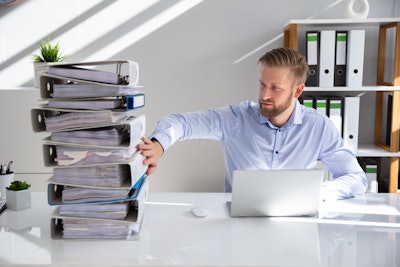
Approaches to food safety controls have changed significantly over the past century. Starting in 1905 when Sinclair’s The Jungle was first published, multiple federal government actions have been taken to improve food safety in the United States, including NASA and the origins of HACCP in the 1960s, the start of a “Food Safety Culture” in the early 1990s, and more recently, the enactment of the FDA Food Safety Modernization Act (FSMA) in 2016. The food industry has evolved from a predominantly “reaction and response” approach to one that now emphasizes “proactive prevention.”
As the latest evidence of this evolution, the FDA’s blueprint for a “New Era of Smarter Food Safety” is pushing the industry to become more agile and adoptive of technologies. The blueprint also provides food manufacturers with flexibility in how they continue to improve their food safety management systems.
Environmental monitoring programs (EMPs) provide a good example of the benefits that food manufacturers can realize through these evolutions. In stark contrast to paper-based test results or the use of spreadsheets, many in the industry now leverage automated EMP testing to learn from results more efficiently. The latest step in this evolution is a digital transformation wherein some food manufacturers are improving their EMP practices by using advanced, connected automation and “smart data” technologies, such as a fully automated, cloud-based EMP workflow and dashboard-driven analytics solutions that automate everything from testing schedules to corrective actions and the reporting and analytics required for audits and inspection. Solutions such as these are becoming generally available today and have been adopted at hundreds of food producers that have decided to become more transparent with their role in food safety within the food supply chain.
The advent of this digital transformation is creating change and change always comes with benefits and risks. For a validated and sustained EMP implementation, the introduction of technology and automation must maintain the integrity of testing and sampling methods. Food manufacturers must also consider the risks that can been introduced or shifted when technology is used to automate and digitally transform existing practices. The following are some important guidelines for organizations to consider when evolving their EMP to a more digitized and automated state:
1. Consider the risks associated with any technology device
Different types of risks are associated with technology use. Hazards associated with technological tools must be considered and analyzed along with other steps in companies’ production lines. The use of electronic devices to collect data and records on-site, such as an ATP scanner for example, begs a few questions:
· How do food safety professionals keep devices sanitized to pose no risks to the product?
· How is employee access to the devices controlled?
The devices should be considered as part of a utensils and equipment management program to ensure they are preventively maintained for potential hazard contaminations. Utensils and equipment management encompasses a safety and testing protocol for all items that are brought onto a production floor, including any technology devices such as tablet PCs, or food safety testing scanners, for example.
2. Maintain the authenticity and integrity of records
When maintaining records collected using digital technology, consider the following key questions:
· How will authenticity and integrity be tracked and maintained, and by who?
· Who took the records and when?
· What are the records for?
· Where are the stored?
· How are the accessed, and by who?
These are the same questions that must be answered with traditional methods and organizations must ensure that the technology can offer the same level of audit-ready records while maintaining the security and integrity of the data itself.
For test report verifications, meeting regulatory compliance works the same way too, as only a different tool is now being used. When using technology, the integrity of records cannot be compromised, and EMP technology providers should be able to prove they produce an audit-ready source of records with verified integrity for both accuracy and access control.
Click here to hear more about authenticity technology in the supply chain:
3. Secure data with proper sharing and transparency practices
Transparency, how to share data, and whether the data is kept secure while using new technologies are critical topics in the digital transformation of the industry. Internal practices should be considered first to ensure a robust security system is in place to protect the intellectual property, which could be challenged and reviewed in a pre-set frequency that fits the operations.
For example, data security can be considered in a company’s food defense plan and be challenged at least annually to catch the near misses. Nowadays, technology providers also provide supporting services to help you ensure an organization’s data is securely stored.
4. After a new technology is deployed, an overall “preventive maintenance” review is always helpful.
A preventive maintenance review can help a facility minimize unexpected incidents. Similar to the management of equipment used in production, stay on top of all tools, software or data platforms used and ensure they are updated to the latest version.
A brief analysis should be conducted on a regular basis to ensure that the integrity of the environmental monitoring program is not compromised. When an EMP is implemented, it is crucial to define sampling methods and locations according to the pre-defined testing frequency. When a technology is involved, companies need to ensure that the platform is reflecting their environmental monitoring practices precisely. A periodic review on what was done and what’s been digitally documented can help ensure that a “smart tool” is supporting food manufacturers in capturing all of their environmental monitoring activities accurately and in time.
Questions to ask a technology provider are:
· Does your solution allow customizable policies and practices as rules within the system?
· Can the system verify that policies and practices are being followed by system users?
Regardless of what approaches organizations use for their EMP, the foundation for how to prevent hazards remains the same. Food safety requires a “Herculean Effort,” an enormous amount of work, strength and courage. Technology is just one of the tools food manufacturers can use to assist in this critical work and support efforts to control food safety. By providing the potential for accelerated visibility and reaction to issues, technology enhances the industry’s ability to meet this overall goal.