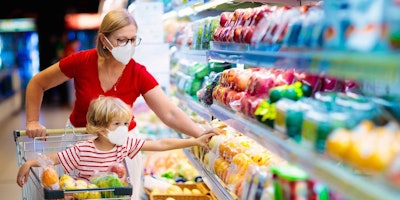
According to the Food Safety and Inspection Services (FSIS) annual report, in 2022 there were 45 recalls on 1,769,556 pounds of food. And, in that same year, the total number of units recalled by the FDA increased by 700%. As we reach the midway mark in 2023, product recalls are only continuing to grow.
Food is being recalled for a variety of reasons – from noted allergens and bacteria to contamination or mislabeled items. Some may speculate that these issues are nothing new, so why the rise in recalls?
The Food Safety Modernization Act, which was signed into law by President Obama in 2011, has shed a spotlight on product recalls. The law’s intention is to ensure that the U.S. food supply is safe by requiring preventative actions by manufacturers. Yet, despite the law, established more than 12 years ago, food recalls have continued to make headlines. Part of the reason is that manufacturers and the government have a greater understanding of scientific testing and tracing, which enables inspectors to identify food safety issues more quickly and accurately than previously possible. Additionally, new technologies, such as the Internet of Things (IoT), data analytics and artificial intelligence (AI) are also enabling manufacturers to collect and sift through more data more effectively than humans ever could.
But, it’s also because of the growth and complexity of today’s manufacturing sites, which make it easier for pathogens to spread. More and more companies are voluntarily recalling their own products as soon as a possible threat emerges. And, we can’t forget about the impact of social media and instant communication, which spreads the word about recalls much faster and broader than previously possible.
For the myriad ways product issues arise and are uncovered, once a manufacturer recognizes that a product recall is warranted, it needs to notify the FDA or Food Safety Inspection Service (FSIS) know as soon as possible and provide a plan of action on how it will handle the recall. The corrective action process is crucial to how the company will overcome the issue, but also to ensure that it never happens again.
Corrective and preventive action plans, by their nature, start as a reaction to an issue. The process allows a manufacturer to understand what happened and prevent these issues from recurring, reducing the need for future recalls. Below are considerations for building an effective corrective action strategy.
Identify and articulate the problem. Creating an effective corrective action plan begins with an accurate and descriptive problem statement. Getting the problem statement right will help orient everyone toward the right solution as well as help to validate it once it’s implemented. In the statement, it’s important to be concrete about the who, what, when, where and why of the problem. Additionally, it’s important to provide context and definitions of unclear terms to better communicate with upper management, along with clear verification criteria that will help the team evaluate whether the problem is actually fixed at the end.
Determine the root cause. People often take the “check the box” approach to corrective action, and nowhere is this more problematic than root-cause analysis. Effective root-cause analysis is essential to actually fixing the problem, and it’s not helpful just to attribute everything to operator error or inadequate employee training. Customers see through this, and many won’t accept weak solutions like informing operators and shift leaders of the correct protocol. Instead, you need to ask deeper questions. Is the process moving too quickly, leading to mistakes? Do you have proper error-proofing procedures? Is there something making the process overly complex?
Set deadlines. Due dates on corrective actions can be somewhat arbitrary based on the person assigning them and/or company policies about how long they should take. As a result, many quality managers assume they need to deal with those that have been overdue the longest. Yet, the top priority needs to be mitigating quality and safety risks. By adding risk assessment to open corrective actions, you can quickly find the problems that represent the greatest risk of recurrence or potential consumer impact.
Assign ownership. Essential to your corrective action plan is asking who will be responsible for seeing the process through to completion. Critical questions to ask include: will it be the same person responsible for each step, or shared among multiple individuals? Who will monitor progress, and who needs to be notified if problems arise with completing the request?
Who is responsible for verifying the effectiveness of the corrective action and signing off on it?
Quality management systems (QMS) or environmental, health and safety (EHS) management systems can help to streamline this step, with dedicated workflows for different categories of corrective actions and their owners.
Monitor effectiveness. A key step to ensure your corrective action plan will actually work is asking how you will judge effectiveness. Missing this critical step could mean closing out a corrective action before the problem is truly solved, allowing the root cause to persist unchecked. It’s important to re-examine the problem statement and compare the results against the criteria outlined. And, a final risk assessment can show if the corrective action has lowered risk to an acceptable level.
There’s no magic panacea to eliminate the need for food product recalls, yet by taking a strategic approach to corrective action plans, food manufacturers can learn valuable lessons to avoid them in the future.