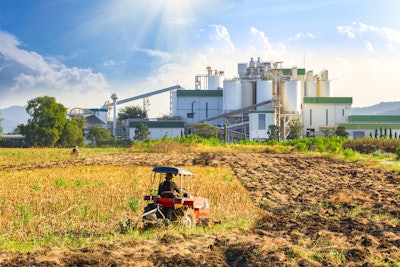
Today’s consumers are increasingly favoring products with carbon-free labeling, and manufacturers are paying attention. A 2022 Consumer Brands Association analysis found that among the Top 50 consumer packaged goods (CPG) companies, all of them had clear commitments to address climate change, improve packaging sustainability and reduce water usage. The Food & Drink Federation (FDF) announced its ambition to reach net-zero emissions by 2040, a decade ahead of the Paris Climate Agreement.
And, to date, more than 300 of the world’s largest companies have also vowed to achieve net-zero emissions by 2040. With such bold commitments, some are asking, “now what?”
Many of these organizations are going all-in on renewables, hoping significant advancements in the coming years will be enough to turn back the climate clock when the right technology arrives. But even if a major switch to renewables was possible today, it would only push costs higher, overburden the current grid infrastructure and force companies to reduce production, which is an impossible option when manufacturers already have difficulty keeping up with rising demand.
There’s a better solution – one that could help manufacturers cut up to 80% of their carbon emissions now by optimizing the thermal processes within their factories. In short, it’s all about capturing waste heat and using it as energy. Manufacturers across the entire spectrum of light industry have the capability to act now, but may not realize they can.
To illustrate, most of today’s manufacturing plants were built 50 years ago or more and therefore have a unique opportunity to upgrade their facilities to minimize waste heat and optimize efficiencies. Take food processing, for example. Many food products today require a significant amount of energy for cold storage and sterilization. This leads to a lot of waste heat during the cooling process, while the factory concurrently needs heat at relatively low temperatures (-250°F) to operate successfully.
Using artificial intelligence (AI)- and Internet of Things (IoT)-powered tools, a thermal utility expert can map these thermal processes, find where the heat is going, monitor performance and flag failures – all in real time – giving site managers the ability to make better, more informed decisions.
Many of today’s manufacturers can knock off 80% of their emissions with this strategy. By implementing an internal process heat exchanger network coupled with industrial high-temperature heat pumps, companies can minimize a plant’s energy waste, optimize its thermal energy efficiency and build a strategy for complete decarbonization. This process is called Circular Thermal, which takes the stream of waste heat and channels it back to the process where the energy is needed in a three-step process that includes de-steaming (conversion to pressurized hot water) all applications below 250°F, recovering direct heat when a positive differential temperature is available and using industrial heat pumps for raising the temperature of low-grade heat to the temperature that is useful for the process.
Once factories have achieved complete optimization, the final 20% of greenhouse gas (GHG) emissions can be removed with renewable sources at a much lower cost, increasing the company’s profit margins and making it more competitive in the long run. And, more importantly, saving the planet from unnecessary pollutants.
Don’t wait for a renewable silver bullet solution to act. Take advantage of the tools available today to make a difference now.