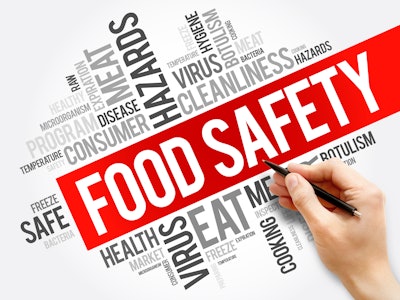
In a global market where counterfeiting and product diversion continue to pose serious threats, robust traceability systems are more important than ever. Looking ahead, sustainability is set to become a driving force, particularly as new regulations emerge, such as FDA Food Safety Modernization Act and the European Union’s Ecodesign for Sustainable Products Regulation.
Track-and-trace systems in beverage counterfeiting: Use case
The beverage industry includes two primary manufacturing categories: alcoholic beverages (such as wines and spirits) and non-alcoholic beverages (including soft drinks and bottled water). Among these, alcoholic beverages—particularly spirits—face greater risks of counterfeiting and diversion due to their higher market value. As a result, manufacturers have been increasingly implementing traceability systems.
One example of such a measure in Spain is the use of tax stamps on spirits, though not typically on wines. Some wineries, however, have adopted their own traceability solutions.
Challenge
The Spanish government introduced a new tax stamp format for spirits, replacing the previous version with one that incorporates a digital signature. This regulation, detailed in the State Official Gazette (BOE-A-2019-18747), mandates compliance from all spirits producers operating in Spain.
These updated tax stamps include QR codes that allow anyone—regulators or consumers—to verify a product’s authenticity via smartphone. Producers are required to quantify and report usage accurately, maintain up-to-date records, and submit documentation to the appropriate regulatory authorities in a timely manner.
Process and solution
- Requesting tax stamps. Producers must complete and submit Form 517 to the tax management office to request tax stamps.
- Verification and delivery. The tax office reviews the submission, verifies the requesting company’s credentials, and dispatches physical tax stamps either directly or to an authorized pickup location.
- Acknowledgment of receipt. Upon receipt, the producer must provide a formal acknowledgment of the delivery.
- Application of tax stamps. Stamps are applied to spirit bottles during the manufacturing phase.
- Tracking application. A system should record which tax stamps are applied to which products, capturing details such as lot number, bottle size, and product name.
- Reporting to authorities. Once a lot is completed, a report must be submitted to the tax stamp management system, including all relevant data.
Technical solution approaches
- Excel-based tracking. A manual method where a quality or production manager records the range of tax stamps used per lot in a spreadsheet. While simple, this approach does not track missing stamps during production.
- ERP integration. Enterprise resource planning (ERP) systems can log stamp quantities per lot, maintain centralized records, and facilitate data retrieval. However, they also do not detect missing or misapplied stamps.
- Dedicated software with physical equipment. A production execution system (PES) integrated with cameras or scanners offers the most robust solution. This setup verifies each applied stamp in real time, preventing issues such as overlapping or missing stamps. As the stamps have sequential codes, discrepancies can be immediately flagged and resolved.
Track-and-trace systems in food diversion and counterfeiting: Use case
The food industry encompasses a wide range of products, including baby food, fish, and cheese. Many of these items are sensitive in nature, and any compromise in quality or authenticity can result in serious health risks for both humans and animals.
One of the most notable cases highlighting the importance of traceability was the 2008 baby food scandal in China, where infant formula and other food products were adulterated with melamine. This incident underscores the critical need for robust traceability and quality control systems in the food supply chain.
Challenge
Products such as baby food require rigorous oversight of raw material quality, strict manufacturing conditions, and full supply chain visibility. Companies operating in this space are subject to intense scrutiny and frequent audits by regulatory bodies.
Process and solution
1. Raw material control. All raw materials are strictly monitored and logged into the ERP system. Each material can be traced back to its origin through associated purchase orders.
2. Controlled production environment. Manufacturing takes place in restricted-access zones with pharmaceutical-grade hygiene standards. Personnel must wear protective clothing, and the environment is tightly regulated. Serialization can be applied to each product during filling and sealing.
3. Aggregation. Products are aggregated into units such as cases or pallets to maintain traceability throughout the supply chain and reduce the risk of diversion.
4. Supply chain visibility begins. Finished goods are moved to warehouses where they are organized and stored. Pallets are prepared for shipping, and tracking begins at this point.
5. Transportation to wholesalers. Products are transported from company-operated warehouses to designated wholesalers.
6. International distribution. For example, products manufactured in the United States and destined for Asia are shipped to regional wholesalers in Asia.
7. Distribution to retailers. Wholesalers distribute the goods to retailers, supermarkets, or smaller shops.
8. Retail sale. Products arrive at retail locations and are made available for purchase by end consumers.
9. Customer verification. Customers can verify the authenticity of the product, typically by scanning a unique code printed on the packaging.
Throughout Steps 4-8, pallet-level scanning ensures continuous location tracking. At any point in the supply chain, a verification request can confirm both the current location and the authenticity of the product. This level of traceability plays a critical role in preventing diversion, detecting counterfeit goods, and maintaining consumer trust.
Conclusion
As global supply chains become increasingly complex, the need for robust traceability systems in the food and beverage industries has never been more critical. Counterfeiting, diversion, and quality control failures pose serious risks—not only to consumer safety and brand reputation but also to regulatory compliance.
Through the use cases of alcoholic beverages and baby food, we have seen how modern track-and-trace technologies—ranging from digital tax stamps to serialization, aggregation, and real-time supply chain visibility—offer effective solutions to these challenges. Whether mandated by government regulations, such as Spain's digitally signed tax stamps, or driven by internal quality assurance protocols in sensitive sectors like infant nutrition, traceability ensures transparency and accountability at every stage of the product lifecycle.
Looking ahead, sustainability and regulatory evolution, such as the European Union’s Ecodesign for Sustainable Products Regulation, will further shape traceability requirements. Companies that invest early in adaptable, data-driven traceability systems will be better positioned to meet these demands, protect their products, and build trust with consumers.
In a world where safety, authenticity, and sustainability are non-negotiable, traceability is no longer a luxury—it's a necessity.