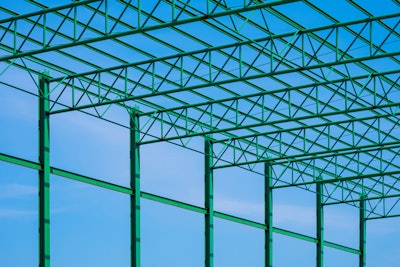
The planet is more vulnerable than ever, according to the World Health Organization (WHO). Climate change is directly contributing to devastating disasters like wildfires, floods, heatwaves, and hurricanes and are only increasing in scale, frequency, and intensity. Research shows that 3.6 billion people are already living in areas highly susceptible to climate change. Global leaders are calling for everyone to help by reducing electricity use, reusing items, and protecting the environment—from forests to oceans and everywhere in between. This mission has put stress on companies to assess their products, practices, and infrastructures to identify areas for sustainability improvements and implement actions to reduce environmental impacts. Leading companies are already turning to solutions like automation to help improve greenhouse gas emissions through better transport options and reduced food and energy waste.
In fact, automated warehouses offer a number of advantages to improve sustainability. They optimize energy consumption for more efficient processes and enable precise inventory management to prevent overproduction, reducing waste and conserving resources. In addition, automated systems often require less space, which minimizes the need for additional warehouse space and enables more sustainable use of existing facilities. While implementing automation within warehouses is undoubtedly making an impact on improving sustainability, many companies are unaware that the materials used within their infrastructures can actually be setting them back from reaching their sustainability goals.
Steel vs. green steel: A sustainable alternative
A common material used in today’s warehouses is steel. However, traditional steel production involves the use of coal which is burned to create the high temperatures needed for smelting iron. This process results in significant emissions of greenhouse gasses including carbon dioxide and methane, and pollutants like sulfur dioxide and nitrogen oxides. The production of steel accounts for about 7% of global greenhouse gas emissions, making it a major contributor to climate change. Additionally, traditional steel production contributes to a significant amount of waste. The process of refining and purifying the iron for steel creates a large amount of slag and other waste products, which can contaminate nearby soil and water sources.
As the second most commonly used building material next to concrete, steel is a highly sought after material. But, because steelmaking involves processes that release carbon dioxide into the environment, many are exploring sustainable methods like green steel—an innovative manufacturing process that uses hydrogen or electric arc furnaces (EAF) instead of fossil fuels to create.
According to Fortune, the global green steel market is valued at $3.75 billion in 2024, a number that is projected to increase to $129.08 billion by 2032. Currently, North America is dominating the green steel market with a market share of over 60%.
A climate-neutral, or low CO2 emitting material, green steel can significantly help companies around the world reduce environmental impacts. Whether building a new warehouse or integrating into an existing infrastructure, green steel has many benefits including:
- Reduced energy and emissions
Green steel production methods, like hydrogen, cut CO2 emissions compared to traditional steelmaking processes. By incorporating green steel into construction, warehouses can lower the overall carbon footprint of their buildings from the ground up, contributing to more sustainable infrastructure. Further, structures built with green steel often feature better energy performance due to advanced manufacturing techniques that can optimize insulation and structural design, reducing heating and cooling energy needs.
In addition to reducing carbon footprints, green steel is produced using renewable energy sources and minimizes waste during the production process. This approach not only lowers overall emissions but also supports a more sustainable and resource-efficient manufacturing cycle. By harnessing renewable energy, like hydrogen, green steel production decreases the reliance on fossil fuels, while improving production techniques and technologies, contributing to a cleaner and more circular economy that results in a more sustainable future.
- Cost savings
Investing in green steel within a warehousing infrastructure can offer long-term financial benefits, like lower energy costs and potential government incentives for using sustainable materials. Green steel is often more durable and resilient, leading to longer-lasting structures. This reduces the need for frequent repairs or replacements, which in turn minimizes the environmental impact over the building’s life cycle. In addition, as the construction industry moves toward greater sustainability, using green steel can position companies as leaders in innovation, making them more resilient to future changes in industry standards and market demands.
- Compliance
As regulations and industry standards increasingly focus on sustainability, using green steel is helping companies comply with environmental laws and certifications, potentially avoiding penalties and enhancing their market position. The companies that adopt green steel demonstrate a commitment to environmental responsibility and sustainability, which can appeal to eco-conscious customers, investors, and stakeholders.
By adopting green steel, warehouses and distributors can align with global sustainability goals, reduce operational costs, and future-proof their infrastructures. As the industry moves toward greater sustainability, embracing green steel can position companies at the forefront of innovation, driving positive change and contributing to a more sustainable future.