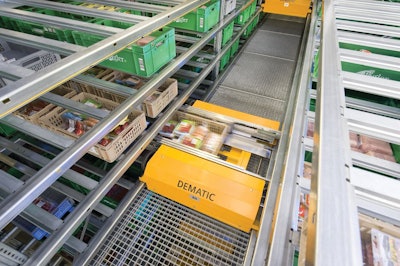
Almost everyone in the food and beverage industry has their dinosaur--the old warehouse or distribution center that’s been around since the beginning, the one that started it all and the one that holds endless memories of the good times.
Some may still be storing product. Some of them were the ‘crown jewels’ of their time, but have lost their luster as the speed and scope of business changed rapidly over the years. And, that pace hasn’t let up. The reality is that if you’re not constantly looking at new innovations and ways to improve your warehouse facility and operations, you’re getting left behind.
Technology advancements combined with the latest demands in the food and beverage supply chain are in perpetual non-stop motion. With consumer demand pushing retailers and suppliers into an “omni-channel” model of business in the future, warehouses will need to be more versatile and more sophisticated than ever before in order to stay at the forefront of their industry.
While the ways to renovate and innovate are many, today’s industry trends show a clear preference in three key areas: energy efficient lighting, labor efficient automation, and the newest improvements in facility design that provide fast and efficient packaging, storage and distribution of goods in the warehouse.
Let LED light the way
The advances in lighting technology have come at a light speed pace in recent years, with LED lighting dominating the category in most warehouse and cold storage facility renovations. From LED High Bay fixtures that come with 10-year warranties, to elaborate integrated control systems that control every space inside the facility, the innovation in the LED category itself continues to make so much progress that it’s hard for facility managers to stay up to date with the changing technology.
Upgrading or retrofitting lighting systems to LED continues to be a hot trend in the warehouse industry because more often than not, the lights are on 24/7 and can typically account for a large portion of the overall electricity consumption. With utility companies continuing to raise rates at sometimes double-digit levels in some areas, upgrading the lighting in the facility is a relatively simple fix that can save thousands of dollars in energy costs in the short term as well as “future proof” your facilities.
The energy savings alone that an LED system can bring compared to an older lighting system is often substantial and enough reason for companies to look into upgrading their lighting, but it’s not the only reason fueling the trend to switch. LED lights offer better light quality and often solve equipment safety and employee efficiency issues by eliminating dark areas in the warehouse. LEDs also offer a longer lifespan, which means lower maintenance costs and quicker return on investment despite the initial higher upfront costs.
The movement to warehouse-wide LED systems is also being fueled by new features and advancements in LED lighting and software systems. Not only do these new systems give users the ability to turn the lights on and off, but dim them, as well as turn them on and off depending upon the traffic and activity in any given space, all of which are huge energy saving measures in big facilities.
These new fixtures and systems are also hugely popular in cold storage warehouse renovations because unlike traditional lighting in these settings, LED fixtures radiate less heat and will not degrade or lose lifespan and longevity due to repeatedly cycling the lights on and off or dimming them when a space is unoccupied for a set amount of time. Even in temperatures of -40 Fahrenheit, LED fixtures can be turned off and on without losing bulb life or quality, an innovation that runs contrary to every other lighting option in cold storage environments.
Automation can ease your labor pain
Automating the repetitive labor processes in the warehouse can relieve bottlenecks that occur when those areas fail to keep up with the efficiency gains at other parts of the line. It also lowers labor costs, offering substantial long term savings that many companies need to stay competitive in today’s market.
With the costs for robotics, automated guided vehicles (AGV’s) and other high tech advances that can fully automate a warehouse still large enough of an expense that it limits access for some buyers, food and beverage companies can nonetheless realize improved efficiencies by utilizing other automation tools, including automated sorters, conveyors, palletizers and automated storage and retrieval racking systems (AS/RS).
In particular, today’s “omni-channel” trend in product fulfillment is generating interest and growth in AS/RS, since food and beverage companies are going from full pallet picking of large orders to small, frequent daily orders in many cases, and an automated system complete with warehouse control software offers them the ability to meet these changing requirements.
“Gone are the days of one SKU and one pallet deliveries to a retail store or even a distribution center,” said Sean O’ Farrell, Market Development Director at Dematic Corp. “Automated storage and retrieval systems can be used as a buffer to consolidate cases, totes, or orders before releasing it to a manual or automated palletizing system, and they can also allow you to better utilize your transportation because you shorten the length of time needed to load and unload trailers at the docks.”
For some companies, an upgrade to a flow storage system and pallet racking is the proper fit for their high volume, space efficient needs. These systems minimize overhandling and product damage, eliminate labor and fork truck operation and emissions, and can also help to reduce aisle space and allow more product to be stored than traditional selective pallet racking. Instead of floor stacking two to three pallets high, automated systems allow companies to optimize inventory management and securely store product higher and deeper to maximize the storage density of the warehouse.
Since the majority of frozen food and cold storage operations conduct warehousing activities in sub-zero temperatures, they often fall victim to high personnel turnover due to the chilly temperatures. Performing these manual operations also can pose operational and logistical challenges like increased product, facility and equipment damage and errors in order fulfillment, all of which are easily eliminated with an automated storage and retrieval system (AS/RS).
Nowadays, high-density AS/RS systems allow cooler and freezer facilities to store unit loads two to 18 pallets deep, while reducing the 12-foot-wide aisles of a typical cold storage facility. AS/RS’s can quickly decrease the operational and logistical challenges many face in these cold storage warehouse environments, because a well-designed system integrates the reserve storage and re-supply of product to some type of order selection process, whether automated, semi-automated, or manual.
But efficiencies through innovations can also come from the latest in energy efficient dock shelters, high speed doors and high volume, low speed (HVLS) fans.
Since the primary challenge for dry, refrigerated and frozen food distributors is controlling the environment and traffic, the fast opening and closing speeds of today’s high speed dock doors minimize the air exchange between areas. Less air infiltration leads to lower heating and cooling costs and less product loss, which directly impacts the bottom line. Most high speed doors also offer low profiles to save valuable freezer or cooler space, and are built to be self-repairing and engineered to withstand the impact of a forklift for increased safety.
Design it and business will come
When it comes to trends and innovations in facility design, it’s almost always based on the goal of making the warehouse more modern, more high tech with plenty of safety, security and “green” features, as well as pressure and temperature control upgrades. Meanwhile, if equipment upgrades and facility upgrades come due at the same time and future growth is on the horizon, many companies are choosing to make the large investment and redesign or rebuild to get their combination of cold storage or warehousing on the cutting edge.
Most often when facility design gets involved it’s starting from the ground up, but with vacant facilities all over the landscape at cheap prices some companies in the food chain are using customized facility designs to retrofit and repurpose buildings that are already standing.
That was the case for Hudsonville Creamery & Ice Cream Company in Michigan, when they took an abandoned former auto manufacturing facility and designed it to fit their growing ice cream business.
One of the design features implemented by Hudsonville was to move all of their bulk raw material silos inside the facility, which allows them to control the ambient temperature, environment and security of their ingredients. With two large truck bays positioned right by the storage silos, raw milk, cream and liquid sugar are delivered right inside giving them the safe and secure work flow through the facility.
“We were really ahead of our time because we designed the new facility to do it right, which meant bringing most things inside instead of out behind the plant like at most food manufacturing facilities,” said Cary Grover of Hudsonville. “Now we can control everything, temperature, pressure and the security around the different raw materials we use.”
Some other trends companies are taking advantage of in design are using better and modern materials to create more efficient and safer waste-piping systems. New designs often use more efficient routing throughout the facility to minimize the number of code-required vents and in turn lower the labor, material and overall installation costs of new systems.
At the same time, other companies are looking to improve their sustainability efforts in regards to warehouses by designing (or redesigning) the facility for on-site wastewater or byproduct recycling. Where flexibility and adaptability are available, companies are choosing to reuse and recycle everything they can before it’s disposed of entirely.
Wastewater designs allow for treated water to be used in irrigation, condensers, refrigeration systems and other non-potable uses.
Beverage, dairy production and also meat packing plants are taking advantage of their manufacturing and processing operations to turn wastewater and other byproducts, such as methane gas, into energy that can be reused in their facilities to help trim energy costs and reduce their carbon footprint. ?