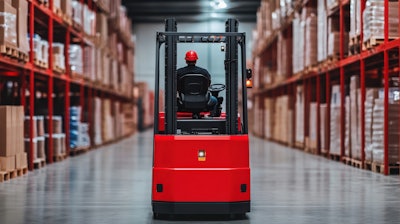
As cornerstones of global supply chain and distribution systems, warehouses play a pivotal role in seamlessly moving goods from manufacturers to consumers, but maintaining these essential spaces comes with challenges. For instance, warehouse and storage buildings account for nearly 8% of total energy consumption in commercial buildings throughout the United States. Additionally, warehousing activities contribute roughly 11% of the total greenhouse gas emissions generated by the logistics sector across the world.
Energy consumption numbers like these point to an important trend in the food logistics sphere: As warehousing needs become a prerequisite for global distribution, abating environmental challenges associated with their operations will be crucial for businesses looking to modernize and remain compliant with industry standards.
The push toward sustainable warehousing practices is more than simply an environmental consideration. Modernizing operations comes with a host of additional benefits, including greater efficiency and productivity, lower operating cost and greenhouse gas emissions; a stronger public image in a market dominated by consumer demand for transparency and responsibility; and — ultimately — higher profitability.
So, what are the best innovations, technologies and practices to adopt in order to create a sustainable warehouse that simultaneously champions productivity and sustainability? Read on to learn the trends leaders looking to create the warehouse of tomorrow should seek to adopt in 2025.
Energy efficiency and clean energy solutions
One of the most significant shifts in warehouse operations involves the transition from traditional, carbon-fueled industrial equipment to electric alternatives. Nowhere is this more evident than in material handling equipment — the conversion to electric forklifts, which now represent 65% of the market, is rapidly improving sustainability efforts while addressing long-standing operating challenges by improving efficiency and utilization.
Consider, for example, the fact that electric forklifts offer a lower total cost of ownership than propane-based alternatives. Although the initial investment may be higher, electric material handling equipment offers savings on fuel, maintenance and repair needs that lead to greater overhead in the long run. With fewer moving parts, no spark plugs, and no required oil changes or tune-ups, electric forklifts address two challenges at once: the high cost of continuous repairs and lengthy downtimes associated with equipment breakdowns and servicing.
Electric forklifts also provide warehouse operators with better handling experience that contributes to a healthier, more sustainable working environment. Fewer vibrations, a quieter ride, less heat and zero emissions improve comfort and reduce on-the-job fatigue, allowing operators to focus on higher-order concerns.
That, and a lack of emissions, creates a lighter carbon footprint, which helps businesses meet consumer demands and remain compliant with industry regulations at once.
To optimize energy use and complement the addition of electric forklifts, organizations should consider implementing integrated energy storage and management systems that combine solar microgrids, battery storage and advanced power management software. These types of systems may allow warehouses to reduce peak energy demand, lower costs and improve resiliency while utilizing more renewable energy. By transforming warehouses into controllable energy hubs that optimize power usage, businesses can reduce their reliance on the grid while ensuring reliable energy for critical operations. These solutions provide a scalable model for warehouses of all sizes to enhance sustainability and long-term cost savings.
The switch to lithium-ion
As businesses move to adapt to more stringent energy regulations, lithium-ion batteries offer businesses another opportunity to optimize. Unlike other power solutions, lithium-ion provides superior energy efficiency, longer run-times, greater capacity retention and faster charging rates, lowering total costs for warehouse managers in one virtually maintenance-free power solution.
Lithium-ion batteries offer rapid-charging capabilities that lead to greater efficiency over lead-acid. Lithium-ion batteries can fully recharge in approximately one hour, significantly reducing downtime and enhancing productivity. Lithium-ion batteries also support opportunity charging, allowing for quick, convenient recharging during short breaks without affecting battery life.
Switching to lithium-ion helps leaders meet consumer demands too. Adopting new, green technologies — such as lithium-ion — prepares forward-thinking organizations to grow sustainability trends as they become industry standards. Lithium-ion helps warehouse managers avoid costly regulatory hurdles while remaining compliant with evolving health and safety regulations.
The rise of automation and smart technology integration
Sustainable warehousing is about more than just energy consumption — at its core, it involves adopting a warehouse-wide culture of continuous improvement that minimizes waste while maximizing efficiency. Enter automation and smart technologies, which enable managers to create streamlined processes that not only reduce energy consumption but also create efficiencies that reduce overall environmental overhead.
One such technology innovation involves the adoption and implementation of mixed, automated lift truck fleets. By relying on a combined network of operator assist technology and autonomous lift trucks, warehouse managers can increase productivity while championing efficient, sustainable labor processes. This does not replace integral operators, who serve vital roles in important positions. Instead, automation advances empower operations to shift focus to more-important job responsibilities requiring greater accuracy and in less time.
Of course, mixed fleets are only one advancement contributing to smoother, more-sustainable warehouse operations. Automation and smart technologies also allow businesses to:
· Optimize picking routes for reduced downtime and lower energy consumption.
· Monitor and adjust equipment usage patterns to improve operational logistics.
· Identify and eliminate costly distribution inefficiencies.
· Predict and prevent maintenance issues before they become larger challenges.
· Accomplish more tasks with less resources, reducing environmental waste.
Recycling and waste management practices
In addition to the adoption of energy solutions and the principles of automation, modern recycling and waste management practices can help organizations create a lean, clean —and, ultimately, more productive — warehouse environment.
Creating the warehouse of tomorrow starts with establishing programs and infrastructure needed to responsibly remove and recycle waste creating circularity where possible. Remanufacturing and refurbishment programs for forklifts and critical material handling components, do extend equipment life cycles and reuse valuable resources for organizations while lowering landfill waste. Other opportunities include implementing lithium-ion battery life cycle management initiatives, which can help maximize battery life spans, and the adoption of reusable components, including switching from disposable absorbent to reusable absorbent pads to reduce nonhazardous waste shipments.
None of these initiatives are certain to work without employee education programs — it’s people, after all, who work to make sure waste and recycling programs are successfully adopted. Organizations can ensure the success of their waste and recycling programs through a mix of in-person interactive workshops and training sessions, digital learning resources and community engagement activities. Establishing employee education programs that foster and maintain a culture of responsibility creates the conditions for a bottom-up approach to waste management, ensuring consistent implementation of recycling practices.
What’s next for sustainable warehousing?
As industry leaders look to the warehouses of tomorrow, three key sustainability initiatives are poised to remake the supply chain sustainability landscape. They are:
· Carbon-neutral warehouses. Reaching carbon neutral in the warehousing sphere is rapidly moving from aspiration to reality, with facilities adopting a series of sustainable fleet solutions, renewable energy systems and other advancements that help offset emissions and reduce carbon footprints. Here, hydrogen fuel cell technology can play a significant role as it has lower, or zero, emissions compared with combustion engines.
· Complex artificial intelligence (AI) integration. AI-integrated warehousing systems stand to improve organizational sustainability in a variety of ways, including by predicting and optimizing energy usage patterns, automating complex processes that reduce efficiency and identifying opportunities for waste reduction.
· Automation and data integration. As automation and data analytics become increasingly integrated, businesses can look to benefits like real-time equipment monitoring and hybrid fleet management tools that simultaneously champion sustainability efforts and streamline warehouse logistics.
Creating the warehouse of tomorrow
There is no one-size-fits-all solution to creating the sustainable warehouse of tomorrow. Instead, achieving greater sustainability takes a collaborative, iterative multifaceted approach involving cooperation across the entire supply chain — from equipment manufacturers and smart technology providers to warehouse operators and beyond.
And while creating the warehouse of tomorrow is no small task, the result is worth it: a sustainable, productive, efficient and profitable infrastructure that exists in harmony with the environment while improving the health and well-being of everyone involved.
But one question remains: What will you do to position your warehouse for sustainable success in 2025?