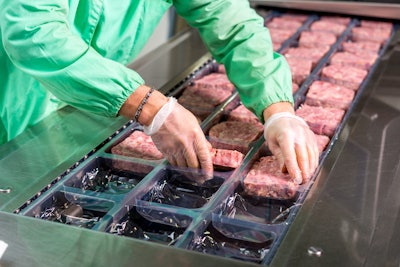
In today's rapidly evolving economy, the food manufacturing industry in the United States finds itself grappling with a multitude of intricate challenges. As the world around us changes, addressing these challenges requires a proactive approach that comprehensively evaluates cost inputs across all operational aspects, particularly within the sprawling supply chain.
The backdrop for these challenges is painted by macroeconomic factors, with inflation reigning as a significant player, creating cost pressures for food and beverage manufacturers and reshaping consumer spending habits. The situation is compounded by an array of supply chain concerns, and in response, many companies are resorting to price increases, shifting the added costs onto consumers to maintain their margins. While this may protect profitability in the short term, a more sustainable approach involves proactive cost evaluation.
Manufacturers are faced with the daunting task of maintaining profitability while finding a price point that is still digestible for consumers and doing so at a time when supply chains are being affected immensely by economic uncertainty, climate change, geopolitical events, R&D, and labor-related costs. It's a delicate dance that requires foresight and innovation.
Consumer habits – Consumption and sustainability
The echoes of inflation and its subsequent impact on consumer spending are undeniable. A telling statistic is U.S. food prices rising by 6.7% over the past year. Yet, as inflation inevitably slows, the budget-friendly habits adopted by consumers are here to stay. Consumers have become more selective in their purchases – leaning toward lower-cost brands and purchasing less – resulting in lower volume demands for food manufacturers and potential increases in cost-per-unit.
Simultaneously, the push for sustainability by consumers and investors alike is driving food and beverage manufacturers to invest in eco-friendly practices such as sustainable packaging solutions and sustainably sourced ingredients. However, these options often come with higher costs. Incorporating biodegradable and recyclable materials and sourcing sustainable alternatives, such as plant-based meat products, requires specialized sourcing and processing, which makes it costlier for food manufacturers.
This shift to sustainability, though crucial, often puts a strain on manufacturers’ budgets. The technology behind these innovations is also still evolving as consumers and companies alike want to make the investment, but no one knows quite how to perfect it yet, so the R&D investment alone can be an expensive cost for manufacturers. Therefore, it’s a balancing act for companies striving to align with consumer preferences while safeguarding their bottom lines.
Climate change – Supply and delays
Furthermore, the impact of climate change on the food supply chain, as exemplified by extreme weather events disrupting the availability and delivery of both raw materials and finished products, also affects manufacturing costs.
This summer, an unprecedented and prolonged heatwave across the country brought intense heat and drought to various parts of the United States, which severely affected crop production, particularly for Midwest staples like corn and soybeans. Additionally, severe weather events like Hurricane Hilary have left many farmers concerned about crop production, especially as hurricane season begins to pick up for the United States.
Heatwaves and drought have also caused intense disruptions across the transportation and logistics networks as hundreds of ships were run aground when the Mississippi River and Panama Canal reached record lows over the last year. These supply chain disruptions made it more difficult for manufacturers to transport efficiently which further compounded cost increases, and ultimately led to delays in getting products to market.
The vulnerability of the industry to climate-related issues has food manufacturers urgently seeking new ways to adapt to climate changes and finding mitigation measures to ensure the resilience of their operations and maintain a stable and sustainable food supply.
Geopolitical uncertainties – Trade and availability
Meanwhile, geopolitical events introduce a further layer of unpredictability. Russia’s invasion of Ukraine has had a cascading effect on the global grain supply chain. In July 2022, the Black Sea Grain Initiative was negotiated between the United Nations, Tukey, and Russia to ensure that grain, including wheat and corn, could be exported from key Ukrainian ports in the Black Sea. However, since Russia announced its decision to walk out of the deal in July of this year, global wheat prices have risen by more than 8%.
Not only has the expired initiative impacted prices, but the supply disruption is felt on a global scale, impacting the availability of crucial ingredients for food production around the world. The unpredictability of the grain market has left manufacturers reexamining their production and distribution costs along with global trade dynamics.
Labor – Shortages and automation
Another factor is the growing scarcity of skilled workers, as labor shortages remain a significant challenge across the supply chain. An increase in efficiency for some areas of the supply chain coupled with a shortage of skilled labor in others, leads to the situation where products end up going to waste. A notable example is dairy farmers in the Midwest finding themselves dumping fresh milk because the processing plants are over capacity between labor shortages and the increase in fresh dairy production.
Additionally, retaining and obtaining skilled workers can be expensive, especially as manufacturing industries face labor shortages and negotiations with many workers demanding higher wages due to increased demand and changing labor laws.
Furthermore, inefficiencies in labor are a significant source of added costs due to the misallocation of budgets to unnecessary or redundant processes that ultimately take away from production. While automation, data analytics, and artificial intelligence (AI)-driven systems offer solutions to streamline operations and enhance productivity, many manufacturers still underutilize these technologies. The cost of hiring and maintaining workers is not solely in wages but also in the missed opportunity to leverage technology for cost-effective and precise processes. If a company can lower allocated labor costs, it can significantly impact revenue and keep product prices down.
Proactive cost optimization solutions
To safeguard against the ripple effects of these challenges, food manufacturers must embark on a comprehensive evaluation of cost inputs. This entails scrutinizing both direct and indirect costs, from raw material sourcing to back-office operations. By identifying and addressing inefficiencies, manufacturers can enhance operational efficiency, maintain margins, and keep consumer prices in check.
Efficiency gains can also be achieved through supply chain optimization and automation. Effective supplier relationship management and streamlined logistics can trim operational expenses, allowing manufacturers to weather disruptions with greater resilience. Furthermore, investments in automation technologies can enhance productivity, mitigate labor shortages, and reduce costs over the long term.
Ultimately, as the U.S. food manufacturing industry navigates these cost-related challenges, a proactive stance is essential, and manufacturers must evolve beyond passing price increases onto consumers to protect their margins. By reducing costs strategically, manufacturers can maintain healthy margins and keep prices within the reach of consumers and keep them from trading down to other brands. This strategy secures immediate gains and positions companies as industry leaders in the long run. The choice is clear: act now to navigate these challenges as the system is already on fire, and facing these costs head-on is your competitive advantage.