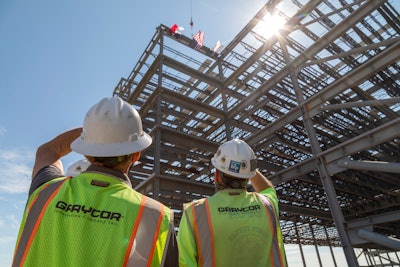
Although the food and beverage industry continues to face supply chain issues ranging from labor shortages to transportation and even disruptions attributable to natural disasters and extreme weather, overall there have been some positive indicators.
McKinsey reported "since 2019, the [grocery] market has grown at an impressive 15%.” The U.S. Department of Agriculture (USDA) says “there are currently no nationwide shortages of food,” pointing out that the avoidance of widespread disruptions is due to “food production and manufacturing [being] widely dispersed throughout the U.S.” However, this production and manufacturing capability relies on a network of built infrastructure that is itself encountering supply chain and cost challenges.
There has been no reduction of new construction starts in the food and beverage market; in fact, a multiplicity of market changes is driving increased demand for facility new-builds, expansions and modernization. Chief among the changes are a pandemic-fueled increase in at-home food preparation and a rise in the consumption of packaged goods. Fresh food delivery, farm-to-table movements and ready-to-eat (RTE) goods are reshaping the market. “Ghost kitchens,” or commercial spaces that prepare food for home delivery rather than investing in storefronts or dining rooms, are also changing the food consumption landscape. Broader consumer-driven trends include the push for greater sustainability and lower carbon footprints in all types of structures. Additionally, facility designs must respond to a heightened interest in cleanability and the separation of production lines to reduce contamination risks. All these factors and more require food processers and suppliers to invest not only in more square footage, but also in different types of manufacturing, storage and picking/packing equipment.
Completing construction on time and on budget requires rethinking business-as-usual because competition for labor and materials is intense. The large volume of under-construction space was highlighted when Commercial Edge reported “the industrial construction pipeline stood at 640.1 million square feet nationally, accounting for 3.7% of the existing U.S. industrial stock.” For food facility construction, the most volatile commodities continue to be metals (both rebar and structural members), mechanical equipment, piping, electrical equipment and conduit and wiring. The volatility can be attributed to the fact that these materials touch every discipline in every market. Shop constraints are a major consideration as well, since current shop hold times are typically only 1-2 weeks at best, and commodity pricing holds are often current pricing only. In addition to material availability and shop constraints, product transport is also becoming strained, adding another layer of availability concern.
Owners are seeking to exert greater control over the value chain, collaborating with industry partners for more robust pre-construction planning, as well as becoming more involved in procurement decisions. Early planning, especially assisted by early contractor involvement (ECI), translates to early commitment for critical materials and equipment, while the collaborative approach ensures that design-phase decisions are coordinated to fit with actual products ordered. Additionally, general contractors contribute in-depth understanding of long lead items as well as material availability and pricing. Often these contractors have strong relationships with vendors, sub-contractors and suppliers, enabling the team to improve hold times based on a letter of intent.
An excellent way of mitigating supply chain issues is by running various construction scenarios and balancing competing considerations across the entire building timeline. The owner and their team should weigh availability issues with other concerns such as safety and quality. For example, choosing bolts over welding reduces variables that can affect quality, resources and supply chain issues. This is because bolts are generally simpler to install, requiring nothing more than a high-quality initial product and proper torquing procedure. Welding, on the other hand, requires significantly more material control (such as weld rod oven temperature control and segregation, control of weld gases, weld machine calibration, etc.) and welders must have skills that require testing and certification. Welds also typically require some form of non-destructive testing, depending on the applicable design code. An additional benefit of the example of bolts vs. welds is that the reduction in special training or skillsets opens up the field to a larger resource pool, mitigating workforce shortage challenges. Project-wide, there are many similar designs elements that can be selected to reduce the need for special training or skillsets.
Because modern food facilities employ some of the most sophisticated automated and robotic solutions available, pre-construction activities should devote adequate time to understanding how a given set of equipment will impact facility layout, utility and energy demands and more. Owners and design partners should work with original equipment manufacturers to understand the needs of proprietary equipment.
Technological tools, while no longer a novelty on most jobsites, will only be fully optimized if all team members are aligned and invested in their collaborative use. Products ranging from construction management software to drones to light detection and ranging (LIDAR) can improve communication, data collection and tracking. Building information modeling (BIM) remains one of the most useful technologies. If utilized early in the design process, BIM can assist in standardizing material sizes and configurations, as well as incorporate constructability or material changes that align with supply chain availability. Use of BIM can allow the team to make more efficient use of early order placement, taking advantage of material availabilities or offsetting long lead times.
Safety, quality and efficiency risks are inherently greater for field fabrication than for controlled shop settings. For this reason, pre-fabrication and modularization can help mitigate field resource availability, including the construction labor shortage. However, prefabricated items require more up-front design time to support procurement, so preconstruction activities should examine timing issues surrounding material and shop availability constraints.
ECI is a foundational strategy for alleviating supply and cost constraints and improving project outcomes. With this collaborative approach, the team can weigh all project variables and run informed scenarios to help identify the most efficient and cost-effective approach to a given problem. They can also make considered use of available technologies.