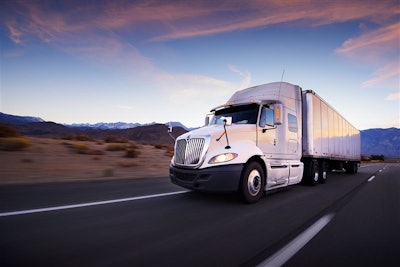
When 2021 hit, the world was ready for the New Year. Even if it brought with it a New Normal -- new way of doing business, a new way to shop for groceries and more -- the turning of the calendar meant putting a year of supply chain disruptions, restaurant closures and constant pivoting behind us.
But, then, on March 23, a stranded Evergreen container ship blocked navigation in Egypt’s Suez Canal, setting the stage for what would be a slew of supply chain disruptions after supply chain disruptions.
Suddenly, 2021 was quickly becoming a mirrored reflection of the year prior.
Then came the ransomware attacks, internet outages, container ships stuck at bay, bridge closures, driver shortages, ingredient shortages, natural disasters and more.
The hits just kept on hitting.
And, industry experts are already showing signs of struggle for 2022 into 2023, as routes to import/export remain clogged, ports continue to be backed up, cost of doing business increases and the labor shortage exists.
That’s because supply chains are messy. And, they’re only going to get worse before they get better.
In Food Logistics’ Nov/Dec 2021 issue, editor-in-chief Marina Mayer talks with several industry experts about the state of the supply chain and what’s in store for 2022.
Here’s an interview with Alex Wakefield, CEO, Longbow Advantage, who explains why now is the time to build flexibility into processes, with excerpts publishing in Food Logistics’ Nov/Dec 2021 issue. [CLICK HERE to read the article in full].
Food Logistics: 2021 started off with supply chain disruption after supply chain disruption. From the Suez Canal blockage and natural disasters to ransomware attacks and an industry-wide labor shortage, the supply chain industry is having to prove its resiliency over and over again. Looking into 2022, what does the state of the supply chain look like?
Alex Wakefield: Supply chains will continue to be a cornerstone of the global economic conversation. As ports get more and more jammed and supply and demand ebbs and flows in seemingly unpredictable ways while we all struggle with optimizing labor and maximizing throughput, companies will be analyzing their traditional planning models to incorporate more in-the-moment analysis and real-time improvements as opposed to reacting once disruption has occurred.
Food Logistics: The cold food chain continues to face a host of risk/security challenges. What can companies be doing now to adapt for the future?
Wakefield: Cold food and other perishable goods don’t have the luxury of sitting in port or at a dock for an extended period of time. Building flexibility in processes based on real-time visibility into a resilient supply chain to allow distribution centers to monitor and maintain statuses and locations of their products real-time will enable them to shift to scale up or down production as appropriate.
Food Logistics: Let’s talk supply chain visibility. What is your company – or what should companies – be doing to improve their own supply chain visibility?
Wakefield: Supply chain visibility is a phrase that means a lot of different things. The area of supply chain where real-time visibility actually can help companies maximize throughput the most is in the warehouse. Being able to make point-in-time changes that have tangible impacts on the shift or the day’s goals allows distribution teams to massively impact profitability. Having a maniacal focus on incremental changes driven by real-time data insights is the biggest opportunity logistics operations have in front of them today.
Food Logistics: The labor shortage is a real thing, and it’s impacting several facets of the supply chain. What is your company – or what should companies – be doing to hire, onboard and retain good quality supply chain workers?
Wakefield: The best thing companies can do to manage the labor shortage is retain the employees they currently have. One of the ways we’re seeing companies do that is by implementing pay-for-performance programs in the warehouse. In distribution centers where we’ve seen them implemented, employees are often seeking out management to better understand their performance and learn how that can maximize their impact, creating a feedback loop that can be used to increase performance, engagement and satisfaction.
[CLICK HERE to read the article in full].