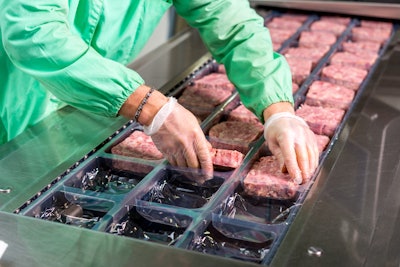
In an industry where prioritizing quality and safety is imperative, food and beverage (F&B) companies often allocate their resources primarily to maximizing profits from low-margin products. However, the repercussions of overlooking quality, safety, and recall issues can be financially devastating for industry leaders.
According to the FDA, a single product recall for a global food company can incur costs of up to $10 million, not to mention the accompanying loss of public trust and business. Unfortunately, investments in quality and safety are typically made only after substantial financial losses have been suffered. This reactive approach not only results in significant financial setbacks but also affects suppliers, customers, and employee morale and efficiency.
After all, who would feel motivated to work in an environment where quality is compromised? So, how can we change this narrative? In today's era of data-driven decision-making, let's delve into how investments in quality software are reshaping industry practices.
Challenges and solutions: Transforming F&B quality management with QMS software
F&B quality management leadership often struggle to manage their department goals simply because they don’t have a “single source of truth” to help ensure equitable and timely governance of their products and manufacturing practices. Running quality management practices via Excel spreadsheets, Word documents, and SharePoint is commonplace within the industry; typically, over half of customers are in this position. These F&B customers struggle to determine the root cause of recurring issues, ensure accurate and on-time SOPs, HACCP, and document revisions and reviews, and most importantly, when a major food safety issue occurs, they don’t even know where to start looking (batch records, tracing exercise, product on hold?). Manual disparate systems provide little to no visibility to make data-driven decisions, without which F&B companies find themselves trying to navigate difficult quality and safety challenges without any real, lasting success.
The core function of quality management system (QMS) software is to ensure the rules/regulations of the industry are consistently and effectively applied to manufacturing practices. The implementation of QMS software will impact all aspects of your business’ performance, from meeting customer requirements to accomplishing the organization’s short- and long-term goals. In turn, your manufacturing plant is in a better position to prevent human and processing errors, reduce waste, communicate effectively across all departments, and improve overall control of your process. When these aspects are properly managed, your business is all but guaranteed to improve the bottom line, have more engaged workers and management, and most importantly, redefine an organization-wide direction to achieve operational excellence.
Bridging the gap: Integrating front-end and back-end quality management
There are two scopes in which to view quality management in the F&B industry: Front-end quality and back-end quality.
● Front-end quality involves day-to-day quality control on the manufacturing floor. Think of any tasks your quality employees would do on a daily basis, including pre/post-ops, inspections, walk-throughs, gauge calibrations, etc.
● Back-end quality management includes everything that the quality management team would be responsible for such as document/HACCP management, NCR/CAPA processes, internal and external audits, customer complaints, etc.
While both scopes are vital for ensuring the highest level of quality and food safety at facilities, it’s common to find a lack of congruence between the two. The main reason often stems from an absence of a unified platform and streamlined communication that enables quick and effective action.
Let's walk through an example likely to have been experienced on the shop floor. If a product lot of finished goods doesn’t pass final inspection, the line inspector will physically tag the lot, have it separated from the rest of production, and go find the supervision. The supervisor would need to review the paperwork on the shop floor to determine what immediate action needs to be taken. Their investigation actions will likely be relatively surface-level and usually won’t incorporate a designated framework approach. Non-conformance reporting (NCR), corrective actions and preventive actions (CAPA) and root cause analysis (RCA) will be addressed later, maybe even 1-2 weeks out, at which point the fine details of the failed inspection will certainly be missed, and the effectiveness of the NCR/CAPA will be greatly reduced. Also, this whole time your product is still on hold!
While this example might be slightly exaggerated, there are inevitably key features that are representative of the inefficiencies and lack of effective communication currently ongoing at manufacturing facilities. With a reactive approach to quality control, your team is always behind the eight ball, and it becomes more about putting out fires rather than preventing them from happening in the first place.
The marriage and seamless integration between front and back-end quality is the key to achieving operational success. The best way to achieve this is having a quality system that integrates both ends of the scope. In doing so, there will be effective and constant communication as well as the necessary escalation required to mitigate quality spills and determine root causes in a timelier manner.
Looking back at the previous example, when a lot doesn’t pass final inspection, in one action, an inspector can automatically place the product on hold in the enterprise resource planning (ERP) system, notify the supervisor, and initiate an investigation process, including the five why process and initial steps (taking pictures, talking to the production team, etc.). Failed inspections can automatically be escalated to NCRs and CAPAs, pulling in the data collected on the production floor so there isn’t the need to replicate information, and the root cause analysis can begin right away.
All of this can be done without even getting the supervisor or management to come down to the production line. While for many F&B companies, this may seem like a pipe dream, advancements in the quality management system enable these types of functionalities to be done out of the box. Even the simple notification and automatic assignment of document reviews will save your team countless hours and avoid audit deficiencies that are common occurrences today.
Unlocking success: The strategic imperative of QMS software in F&B industry
Studies conducted by the American Society for Quality (ASQ) found that companies that effectively implement quality management practices (front-end and back-end quality congruence) experience on average a 9% increase in sales and a 26% increase in profitability. Furthermore, a Harvard Business Review study found that 65% of organizations achieve at least $25,000 in savings within one year of adopting a formal QMS, with 27% saving at least $100,000. On average, a company is able to recoup their QMS investments within 3.5 years.
Investing in QMS software isn't just about meeting regulatory requirements; it's about safeguarding your brand, ensuring customer trust, and driving operational excellence. By embracing technological solutions that integrate front and back-end quality management, F&B companies can not only mitigate risks but also unlock new levels of efficiency, innovation, and competitiveness in an increasingly demanding industry landscape. The choice is clear: adapt and thrive, or risk being left behind in an ever-evolving market.