraging advanced technologies like artificial intelligence, machine learning, and data analytics can enhance supply chain visibility. Real-time monitoring and predictive analytics can help companies identify potential disruptions early on, allowing for proactive mitigation strategies.
Resilient supply chain strategies. Companies may adopt more resilient supply chain strategies that emphasize flexibility and adaptability. This can involve maintaining safety stock, having alternative transportation routes, and establishing contingency plans for rapid response to disruptions.
Supplier relationship management. Strengthening relationships with key suppliers is essential. Open communication channels can facilitate the exchange of information regarding potential risks and enable collaborative problem-solving when disruptions occur.
Strategic inventory management. Balancing inventory levels is critical. While holding excess inventory can be costly, having strategic stockpiles for critical components or goods can act as a buffer during supply chain disruptions.
Scenario planning. Companies may engage in scenario planning to prepare for a range of potential disruptions. This involves simulating different scenarios to understand their potential impact and developing response strategies for each. Dress rehearsals to manage through issues is always a good practice so when an emergency hits, you are ready.
Regulatory compliance. Staying informed about changes in regulations, especially those related to international trade and sanctions, is crucial. Companies need to ensure compliance with evolving laws to avoid disruptions due to legal issues.
Supply chain visibility platforms. Investing in supply chain visibility platforms can provide real-time tracking of goods and components throughout the supply chain. This visibility enables companies to quickly identify disruptions and make informed decisions.
The goal is to build a process that connects the entire ecosystem on the same operating platform to build a resilient and responsive supply chain. Regular monitoring and adjustment of strategies in response to changing geopolitical, economic, and environmental conditions are critical for success.
Food Logistics: According to multiple sources, the average value of cargo stolen during reported events in 2023 was $214,104, equivalent to an estimated $223 million in cargo across 1,778 reported theft incidents. What can be accredited to the rise in cargo theft?
Dombroski: There are several factors that might be contributing to a higher-than-normal amount of cargo theft.
Economic conditions. Economic downturns can lead to an increase in theft as individuals may turn to illegal activities due to financial hardships. Certain high-value products, especially food items are subject to counterfeiting. Manuka Honey being one such product. Black Market counterfeiting groups will find ways to scavenge food containers of high-end products and put lesser quality goods in the containers and sell them as the original. Then, repackage the original and sell them in other packaging for a premium.
Organized crime. Cargo theft is sometimes linked to organized criminal groups that operate strategically to steal and sell valuable goods and resell them on the Black Market.
Technology and cybersecurity. Advances in technology can sometimes be a double-edged sword. While technology can be used to enhance security measures, it can also be exploited by thieves who are increasingly sophisticated in their methods, such as hacking into tracking systems and mapping out plans for theft.
Supply chain vulnerabilities. The value chains for many products have expanded to such levels that product transportation nets are now wider that will expose more touch points for heists. Weaknesses in supply chain security, such as inadequate tracking, insufficient security measures, or lack of employee training, can contribute to an increase in cargo theft incidents.
Geographical factors. Certain regions or transportation routes may be more prone to theft due to various factors, including law enforcement presence, infrastructure, and overall security measures.
The market and the economy has changed dramatically over the last several years. High-value items have always been the target of theft especially at the cargo level. It is now to the point where it has expanded to the food industry for high value food products and the actual packaging that is associated with the items.
Food Logistics: Labor disruptions are also substantially higher this year, up 136%, according to Resilinc data. This includes company and site-level strikes, national strikes, layoffs and labor protests, among others. What does this mean for the future of cold food supply chains?
Dombroski: When you are talking about the operations of a supply chain, there are many factors that go into managing them. It starts with planning. Demand (forecasting), distribution, production, procurement planning functions. You need to have a plan in place. However, executing that plan is a different story. You can have the most accurate product forecast, the best distribution plan, the best capacity plan and have all your materials and ingredients ready to go. But, if there is a work stoppage at any of the touch points of that supply chain. Well, we can come up with many terms, many of which cannot be printed in terms of a result. When dealing with a cold supply chain, timing is everything because it revolves around perishability. So, in terms of the future, the more work stoppages that might occur, mean more disruptions which means more broken supply chains. In turn, companies can accept the fact that there will be problems and wait for things to happen or build a process to at least prepare themselves for ways to minimize the effects of a work stoppage. In addition to preparation, a number of issues might arise.
Preparations
Operational restart procedures. A work stoppage at any point of the cold supply chain will necessitate companies having procedures in place to restart operations. It is not simply a matter of turning the factory lights back on and restarting. There might be expired products on store shelves, in warehouses or in-transits that need to be dispositioned. Workers need to be ramped up. Production lines need to be ramped up. In terms of ingredients and raw materials, a company might be out of things due to expiration. So, an operation restart procedure should be in place.
Diversification of suppliers. To mitigate the risks associated with labor disruptions, companies may consider diversifying their supplier base. Relying on a single supplier or a limited number of suppliers increases vulnerability to disruptions. Having multiple suppliers can provide flexibility and alternatives in case of labor-related issues.
Increased automation. While labor can never be totally eliminated, companies may explore increased automation and technology adoption to reduce reliance on manual labor. This could include automated processing and packaging systems, as well as advanced logistics technologies that minimize the impact of labor disruptions.
Issues that may arise
Safety and quality of food. Cold food supply chains are especially sensitive to disruptions because of the need to maintain specific temperature conditions for food safety. If disruptions lead to delays in transportation or processing, there is a risk of compromising the quality and safety of perishable goods.
Supply chain disruptions. Labor disruptions can lead to delays and interruptions in the production and transportation of cold food products. If key workers are involved in strikes or are laid off, it may impact the ability of companies to meet demand, resulting in shortages and potential stockouts.
Increased costs. Managing labor disruptions often requires additional resources and contingency plans. Companies may need to invest in alternative labor sources, overtime pay, or expedited shipping to overcome delays and maintain the efficiency of the supply chain. These additional costs could potentially be passed on to consumers.
Company and brand damage. If labor disruptions are skewed more to a specific company than industry, persistent labor disruptions can harm the organization's reputation. Consumers may associate shortages or delays with poor management, and repeated disruptions could lead to a loss of trust in the brand.
Increases in labor disruptions pose challenges for cold supply chains, requiring proactive measures, strategic planning, and potentially a reevaluation of supply chain structures. Companies that can adapt to these challenges may be better positioned to ensure the resilience and reliability of their cold food supply chains in the future.
Food Logistics: What are some things not addressed above that may be pertinent to our readers?
Dombroski: There are several facts and challenges about the cold supply chain that might not be as widely known or published. Here are a few:
Temperature variability in work-in-process and temporary transit situations. Maintaining a consistent temperature throughout the entire cold chain is crucial. One area that often gets overlooked is the intermediate transit points of products that might still be in the work-in-process or value add stages. Ensuring the timely transfer to the proper cold storage units for products at all inventory levels is critical. Lack of superior technology to maintain, monitor and alert for temperature deviations throughout the process is critical. Moving something out of cold storage then back into a cold environment, even for the slightest temperature alteration could jeopardize product integrity.
Infrastructure deficiencies and energy dependencies. In some developing countries and regions, there may be inadequate infrastructure for maintaining a reliable cold chain. Lack of proper refrigeration facilities, transportation, reliable energy sources and storage can lead to significant losses in food quality and safety. Cold storage and transportation rely heavily on energy, primarily electricity. Power outages or disruptions can lead to temperature excursions, spoilage, and food waste.
Traceability. Ensuring the traceability of food products throughout the cold chain is essential for identifying and addressing issues promptly. However, some supply chains may lack robust traceability systems, making it difficult to track the origin and handling of food items. Technology is always being developed for better monitoring and the development of sensing devices in packaging and transport vessels and containers is on the rise.
Data gaps. Inefficiencies arise when different stakeholders in the cold chain operate with isolated or incompatible systems. Integrating data across the supply chain can enhance visibility and coordination but may require investments in technology and standardization.
Training deficiencies. Effective cold chain management requires specialized knowledge and training. Insufficient training among personnel involved in handling and transporting cold goods can lead to errors and compromise the integrity of the supply chain.
Packaging. Packaging is a hot topic especially around sustainability. While many advances in packaging have occurred to work toward sustainability, sometimes, the changes might impact the integrity of keeping items cold such as packaging thickness. It is important that all factors are considered in the development of packaging products that include sustainable aspirations as well as the integrity of the cold chain. Packaging plays a vital role in preserving the quality and safety of cold foods. Inadequate or improper packaging can result in exposure to external elements, compromise insulation, and increase the risk of contamination.
Learning about, understanding and managing these lesser-known and publicized issues can contribute to a more resilient cold supply chain. It requires collaboration among stakeholders, investment in technology and infrastructure, and a commitment to sustainable practices.
CLICK HERE to read the article in full.