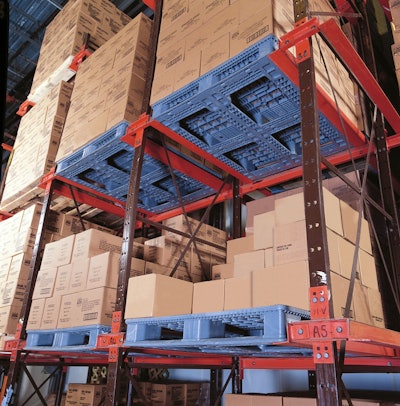
Recyclable, renewable, repairable and durable. Wooden pallets have long been considered the most cost-effective option. However, a recent study by the Virginia Tech Center for Packaging and Unit Load Design makes a strong case for the plastic pallet’s long shelf life.
Using the center’s FasTrack life-cycle analysis to compare relative durability, researchers found ORBIS Coproration’s 40x48-inch RackoCell plastic pallet has approximately 18 times the life span of a 40x48-inch whitewood stringer pallet.
The FasTrack life-cycle analysis included a 10-step handling sequence, which involved routine pallet handling activities, followed by inspections of the plastic and whitewood pallets. In testing, the RackoCell plastic pallet completed the sequence up to 200 times without failure, while the wood pallet’s average failure was after 11 cycles.
“We wanted to quantify the life and durability of plastic pallets to help companies understand the long-term cost savings associated with reusable plastic pallets,” explains Ryan Roessler, product manager at ORBIS Corporation, a pallet manufacturer that specializes in reusable, returnable packaging, primarily with bulk containers, pallets and handheld containers.
While 90 percent of the market is still using wood pallets, Roessler says the FasTrack life-cycle analysis confirms an advantage plastic pallets may have over wood—reusability.
“Wood pallets are used because they're cheaper and they're always going to be cheaper, but companies are turning to plastic pallets for a few reasons,” he adds.
The long-term cost benefit of a reusable pallet is a big one, in addition to their dimensionally consistent design, cleanability and environmentally-friendly characteristics. These factors become increasingly important in the food and beverage space, where issues beyond durability come into play.
An Engineered Solution
As automation, especially for food and beverage manufacturers, continues to expand throughout the supply chain, so does the use of plastic pallets. While premium wood pallets have also made advancements in this area, the dimensionally consistent design of a plastic pallet allows for a smoother movement of product through the supply chain and can be easier to build automation around.
“Reusable plastic pallets provide value in that they're an engineered solution, so they're made specifically for all types of material handling equipment; they're designed in a way that just allows the product to be moved easier,” explains Roessler.
In contrast, Roessler says some wooden pallets can be inconsistent in how they're built and can hinder the entire automation process.
“The top deck boards can be odd sized, the stringers in the bottom are not always the same in style and then those pallet boards can break easy too,” he says, adding, “With automation there are a lot of lasers and stuff around the plant that tell the machinery where to go, when to stop, etc. When those lasers are focused on something that's on a pallet that's not a consistent size or shape, it can stop the whole supply chain, bringing about a lot of inefficiencies that cost plants and companies money.”
Jeff Liebesman, CEO of iGPS Logistics, a logistics solutions provider that offers the only plastic pooling rental program in the United States, agrees, noting this is especially important in the grocery industry where margins are tight.
“Since the grocery supply chain is margin compressed, implementing automation systems in food and beverage industries is accelerating to advance cost efficiencies. Our (plastic) pallets’ consistency in size, weight and shape maximizes efficiencies and returns on the large investment in these automated systems. A wood pallet by comparison varies often and significantly in size, shape and weight, causing shutdowns and additional maintenance and compromising the efficiencies of the automated systems,” Liebesman adds.
Roessler encourages companies who are investing in automation to bring in their pallet supplier or packaging experts and really build their automation around their pallet. “That can save you a lot of problems in the future,” he adds.
Safety First
Due to government mandated legislation and consumer outcry, food safety is also top of mind for food and beverage companies. Because wooden pallets often are unable to comply with these industry requirements, the demand for plastic pallets continues to grow. Plastic pallets are also easy to clean and dry, as they have a smooth and closed surface that eliminates cavities and doesn't allow dirt from accumulating.
As for ORBIS, Roessler says they are just starting to see the effects of sweeping regulations such as the FDA’s Food Safety Modernization Act (FSMA).
“We're kind of at the point where customers are taking a more serious stance,” Roessler says. “Plastic pallets weren’t the first thing customers thought of when it came to FSMA; it's been more about their equipment, more about the actual processing of their product, but now it's trickling downward more and more.
“Plastic pallets, just in general, give customers peace of mind; it's one less thing that's going to cause a potential recall,” he adds.
And ultimately, the whole goal of better food safety practices is to prevent recalls from happening. The fallback of that for ORBIS, Roessler says, has been the emergence of a customer demand to convert their entire supply chain to something that's reusable.
“So for example, if I'm a soup manufacturer, I want my product coming in on a plastic pallet. For my suppliers that are supplying the celery and carrots or other ingredients, I'm encouraging them upstream in the supply chain to bring the product on plastic pallets.This helps to mainstream the whole process. And then they have a better peace of mind that the proper food safety measures are in place throughout, from start to finish in the supply chain,” Roessler explains.
Liebesman adds that the same security is not offered with wooden pallets.
“Wooden pallets carry a significantly higher risk of product loss and contamination, which food and beverages are more vulnerable to, and very importantly rejection by the retailer, which is costly to the manufacturer,” he notes. “It is a difficult task to remain competitive in a comparatively high-risk industry like food and beverage production, so customers are seizing on any and all cost-saving measures and employing them wherever they can.”
Long-term Cost Benefits
Cost is an obvious impediment for plastic pallets, as the price of wooden pallets is relatively low in comparison. While Liebesman acknowledges that the upfront cost of plastic pallets is higher than wood, he says the correct way to evaluate costs is over the life of the asset including repair and replacement.
The main point of attraction for many companies that purchase plastic pallets is the reduction in the costs associated with the repair, maintenance and storage of pallets. Rental companies like iGPS further eliminate these costs by providing regular quality checks to avoid any damage to pallets. Rental programs also give companies the flexibility to rent the exact number of pallets they need, rather than having to stock for peak seasons and keep idle pallets in storage.
According to iGPS Logistics’ Liebesman, the company’s plastic pallets have made more than 100 million trips throughout the grocery supply chain, allowing iGPS to uniquely develop a platform that can withstand the robust and rigorous use as a pooled rental pallet.
“While other plastic pallet options are available, none have the durability or design to withstand the rigors of a pooling service, and generally have a shorter life,” says Liebesman. “We understand clearly the greatest benefits of plastic pallets and know how to maximize them for customers.”
Follow Amy Wunderlin on Twitter.