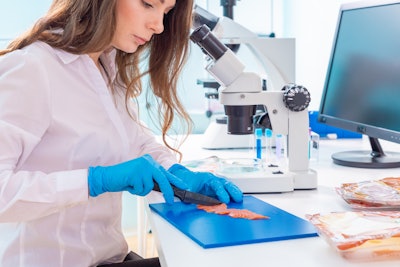
February marked the 30th Anniversary of the start of the ground campaign for Operation Desert Storm. While a Gulf War milestone may not seem directly connected to the food processing and logistics industry, it did bring me back to when I was a 19-year-old Veterinary Food Inspector (91R) in the Army during the Gulf War.
The early 1990s was an amazing period of time, with the world on the cusp of a new era in technology. In the Army, we were just getting into the digital age, using high-speed (2,400 baud) modems. We could place an order “online” and then it would show up at its destination, hopefully meeting specification.
With more than 30,000 soldiers in the system, the daily feeding supply line was tenuous at best. I was the last inspection point prior to troops eating. We received rations from logistics bases (later in the deployment) or the port, who received them by ship, or in rare cases, air transport. The “technology” at my disposal was a dial thermometer, wrench to calibrate it, two inspection stamps and a notebook.
Yet, the process was anything but simple.
The Department of Defense — via Army Food Inspectors — performed inspections at each step in the process on the home front or required proof of inspections. We were still using World War II/Cold War-era strategies and executing against those guidelines. We believed it was better to stop something defective while it was still on U.S. soil before going through the trouble of shipping it to the sands of Saudi Arabia.
Fast-forward to the present civilian food supply chain. The concepts behind the movement of food to market, in its basic form, hasn’t changed. Nor has the concept of production of food products. What has changed though is the science and technology, from the variety of ways companies can monitor in the field to electronic vision inspection, x-ray, automated probes, etc. The amount of data that can be pulled together about a product at any point in the supply chain today is pretty amazing, yet overwhelming.
Food processors and logistics providers have the ability to track product from ingredient to end user. On the meat industry side, they can track every cow in this country from the time it was born to the steak on the plate. The real question though is, are companies really taking advantage of food safety technology?
In most cases, “sort of” is the answer. You can ask a supplier about the safety of its raw materials, and that supplier will often provide documentation or mention its “program,” “HACCP” or how they processed it, etc. But, does the supplier really know?
Most will say the audit assures food safety. But, the real answer is often, no, they do not know. The trouble with audits are that they occur semi-annually at best. What happens when the auditor isn’t there? The auditors don’t follow every shipment; they only check a statistical percentage.
The thing is, even with all the technology available, you have to include the tried-and-true inspection methods of the past. You must have eyes on the entire process, just as we did in the Army. We fed well over 1 million men and women 30 years ago with very few issues concerning food safety. Since those days, we have discovered that even if we inspect product every step of the way, bad product still gets through, and even if we audit companies on a routine basis, we often get the same negative result. Imagine if there were no eyes on the product.
Do you know your farmer, your pre-processor, etc.? While it sounds kitschy to some and maybe preposterous to others, having this relationship and knowledge assures your products are safe. You don’t have to spend enormous amounts on audits, nor your limited human resources on second-party reviews. Each of those steps in the current chain collect more than enough data to verify safety of the products you receive. The key is creating secure ways to get access to that data.
Unfortunately, there appears to be too much emphasis nowadays on what happens “under my roof,” and not enough on what is happening beyond the walls. Take, for example, certificates of analysis. A product is harvested, tests are performed and the results go up one step of the food chain at best. They simply don’t get passed on from there. If your suppliers only send you their own test results, do you really have the entire picture? How can you tell what is really going on with the raw material you are using if you have 5-6 of the steps in the supply chain vs. all the steps from beginning to end?
Additionally, technology is great, but there is no standard for how these machines communicate with each other, link together and provide all information to the end user in a secure manner.
Thirty years ago, communication is what made the Army’s supply chain work. If there was an issue, I sent it via the Division to the Corps to Theatre Army HQ, who then sent an answer via reversed chain in a day (depending on how important it was). That gave me the ability to recommend feeding or bypass the product in an efficient manner. I had 30,000 other soldiers counting on me, and we got it right. Can you get answers to your questions in a day? Would you know if someone changed a process several steps back on the chain, materially affecting your product? You need this old-school approach of knowing about each step, but you can use modern-day technology to help resolve the challenges of receiving and analyzing that information.
The “eyes-on” approach will allow you, during quiet times, to achieve a forward-deployed mode in the supply chain.
Then, when a major supply chain disruption happens, such as the Coronavirus disease (COVID-19), a trade war or any other disruption to the chain, you would be ready to power up the supply line. Leveraging technology helps you and your company prepare for both. But, you must know and understand your entire supply chain to make that work.
All members of the food supply chain must become more proactive in these efforts. That doesn’t mean giving up trade secrets; it means setting standards that are universal and applying them to the new technology available today. All this wrapped up in the ability to rapidly see product data up and down the entire supply chain allows all links in the supply chain to have eyes on the finished product.