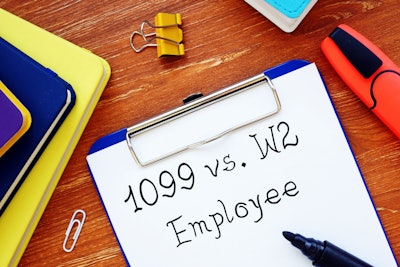
There’s no getting away from the impact of the global tariff war on the food logistics sector, and the ripple effects that have been felt all the way down the supply chain.
Intended as short-term measures to improve trade deals, tariffs are likely to have long-lasting effects that may continue to evolve (as the tariffs themselves continue to evolve), creating an unpredictable environment for businesses.
In fact, April’s Bureau of Labor Statistics Jobs Report shows that warehousing demand and labor needs are already fluctuating, with the addition of 9,800 warehousing jobs alone, on the market.
Given these effects on just one element that makes up the full, end-to-end supply chain, is it indicative of a wider issue, and if so, what’s the solution?
Here are some steps businesses can take to minimize its impact on day-to-day operations.
The tariff effect: Opportunities and challenges
There are, undoubtedly, positive effects to be felt by U.S. food logistics businesses, as a result of increasing global tariffs – not least, the rise in domestic production can shorten supply chains, reducing reliance on overseas shipping and creating more regional logistics activity.
But when companies have traditionally been reliant on smooth flow of goods across borders, the disruption that rising tariffs bring can lead to a rise in operational expenses. And staffing costs form a significant proportion of these expenses, pushing businesses to reassess their workforce needs.
As Noah Yosif, chief economist at the American Staffing Association, explains, extended tariff policies could slow hiring and job growth, and even lead to layoffs. To avoid this scenario, businesses will need to adjust their staffing strategies to deal with increasing costs, and look at a range of different solutions.
Ultimately, uncertainty in the economy, whether tariff-related or otherwise, makes it more difficult for businesses, especially in the food logistics sector, to make long term investments. This is especially true given the recent back-and-forth from the current administration, with many organizations adopting a ‘wait and see’ approach.
But that doesn't mean that businesses have to be in a full holding pattern in the short term. When demand changes on a dime, it’s critical for businesses to be able to adjust accordingly to both hit their demand and maintain their cost structure.
How to meet this ever-changing demand: The right staffing levels
Food logistics leaders can’t simply hire more full-time staff, as these changes in demand are likely temporary and demand planning has become more difficult than ever in this volatile climate.
As a result, many organizations are turning to a more flexible workforce to overcome this volatility and temporary staffing shortages.
This results in heavier reliance on contingent workers, who complement an existing, permanent workforce, or utilizing a more even mix of full-time employees and contingent workers, allowing you to increase productivity levels or scale back quickly, as conditions change.
This flexible approach enables businesses to respond to market fluctuations more quickly and effectively.
3 ways flexible staffing helps your business
Flexible staffing isn’t just a nice option to have when the market chops and changes – it can genuinely help you, by:
1. Matching staffing levels to real-time demand, as inventory levels change: Having a ready-made pool of reliable, skilled contingent staff allows you to bring them in as and when demand spikes, then reduce the need for them when things cool down again.
2. Reducing fixed labor costs while remaining compliant with changing regulations: Turning to contingent workers can bring your overall staffing costs down, without contravening any local or national labor regulations. In fact, by hiring temporary workers, employers can save approximately $9.27 per hour, as they’re not required to provide health insurance, retirement contributions, or paid leave, which are typically reserved for full-time staff.
3. Accelerating hiring and onboarding by using a pool of skilled contingent workers: This allows you to turn to the same workers — who you already know well — time and time again, allowing for greater consistency and productivity, as they don’t have to get up to speed on your systems and processes each time. This approach is particularly useful when it comes to last-minute fulfillment in last-mile delivery and warehouse operative roles.
Looking ahead: Planning when the only certainty is more uncertainty
As global trade policies continue to change, even as this post is being written, businesses within the food logistics supply chain stand to benefit from looking at more agile workforce strategies. And with demand often fluctuating rapidly, there’s certainly a need to develop flexible staffing models that can scale up or down quickly.
Ultimately, in times of volatility, having a variety of staffing options on the table is likely to be one thing that allows businesses to steal a march over the competition.