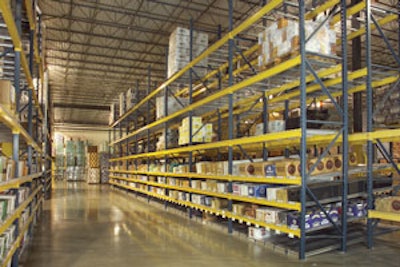
The price of steel is at an all-time high, thanks to heavy demand from China and India, as well as the fact that the U.S. dollar's weakness makes domestic steel a great buy for other nations.
Each month brings additional price increases from domestic steel mills and according to industry sources, prices, which have more than doubled since January, will continue to rise at least until the end of the year.
However, warehouses need additional pallet position more than ever. Before companies make the decision to commit themselves to a racking upgrade, they should consider what their alternatives might be.
"When a company is deciding whether or not to expand its racking system, where it is located can drive what the optimal solution is," explains Ned Bauhof, principal and vice president of Precision Distribution Consulting Inc., a York, PA-based warehouse design consulting firm.
"For example, it might want to consider renting outside storage space during peak times of the year, as opposed to constructing new racking. The affordability differs depending on whether the company is situated in an urban or rural location, as do costs to shuttle goods from the facility to the storage space," he says.
Bauhof also cites the availability of racking in a company's area and the cost to ship it to a location among the factors to consider. If racking still makes sense after all other considerations, it can then determine what type is required.
"There are two ways that a company can affect the cost of its rack purchase: first, it should ensure it's buying the right quantity and then it must make sure it is buying the right type of rack," he says.
An analysis can often reveal that companies don't require as much racking as they thought. They might be able to cut down on their expenditure if they better utilize the space they have, which might involve putting some of their products in cartons or carton flow.
"In our case, we try to take their pallets and cases and cube them into the correct space," says Terry Shaw, director of applications engineering for SSI Schaefer LTD., Charlotte, NC. "We maximize the investment they already have and get it functioning."
Shaw suggests companies concentrate on getting rid of any SKUs that aren't turning for the business. "Why store dead product? Use the space for more profitable product lines."
Understanding a company's business requirements is important in order to avoid wasting money on knee-jerk purchases. For example, buying rack with the intention to merely add capacity can be an expensive mistake if a company sacrifices selectivity in the bargain.
"The direction that the food and beverage industries are going-adding an ever-increasing number of SKUs-means that the ability to get to the right SKU without having to move something else out of the way is vitally important," says Precision Distribution's Bauhof. "Ignoring this factor in a rack purchase can not only hurt a business, but mean a lot of money wasted on high-priced steel."
A Menu Of Options
With the price of racking so high, manufacturers are reporting that their customers are showing a strong interest in leasing their racking systems.
"With racking up 40 or 50 percent, leasing is a little easier for companies to accept these days," says Dennis Hartman, chairman and CEO of Twinload Corp., Southbend, IN. "They can amortize it if they do a five-to-seven-year residual lease and pay by the month for it."
Hartman says that there are different types of leases available, including lease to own as well as residual leases. "It's just like leasing a car. They estimate what the value of the product will be at the termination of the lease period and they take it off up front."
"Racking can also be bought in phases," says Kevin Curry, national accounts manager for Steel King Industries Inc., Stephens Point, WI. "Maybe you don't fill the whole building right now. Maybe you fill half of the building and wait."
Curry suggests companies be conservative during this time of volatile steel prices-and it's not just steel prices that are in flux, he notes. Shipping is up due to diesel prices as is the cost of labor to install the racks.
Pre-paying for racking can also help to reign in costs.
"We're finding that companies can mitigate the risk of higher steel prices by putting significant money down," says Ray Chase, executive vice president for Konstant, located in Rolling Meadows, IL.
"I can't tell them what the steel surcharge will be when they actually need the steel in six months," he adds, "but if they commit to me now and give me 60 percent of the price up front, I can buy the steel and avoid the surcharge when it comes around."
"Then they have to find a way to store it," notes Steel King's Curry. He suggests offsite storage, or having the rack made early and then shipped to the job site, where it's stored under tarps.
"Or, if the building is already under construction and the roof is on, we can put the rack in there and stage it in a corner until it's ready to be installed," says Curry.
Some experts warn caution when considering prepaying for steel. Curry says it's a gamble. The cost is tracking upward right now through 2008, but he says that it may eventually level off or even come down.
"It's like buying a tank of gas," says Dwight Beery, vice president of engineering solutions for Next Generation Logistics Inc., Inverness, IL. "If you get it today it's $3.98. If you get it next week it will be $4.25. The following week, you don't know for sure."
Precision Distribution's Bauhof suggests that another way companies can help minimize the cost of racking is to buy it directly from the manufacturer, instead of going through a distributor.
Searching for a deal when it comes to the cost of racking can result in lower quality racking.
According to Next Generation Logistics' Beery, some manufacturers shave a sixteenth of an inch off their steel in order to get a price advantage. Customers need to review the dimensions of the steel being used in their racking. They should also be aware of the volume of manufacturing the racking supplier does.
"If you have a small rack supplier who is bending his own uprights and punching his own steel, his cost per unit is going to be higher. He might reduce the thickness of the steel or not use an undercoating to compensate," says Beery.
Used Racking Considerations
Companies might want to consider buying used racking from used racking dealers, as a means to avoid the high cost of new steel. There are a number of potential issues however.
"With used racking we run into problems because the customer doesn't always have the specs and he can get into a lot of liability or safety issues because the racks are not used properly," says SSI Schaefer's Shaw. "Sometimes he'll install it in his facility and put a 5,000 pound load on it, for example, when it's only capable of holding a 4,000 pound load."
In addition to a lack of information regarding specs, buyers of used racking don't necessarily know the true condition of the racking they are purchasing. It could be rack that was bent by fork lift impacts and then straightened out-which reduces the tensile strength of the steel. Such damage can be hard to detect once the steel has been repainted.
Experts like Precision Distribution's Bauhof say that used racking can be an effective solution, though, for small installations that involve a few hundred pallet positions. However, companies need to be aware that any savings on the cost of the rack could be eaten away by shipping costs, depending upon where they are located.
"If they can find a used rack supplier in their immediate area, there might be some savings," he notes.
Roll Vs. Structural
Price changes in the types of steel used in racking-roll form and structural steel-could make companies think twice about the type of racking they decide to install. Currently, roll form, which is manufactured in sheets, slit to different lengths and rolled when it's cold, is rising in price faster than structural steel, which is a stronger type that is hot rolled into shapes. This means the real value today is in using structural steel. Companies that typically build their racking systems from rolled form steel could save some money by switching to structural.
Next Generation Logistics' Beery suggests that before companies make a decision about what type of steel to utilize, they should consult with a racking company that supplies both types, tell them what function the rack system has to provide and listen to their advice. In some instances, structural steel, while stronger, does not function as well as roll form.
"If you have a high damage rate because you're using wide trucks in narrow aisles, you're better off with roll form than structural," says Beery. " If you damage the bottom one to two feet of a structural steel rack, the damaged portion can't be cut out and replaced, as is the case with roll form."
The racking experts say that companies planning on new racking projects this year need to get a baseline understanding of what the costs for the project will be by the time they need to purchase the steel.
A current quote won't be good in 30 days after the steel mills roll out yet another surcharge increase. This means that it's important to mutually agree on a way to chart the increase or decrease of prices from the beginning of a project until the steel is delivered.
"You need to sit down with the supplier and say that you understand what the price is right now," says Steel King's Curry, "and you understand that you don't need the rack for five months and in the meantime, you're going to track the price changes together."
The most common way to track these changes is through steel industry websites. Curry says it's a customer's responsibility to stay informed so that he isn't surprised by sticker shock when it's time to pay for the steel.
"You have to be open, pay attention to what's going on and have meetings with your vendor," says Curry.