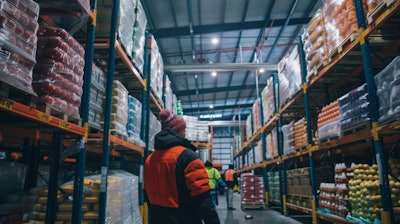
Over the past decade, the United States’ temperature-controlled logistics industry has made impressive advances in the sustainability of cold store buildings and operations.
More than 200 temperature-controlled warehouses are now participating in GCCA’s Energy Excellence Recognition Program (EERP), which helps businesses measure and improve cold store energy efficiency using qualitative and quantitative assessment tools.
Opportunities to improve warehouse sustainability are unique to each facility, as are the challenges. The most suitable approaches to sustainability for a 30-year-old small port-based facility will likely be very different to the right approach for the design and construction of a new 200,000-square-foot automated cold store. However, there are a number of overall trends currently at the forefront of the industry’s action to advance cold store sustainability.
Fundamental to a thorough and considered approach to improving sustainability in temperature-controlled facilities is the effective collection and analysis of site-specific data. Sustainability audits that provide a holistic understanding of a warehouse’s sustainability performance are increasingly being supported by detailed assessments of, for example, cold store building envelope insulation and sealing performance, real-time tracking of refrigeration system performance, and sub-metered monitoring for energy usage data specific to different sections of equipment and facilities. The data acquired through assessments such as these can reveal where energy is being wasted, where sustainability improvements could be made and where equipment requires maintenance before energy efficiency suffers.
This industry trend for sustainability data is being supported by increasingly comprehensive, accurate and affordable cold store monitoring and tracking technologies, and by sophisticated software facilitating the analysis of the data and recommendations for action. It is a trend that is being reflected throughout the food logistics supply chain, where real-time temperature tracking is increasingly used to support both food safety and efficient use of energy.
There are also a number of trends related to the investments businesses are making to improve the operational energy efficiency of their cold stores. In the early phases of sustainability action, sites have been putting a clear and logical prioritization on the “quick wins” that can deliver a significant energy efficiency improvement through comparatively straightforward and cost-effective actions. Switching to LED lighting, repairing door seals and minimizing unnecessary opening times, addressing air leaks, and regular maintenance on refrigeration systems can all deliver significant sustainability improvements alongside energy cost savings. Many cold stores that have already implemented these approaches are now moving next onto actions that can bring substantial sustainability rewards but typically require greater capital investment, such as building envelope refurbishment or replacing ageing refrigeration systems with new, far more energy efficient models.
A fast-developing sustainability trend for cold stores is the opportunity for on-site renewable energy generation. Roof-top solar has become considerably more attractive over the past few years due to the confluence of rising energy costs, solar technology becoming increasingly mature and effective, and the costs of equipment lowering. Many cold chain sites are very well-suited to renewable energy generation and as innovations continue in on-site energy storage and the application of AI-driven renewable energy generation systems, there is great potential for many more cold stores to access very significant sustainability and cost benefits.
Another growing industry trend in the United States for advancing the sustainability of temperature-controlled warehouses is a focus on improving use of space. This includes making better use of the full height of buildings, introducing new pallet systems, and automated systems. Maximizing use of space in this way enables the same energy requirement for a greater number of pallets, thus reducing energy per pallet and improving sustainability of operation.
None of these sustainability approaches are possible without the right skills, knowledge and focus from the team working throughout the cold store and from the business’ support teams. This is why many cold chain operators have introduced regular sustainability training, are employing sustainability managers, and are working to embed sustainability throughout organizational culture.
Alongside Corporate Social Responsibility and the opportunity for cost savings, improving cold store sustainability is also driven by the requirement to comply with increasingly stringent regulations.
Some important new requirements are due in the coming 12 months for temperature-controlled warehouses. However, changes in government strategy under the second Trump administration may lead to some amendments to these requirements, in line with a paring back of the overall regulatory framework: one of the President’s first Executive Actions of his second term was to freeze all regulatory activity to enable a regulatory review. Action to reduce the regulatory burden on businesses is also anticipated within the remit of the new Department of Government Efficiency.
Also expect a change of government direction on climate change and energy issues, as set out in the Day 1 Executive Orders withdrawing the United States from the Paris Climate Agreement, the UN framework on climate, and the declaration of a national energy emergency.
One requirement currently imminent relates to the transition from Hydrofluorocarbons (HFCs) to lower-GWP (Global Warming Potential) substitutes in refrigeration, under the American Innovation and Manufacturing (AIM) Act. The Act’s “Technology Transitions” rule sets a compliance date for cold storage warehouses of Jan. 1, 2026 regarding the GWP limits for HFC refrigerants used in new systems put into place after this date. At time of this writing, it is uncertain whether the second Trump Administration will continue with this timeframe or whether it may take steps to slow or roll back AIM Act implementation. At this stage it is sensible for cold storage operators to continue to prepare for compliance according to the existing implementation timelines.
GCCA is calling for a change to current implementation plans on another incoming new requirement for the cold chain. The Food Traceability 204 rule under the Food Safety Modernization Act (FSMA) requires traceability recordkeeping beyond those in existing regulations, with a current compliance deadline of January 2026. GCCA has raised concerns that current requirements will be unnecessarily burdensome and that the industry needs additional time to implement compliance measures. GCCA is urging the FDA to engage with the industry on pilot programs that will support the rule’s objectives, including a reduction in food waste throughout the supply chain, but without creating additional unnecessary burden; to further develop compliance guidance materials for industry; and to postpone the compliance date.
The latest Risk Management Program (RMP) Rule “Safer Communities by Chemical Accident Prevention,” in effect since May 2024 (but with the compliance date for most provisions not until 2027), may also be subject to change as it is possible that President Trump may reverse some RMP changes in a similar approach to his first term.
Cold storage facilities can consider new opportunities following a recent policy change on the location of Import Houses (I-Houses), storage warehouses permitted to serve as holding areas for goods called for import inspection. The Food Safety Inspection Service (FSIS) announced in December 2024 the removal of an arbitrary restriction on the permitted locations of I-Houses, following a successful joint petition by GCCA and the Meat Import Council of America (MICA). This change will help reduce food logistics transportation times and distances, delivering an important sustainability benefit for the food supply chain.