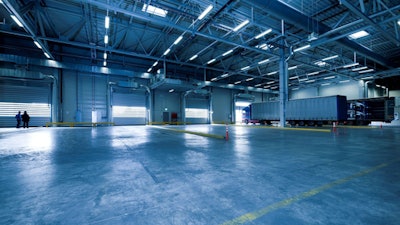
Food distribution logistics in the United States have been challenging for many years, with inefficiencies in the system often leading to pain points for both food distributors and consumers. Big data is available to lend a helping hand, from warehouse scanning to virtual inventories. And with advances in technology, data can now be used to improve operations and make the system more efficient.
How is structured cabling used in food distribution?
One area that has seen significant improvement in recent years is the use of structured cabling systems. These form the backbone of any food distribution center and allow different types of equipment to be connected, including everything from conveyor belts to scanners and sensors.
Structured cabling improves the flow of information between different parts of the distribution center. This is important because it helps identify bottlenecks and other potential areas of improvement. Additionally, structured cabling systems can also help to improve safety in the workplace. By better understanding how the distribution center is being used, hazards can be identified and quickly addressed.
Finally, structured cabling systems also help improve the distribution center's overall productivity. With a more efficient system, food can be distributed more quickly and effectively. Why is this important? Ultimately it leads to lower costs for both the distributor and the consumer.
How is data used in food distribution?
With structured cabling in place, data is an integral part of supply chain management in food distribution. It's used to track the movement of food products throughout the supply chain, from farm to table, including warehouse and logistics tracking in between. This tracking can help identify inefficiency and waste areas, which can then be addressed by management. Additionally, data helps to monitor the quality of food products, meaning that only the highest quality products are being distributed.
Here are some of the top ways that data is collected and analyzed:
- Warehouse data - the location of inventory, order picking accuracy, and more.
- Transportation data - shipping routes, delivery times, etc.
- Consumer data - purchasing habits, preferences, etc.
- Volume data - the amount of food being distributed and any trends that may be occurring.
- Financial data - the cost of food and the price of transportation.
- Demand data - the demand for specific products and any shifts that may be occurring.
- Qualitative data - the quality of food, as well as customer satisfaction data.
- Production data - information on farms, processing plants, and more.
All this data is critical in understanding the food distribution process and how to improve it. But it's also essential to understand the relationship between different data sets, with each type of data having a knock-on or domino effect on other data sets.
For example, consumer data can be used to understand what types of food are in demand. This information enables companies to adjust production schedules accordingly. Additionally, financial data helps understand the cost of food and transportation, which subsequently optimizes routes and schedules. Ultimately, all of this data comes together in perfect harmony to create a more efficient food distribution system.
What technology challenges does the industry face?
Let's take a deeper dive into two of the specific challenges involved in food distribution logistics.
Technology investment. Although there are more than 16,500 companies operating in the food distribution industry, the Top 8 companies make up 41% of the market. So, one of the top challenges for smaller distributors is adequate investment in technology that allows them to compete with the bigger players.
Some of these tech giants can use its technology and data to undercut the prices of other distributors. Additionally, they have the financial resources to invest in even more innovative technologies to solidify its position in the industry.
So, how can smaller distributors compete? One way is to focus on niche markets. By catering to a specific type of customer or market, smaller distributors can provide a higher level of service. Additionally, they can also focus on developing long-term relationships with their customers. However, as the price of technology decreases, big data solutions are closer in reach than previously.
Warehouse floor technology. Internet of Things (IoT) technology is being used more and more in warehouses to automate tasks and improve operations. But it can be difficult to integrate into existing infrastructure, which is where an investment in optimized structured cabling becomes a necessity. Although there’s an associated upfront cost, this is also a way to future-proof the distribution network.
Additionally, there can be a lack of standardization among different types of warehouse floor technology. This makes it difficult for companies to compare different technologies and choose the best one for their needs.
How does RFID solve these food distribution pain points?
So, what can companies do to address these challenges? One option is to invest in RFID. Radio frequency identification (RFID) identifies and tracks objects. RFID tags are usually attached to products and contain information that can be read by RFID scanners. Supply chain managers use this to track the product throughout the supply chain, from farm to table.
There are many benefits of using RFID technology in food distribution. GTINs, for example, can be used to automatically identify products. This data then allows companies to keep track of the product throughout the entire supply chain and ensure that it is delivered to the correct destination.
RFID tags are also critical when tracking the temperature of food products. This is important for perishable goods, as it can help to ensure that they are stored and transported at the correct temperature. This information helps to improve the overall quality of the food and prevent unnecessary food waste.
But RFID isn't a new technology. In fact, it's been used in supply chains for more than a decade with fantastic results. For those looking to start using RFID and big data in supply chain and food distribution management, ensure you have the structured cabling infrastructure in place to support the technology. This is a decision that could pay off in the long term, as companies willing to invest in innovation are bound to outlive any fluctuations in the market.