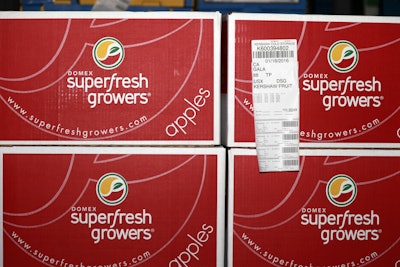
Supply chain traceability has taken center stage in the food and beverage (f&b) industry like never before. The near finalization of the Food Safety Modernization Act (FSMA) has forced the industry to scrutinize its food safety practices. And as supply chain companies comply with the new law, an emphasis on improving traceability throughout the supply chain has been ongoing for some time.
A globalized market, advances in production capabilities, enhanced disease detection systems, SKU proliferation, Internet-enabled reporting and the omnichannel have all shaken what was once a fairly simple f&b supply chain. These forces have expanded the supply chain and created new challenges to supply chain visibility. Growers, processors, packers, distributors, retailers and transporters are all in need of better traceability tools.
Advances in processing, packaging and temperature control have extended the shelf life of many products, creating opportunities to send products across greater distances. At the same time, changing lifestyle trends and advances in global communications have created a demand for more food attributes such as non-GMO, gluten-free, fresh, local, cage-free, etc.
Improving supply chain traceability usually requires integrating inventory accountability with case, package and/or pallet labeling. To track the movement of inventory, a company needs to have the hardware that enables asset identification (i.e., label printers and scanners) and the software that monitors its movement through the supply chain.
What is traceability?
Traceability refers to collecting information about a product and ensuring the data’s visibility to other points in the supply chain. Technology has created a vast array of tools that enable this capability, such as sensors, barcodes, RFID tags, label printers, GPS transmitters, radio frequency scanners, temperature and humidity loggers, and supply chain software.
A specific application will vary based on the particular supply chain function. The need to track an individual unit versus a batch or a lot will depend on the product. Similarly, the type of information tracked depends on the product’s attributes and uses.
As this story will explain, available tools include an expanding array of hardware and software solutions.
A major tool that has emerged to support traceability in the supply chain is data standardization. Different data schemes exist, the most established being GS1 US, a global organization that develops and maintains supply chain standards.
As data standardization expands among supply chain players, users will find they can provide partners more accurate information faster.
A company that can reliably trace a specific product in its supply chain can pull the product without having to remove more products than necessary. Because the standard provides identification for each individual case and/or pallet, it is not necessary to remove cases of product unaffected in the event of a recall.
Uniform data standards emerge
Traceability hardware and software providers were nearly unanimous in pointing to GS1 US as the key to improving supply chain visibility.
Meat, poultry and produce were the first food segments to adopt GS1 standards, says Angela Fernandez, GS1 US vice president of retail grocery and foodservice. Dairy, deli and bakery are catching up, she says, and seafood – most of which gets imported in the U.S. – is also getting on board. In all product segments, the larger growers, processors and distributors are leading their smaller competitors.
Particularly in the produce industry, traceability has been driven forward by companies that implement standards according to the Produce Traceability Initiative (PTI), which is designed to help the industry maximize the effectiveness of current trace-back procedures, while developing a standardized industry approach to enhance the speed and efficiency of traceability systems for the future.
The retail food segment invested in data standardization faster than foodservice, Fernandez says, but this is changing. “They (foodservice companies) are quickly coming up to speed and in some cases surpass where the retail industry is,” she says. Traceability has been a major driver of interest in data standardization.
More than 15,000 companies sign up to use the GS1 Standards every year, Fernandez says.
Data standards require planning
While the growth of data standardization is a positive development, the task of adopting the standards requires planning and commitment. Companies must make a multi-year investment to implement GS1 Standards across the entire supply chain for a comprehensive traceability program, Fernandez says.
A retailer seeking end-to-end supply chain visibility will need to get all its suppliers to use the GS1-128 bar code at the case level, which has the capability to capture more traceability data such as batch/lot number, and sell by/use by/pack/ dates. They will also have to make sure that all DCs in their supply chain are capturing and storing all the dynamic information carried in the bar code. All stores in the chain will have to use bar code scanners at their back door to read the GS1-128 bar code.
Periodic software updates and scanner updates will also be necessary. “There are many benefits to being able to capture and share more product information,” Fernandez says. In addition to improving food safety through supply chain visibility, companies can reduce costs, enhance operational efficiencies and strengthen their trading partner relationships overall.
Why implementation lags
A few major U.S. retailers took a leadership role a few years ago in embracing the PTI, the industry traceability initiative that leverages GS1 standards. Implementation, however, has not been as easy as some envisioned. The retailers’ distribution and store systems were not ready to track the suppliers’ traceability information through the DC to the store or suppliers’ direct-store-deliveries (DSDs), says Todd Baggett, president and CEO of Redline Solutions, the Santa Clara, Calif.-based provider of inventory and traceability software.
“It’s not a simple problem,” Baggett says. “Traceability requires transparency of grower item and lot information down to the store level. This is much deeper that they tracked in the past and requires software systems to be updated.”
While adoption of electronic traceability solutions is growing, there are still a lot challenges with regards to data uniformity and standardization throughout the supply-chain, says Wayne Slater, director of Ontario, Canada-based Carlisle Technology. The collection and transfer of data can vary greatly among supply chain partners. Challenges include learning automated collection process, the nuances between different electronic traceability vendors, and overcoming the legacy best practices (aka: “we always do it this way”).
“It’s no secret, the GS1 traceability standard does a great job at defining the minimum traceability requirements within business processes to achieve full chain traceability, independent of any technology by using other GS1 standards,” Slater says. “While growing in adoption, thanks mainly due to standards imposed by progressive retailers like Walmart and Costco, I am still running into many food companies where traceability principles and GS1 adoption is still in its infancy.”
Slater thinks companies will adopt the GS1 standards as they realize the efficiency and accuracy it offers over manual data entry.
FMSA to drive data adoption
The FSMA’s new record keeping requirements are likely to encourage supply chain players to adopt more uniform data standards. Hence, while the FMSA’s purpose is to improve safe practices, the adoption of uniform data will improve inventory traceability throughout the supply chain.
Some observers believe that in designing the FSMA, the Food and Drug Administration recognized that the different data coding systems within the f&b industry was an obstacle to enforcing food safety. Hence, FDA developed record-keeping requirements that could make both compliance and enforcement easier. While the FSMA does not say what record-keeping systems companies should use, they will find standardized data templates will make compliance easier.
Carl Iversen, vice president of product development at LINKFRESH, the Ventura, Calif.-based ERP provider, says the FSMA is actually mandating traceability of certification and documentation as well as traceability of product. This is borne out by the law’s electronic reporting requirements which are intended to make compliance easier.
Iversen envisions companies setting up websites to which suppliers will submit electronic forms and scanned document uploads. Suppliers will submit digital photos of certificates of things like quality checks, HACCP and GMP compliance. “How is your supplier providing all the things required?” he asks.
Iversen sees the Internet of Things (IoT) becoming a big part of f&b traceability. Software silos are giving way to unstructured data platforms, where things like scanned paper trails, emails and phone logs become part of a transaction record.
In time, people will realize that technology is making their lives easier rather than harder. “Greater integration is actually making business people’s lives easier,” he says.
“While many of these documents still have to be produced physically, the future will see more and more acceptance of ‘digital’ compliance,” he points out.
Under the FMSA’s preventive controls section, some facilities are required to verify that a preventive control is capable of controlling an identified hazard. However, the FSMA does not mandate specific tools for verifying preventive controls.
Documents must be monitored
Under the FMSA’s sanitary transport rule which is scheduled to be finalized at the end of March, some facilities must document monitoring and recording whether a process or action was in compliance. Examples include monitoring temperature during transportation, product temperature prior to loading or pre-cool temperature of a truck.
Jere Van Puffelen, president of Prism Logistics, a Stockton, Sacramento, Livermore, Modesto and Hayward, Calif.-based warehouse logistics provider, has found great benefits in having end-to-end electronic traceability. When drivers electronically sign a bill of lading, the system records the driver’s photo and attaches it to the electronic file. These measures are not required by FSMA, but Van Puffelen wants to stay ahead of where things are going for his customers, who are already dealing with the FSMA requirements when it comes to product traceability.
GS1 bar codes allow Prism Logistics to keep track of packages on mixed pallets holding many different packages. Should there be a recall of a particular SKU, identifying the pallet will be handled by the system recalling the specific pallet data. Van Puffelen also likes the fact that the GS1 bar code allows him to enter a lot of product data quickly. “It’s just moving us down the automated data capture trail,” he says.
Van Puffelen is anxious to see more of his food supplier clients use the GS1 bar codes. As a 3PL warehouse operator, he can capture the data on the inbound and then have visibility of the outbound shipments for those manufacturers using these bar codes should there be a question further along the supply chain.
For those customers not using the GS1 bar codes, the warehouse has to manually enter lot codes into the system. “The less you have to have manual data entry, the less potential there is for error,” he says. “Speed of information is becoming more critical and necessary. These bar codes and EDI help everyone in that process.”
Canada leads in farm-to-fork traceability
VG Meats, a meat producer based in Simcoe, Ontario, Canada, has a unique perspective on the beef supply chain. The family-owned company operates a farm, a packing facility, a butcher shop, a wholesale division and a retail division. Being based in Canada, the company was able to take advantage of that country’s national livestock identification program in developing what can be described as a farm-to-fork traceability system.
VG Meats’ tracking scheme focuses on animal identification, location identification, health information, animal movement and meat quality.
Canadian farmers have been tagging livestock with RFID tags under a mandatory industry/government program. VG Meats built on that system by recording the animal’s medical history, birth measurements, weights, tenderness and yield. The company gathers additional information to calculate genetic evaluations for each animal.
This information is useful in deciding how animals are mated to improve meat quality.
The mandatory ID tag uses radio frequency and simply gives each animal a unique identification. Most farmers use a second tag that they can easily read without a scanner when managing cattle. Using on-farm systems, farmers can collect information on pedigree, breeding, calving, weights, vaccinations, treatments and movements.
Should a worker in the field notice an issue with an animal, they can access the animal’s medical history on their smartphone.
VG Meats uses a system called bio Track to capture on-farm information and another system called bio Links to capture information during harvest of the animals, including carcass data. The company creates QR codes containing useful information for consumers and puts this on each piece of meat for sale in the retail store.
VG Meats works closely with BIO (from Bridging Intelligence), which offers both bio Track and bio Links from its headquarters in Eloro, Ontario.
The information has proven helpful in different aspects of VG Meats operations, notes Cory Van Groningen, a partner at VG Meats. Customers in the company’s butcher shops can find out whether an animal was fed grain or grass. They can also learn the meat’s tenderness rating. The company includes a tenderness score on packages in its wholesale division that serves the retail trade. Customers use tenderness to determine the proper cooking method for a cut of meat.
Grower tracks by case
Kershaw Fruit, based in Yakima, Wash., decided to focus more on pallet tracking when it expanded its warehouse in 2013. The company deployed a WMS from Redline Solutions and equipped its forklift drivers with barcode scanners. The system creates a PTI-compliant label that includes information like the lot, case number, date it gets shipped, and where on the truck it was placed. The scanners make it easy for the company to track the PTI labels on pallets and cases. Tracking by case and is important since pallets can hold product from more than one lot. “From the pallet tag we know the grower and the lot,” says Eric Skiles, Kershaw Fruit’s IT manager.
“We’re taking the complexity away,” says Adrian Down, Redline Solutions’ director of marketing.
For tracking temperature in transit, Kershaw Fruit uses Temp Tales from Beverly, Mass.-based Sensitech. Skiles believes the Temp Tale sensors that track temperature in real-time will meet the FSMA temperature control requirements.
Lot tracking plays a big role in in f&b traceability for many f&b companies.
By tagging batches of fish with bar codes, fish packing houses can locate what lot a batch came from, says Alison Falco, president of Dynamic Systems Inc., a Redmond, Wash.-based traceability solutions provider. “With our system, once a lot is co-mingled, only those cases with that lot will be recalled,” she says. The company’s SIMBA software includes time-stamped productivity reports.
In the case of the seafood industry, companies are interested in traceability for sustainability since they aren’t dealing with stringent regulations that the fresh produce market faces, Falco says. Recent reports of human slavery in the supply chain have created a greater awareness about ethical practices, so the ability to prove the source of the fish becomes important for a seafood company’s brand. “There’s been an emerging emphasis on ethics,” she notes.
The software can create customized labels. “We can store and print on-demand in whatever format they (customers) want,” Falco says. “Eventually, everyone (in the food industry) will have to label for compliance and for traceability.”
In some fish packing facilities, individual fish get tagged as they are weighed.
More regulations ahead
Some fish pack houses have extra incentive to improve their recordkeeping on account of a change in federal oversight scheduled to begin to take effect this month.
“This new (Food Safety and Inspection Service) regulation is challenging catfish producers,” says Tom Huls, vice president of sales for CAT Squared, a Conway, Ark.-based software provider for the food industry. “FSIS is going to require food safety data to be available in a very short time frame, which means that plants doing HACCP checks on paper and manually entering them into spreadsheets aren’t going to be able to meet government requirements.” CAT Squared’s system allows companies to collect HACCP, food safety, quality, downtime, plant monitoring, and facility data.
Data capture solutions emerge
There are a variety of automated data capture solutions for lot tracking. Bar codes are the dominant solution, but RFID, which allows faster tracking, is gaining ground.
Terry Myers, CEO of Infratab, which provides cloud-based RFID solutions, says the decision should be based on what the customer needs. While the type of RFID in the supply chain, often known as RFID UHF or RFID EPC, has certain advantages over barcodes, a customer needs to have an RFID reader to use RFID. RFID readers can be installed in smart phones, but the tag has to be physically tough enough for the smartphone to read it.
RFID offers the advantage of being able to scan multiple packages simultaneously, Myers notes. However, aluminum-insulated packages (sometimes used for temperature control) will block RFID signals.
RFID can also allow real-time monitoring of temperature and freshness, but Myers points out that this only makes sense for customers who need it. “Do you really need to know in real-time?” she asks. Customers warehousing grapes are checking temperatures three or four times a day rather than continuously.
Most customers tracking temperature do so for product quality control, Myers says. In such cases, the customer has to decide how many readers are needed and how often they should be checked. Pack houses need to know temperature histories for produce when it arrives from the grower.
“It requires judgment with what you are trying to achieve,” she says. “What incremental value does all that data give you?”
In Myers’ experience, RFID tagging is used mostly for product quality control rather than for traceability or inventory management.
“It’s always going to be a mixture of different tools,” she says.
Retailers and product suppliers alike are showing more interest in automated and real-time temperature monitoring on account of FSMA, says Amy Childress, vice president of marketing at PakSense, a Boise, Idaho-based manufacturer of cold chain monitoring solutions. The company’s AutoSense reader contains a global SIM card that wirelessly reads PakSense temperature monitoring labels on pallets. The reader automatically transfers the data, including supplier name, commodity and temperature, to the cloud via cellular signal and sends alerts directly to users’ smartphones.
As with other aspects of FSMA, the sanitary transport rule does not dictate what tools a shipper must use to meet the requirement. Tom Robinson, senior vice president for ORBCOMM, the Rochelle Park, N.J.-based provider of M2M and IoT solutions, says pre-cooling prior to loading will be a new procedure for some companies. “As important and pervasive as FSMA is expected to be in the industry, we expect participants in the food supply chain to require investment and process improvements.”
There may be additions to the FSMA requirements after the initial implementation phase, Robinson says. For example, the industry may face questions around the calibration and accuracy of temperature management equipment.
Orbcomm’s reefer management device integrates with Thermo King and Carrier Transicold refrigeration units. This ensures that fleet managers can extract temperature data and alarms from the reefer unit while the vehicle is on the road.
FedEx Custom Critical, a subsidiary of FedEx Corp., uses temperature recorders and tracking systems provided by ORBCOMM. The solution enables FedEx to make the cooling chain transparent to their clients; recording and delivering data and taking responsibility for the maintenance of predefined temperature conditions during transport.
New tracking and tracing technologies continue to emerge.
AFS Technologies’ WMS software solution provides single-scan traceability, providing the ability to scan a GS1 label once to extract multiple data elements such as lot and quantity. This single-scan functionality results in more accurate data and reduces scans by 300 percent, adding value throughout the supply chain.
“It really accelerates that data capture process,” says Joe Bellini, CEO of AFS Technologies, based in Phoenix, Ariz. “The single-scan traceability will be especially helpful for complying with the FSMA’s preventive control rules, Produce Traceability Initiative and in managing recalls”
AT&T has introduced a cargo tracking solution for global wireless communication that provides real-time dashboard monitoring of shipments in any transit venue – ground, sea and air. The cloud-based system, called AT&T Cargo View with Flight Safe, includes sensors that can monitor location, temperature, light, pressure and shock.
Customers already include prepared food processors who want to ensure that package temperature is within a specific range, says Mobeen Khan, associate vice president of industrial IoT for the Dallas-based AT&T division.
While the FSMA has generated more interest in f&b supply chain traceability, companies are recognizing that improved supply chain visibility enables them to meet customer needs faster and easier. Traceability solution providers continue to innovate new and better ways to improve this critical goal.
Enhanced WCS Enables End-To-End Product Tracking
As automation expands in the food supply chain, warehouse managers must ensure the equipment they work with can track inventory through more complex warehouse operations. Automation provides a reliable method to efficiently and accurately track and trace product through the supply chain.
Enhanced warehouse control software enables the fulfillment systems to track products in each step of the process, from receiving and put-away through picking, sortation, onto the truck and in transit. This is important as material handling equipment gains new functionalities, requiring warehouse managers to make sure software systems are capable of tracing inventory from receiving to shipping.
Retrotech Inc. in Rochester, N.Y., provided a WCS software solution to enable a snack customer to meet internal quality standards through improved traceability. The system was used as a buffer for raw materials received and stored in an ASRS, which then fed the production lines to create the snack mix.
The customer was then able to: locate any pallet, lot code or SKU in the system in real time; trace every processing point a pallet of ingredients went through; use part of a pallet’s contents, return the remainder to storage and then use the remainder later with individualized tracking; place quality holds on individual pallets, lots or entire SKUs; apply product holds while pallets were moving, reroute so as not to use during active runs, and even replace with those pallets.
“Data allowed the site to efficiently work through any event that may cause a recall of product,” says John Campany, software engineering manager at Retrotech. “When a recall was warranted, smaller amounts of finished product could be recalled due to the granularity of the data kept for each production run. Data could be kept for up to three years to ensure adequate history was available, and mock recalls could be run to ensure employee readiness.”
Watermark Barcode Offers Easier, Faster Tracking
One of the newer identification technologies to emerge in recent years is digital watermarking.
Digital watermarking technology delivers faster check out, more efficient store operations to retailers, and richer consumer information to brand owners and consumers.
Digimarc, a Beaverton, Ore.-based provider, has introduced the “invisible” bar code in partnership with GS1 US. The “DW Code” can be scanned without someone having to point the scanner at the barcode. The watermark spreads across the entire surface of the package.
Like barcdoes, the watermark has to be scanned in the user’s line of sight. Hence, the watermark will is complementary to RFID tags which have the advantage of not having to be in the user’s line of sight.
“It’s definitely a step forward on the amount of information and the accuracy of the information,” says Mike Wehrs, GS1 US’s senior vice president of data products and services.
One of the benefits of DWCode is that it leverages and extends the existing GS1 Standards, Wehrs says. It does not require additional data carriers to be printed on the package and is a good foundational building block for a robust traceability program.
The watermark has a good future in traceability since the code uses trusted information that comes directly from the brand.
Another advantage is that it is very affordable because it leverages the existing printing process used for barcodes.
One challenge is that some users will need to upgrade their scanning equipment in order to read the watermark code.
For more information:
AFS Technologies, afs.com
AT&T Cargo View, att.com/cargoview
BIO, bridgingintelligence.com
CAT Squared, catsquared.com
Carlisle Technology, carlisletechnology.com
Carrier Transicold, carrier.com
Dynamic Systems Inc., dynamic-systemsinc.com
Food and Drug Administration, fda.gov
GS1, 937-435-387gs1us.org
Infratab, 805-986-8880, infratab.com
LinkFresh, 805-804-5060, linkfresh.com
PakSense, 208-489-9010, paksense.com
Prism Logistics, 925-838-1691, prismlogistics.com
ORBCOMM, orbcomm.com
Redline Solutions, 408-562-1700, redlinesolutions.com
Sensitech, 800-843-8367, sensitech.com