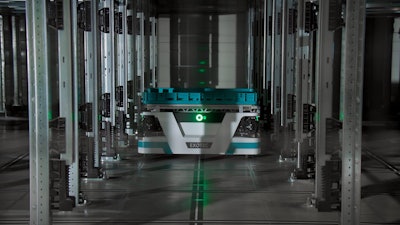
The future of warehouse automation involves emerging technologies, everything from artificial intelligence (AI) and cobots to predictive maintenance, robotics, augmented reality (AR), machine learning (ML) and more.
Present day, these automated systems are revolutionizing the way warehouses operate, driving efficiency, improving accuracy, reducing labor costs, increasing safety and more.
That’s why nearly 63% of warehouse leaders plan to implement AI and AR within the next five years, with 64% planning to increase spending on warehouse modernization, and 63% already accelerating their modernization timelines or planning to do so by 2029, according to a study released by Zebra Technologies Corporation.
The goal: to future-proof cold food chains.
But, “while comprehensive future-proofing is impossible, technology can enhance efficiency, safety, and sustainability through smart monitoring, AI-driven analytics, predictive maintenance, and automation,” says Steve Pullo, EVP, Made4net.
Software solutions, for instance, play an increasing role in maximizing productivity of warehouse automation, says Tim Mosier, sales director, integrated solutions, Swisslog Americas.
“We see increased focus on optimizing execution in the warehouse through the use of AI-enabled software that learns the customer operation to make better decisions, which will begin the move away from common rules-based systems. Given the growing complexity of automation systems, it is also becoming more challenging to have multiple software layers on the systems. Companies need intelligent software that helps make decisions on how to run operations, enables seamless interweaving of manual and automated processes and allows access and control of all aspects of the operation from a single interface,” adds Mosier.
For some supply chain managers, throwing automation into the mix is the answer to improving efficiencies within the warehouse.
“But equipment is only as fast as the humans that run it or must work alongside it,” says Keith Moore, CEO, AutoScheduler.AI. “The integration of robotics amplifies the need for meticulous planning and scheduling. While robots are efficient, they operate based on pre-defined algorithms and lack the intuitive decision-making ability of humans. If a robot encounters an unexpected obstacle or a change in its routine, it requires a set of instructions on how to proceed. These unexpected scenarios can lead to significant downtime without a robust planning system.”
But, when it comes to automating a warehouse, questions arise as how to where to start, what needs to be automated, and why.
Subscribe to our bi-weekly e-newsletter: Cold Chain Insights
“The difficulty lies in the high variability, complexity, and need for human judgment in certain tasks,” Moore adds. “While automation excels in repetitive, predictable processes, areas requiring flexibility, creativity, or nuanced understanding of products remain harder to replicate with current technology. However, advances in AI, robotics, and machine learning are gradually addressing these challenges, pushing the boundaries of what can be automated.”
The elements in a warehouse that should be automated really depend on the company’s needs, says Josh Hartman, market development director, Dematic.
“If you’re looking to start your automation journey, ask yourself a series of questions, such as, ‘What problems am I seeking to solve? What storage and throughput capacity will I need five to 10 years from now? What is my current supply chain network, and will it change? What budget do I have available to invest?,’” says Hartman.
What’s more, “the first kinds of tasks in a warehouse that should be automated are those that are easily repeatable,” says Merry Frayne, product manager, industrial inspections, Boston Dynamics. “This can include inspections such as thermal sensing, visual inspections, and acoustic imaging, all of which are time consuming and monotonous, and if left unchecked, can cost facilities thousands of dollars in downtime. Using robots to complete these types of dull inspections autonomously, and feed the data back to operations teams, allows employees to focus their attention elsewhere.”
Boston Dynamics
Furthermore, cold storage comes with strict compliance rules, and automation is one way to guarantee compliance, according to Andy Williams, EVP, sales North America, Exotec.
“Other areas that should be automated are places where you can see increased efficiency. A good place to start is to identify time-intensive, manual processes that eat up a lot of your team’s time. De-palletization and palletization are good places to start in cold storage. Businesses can easily automate this process, decreasing the time it takes for goods to be processed and to reduce potential errors,” adds Williams.
However, some processes, such as handling fragile items, oversized products, quality control, custom kitting, and complex problem-solving remain difficult to fully automate due to technological limitations and complexity, says Andrew Wallen, director of distribution, ITF Group.
“Therefore, a collaborative approach, combining human workers with automated systems, often offers the most effective solution,” he adds.
New solutions to future-proof supply chains
To help the cold food chain space automate for the future, companies are bringing to market a host of AI-focused solutions designed to future-proof warehouse operations.
For starters, AutoScheduler.AI introduced AutoPilot Central, a centralized warehouse orchestration that gives companies an aggregated bird's eye view across multiple sites, allowing managers to rank the sites and take corrective action for areas out of service to mitigate risk across the network.
Swisslog
Meanwhile, Swisslog collaborated with La Réserve des Saveurs to create a fully automated storage/preparation facility using the AutoStore multi-temperature solution to enable tri-temperature management. This allows fresh, frozen and dry products to be stored simultaneously, while eliminating the need for traditional cold storage.
Made4net partnered with Gather AI to enhance inventory management through AI-driven drone technology. This collaboration integrates warehouse management systems (WMS) with cutting-edge drone inventory solutions for improved inventory accuracy, streamlined operations, and reduced costs.
In February, Exotec launched the Next Generation of Skypod system, an all-in-one robot-based automated storage retrieval system (AS/RS) that comes with a number of design improvements such as a new and more compact Skypod robot, a workstation for robot-to-robot picking, high-throughput Exchanger, and denser storage.
“The system actually first stemmed from a challenge from one of our grocer customers– E Leclerc Seclin. After the global pandemic, they saw a huge uptick in customers doing curbside pickup. As the amount of customers increased, they needed a better way to balance the flow of goods and customers for pickup,” says Williams. “We provided them with a high-density, flexible storage and retrieval system with a number of key benefits to increase efficiencies. For example, the Next-Gen Skypod system’s Integrated Buffer allows for efficient order storage and ensures quick reactivity, optimizing space within their site while accommodating the different temperature requirements various goods may need. Further, our robots are capable of handling both cold and ambient temperatures without the need for additional hardware. Customers can confidently shop online knowing the items they receive when they come to pick up are fresh and they’ll receive their goods in a timely manner. Initial results are incredible; they’ve seen a 73% reduction in customer wait time from 15 minutes to 5 minutes.”
Boston Dynamics implemented enhancements to Spot, its mobile robot. New is an acoustic vibration inspection, enabling Spot to perform ultrasonic inspections of rotating equipment to detect early indicators of bearing failures, air leaks, out-of-range gauges, equipment running hot and more before they cause a breakdown.
Additionally, Spot has become a key part of AB InBev’s “Brewery of the Future” program, which invests in emerging technology to support the company’s goal of achieving net-zero operations at its Leuven, Belgium, facility by 2028. Spot conducts 1,800 individual inspections each week across 10 packaging lines that churn out over 50,000 containers of beer every hour.
Meanwhile, Dematic, a member of the KION Group, is collaborating with NVIDIA and Accenture in a recently announced partnership focusing on AI-powered solutions and digital twin technology. Leveraging Dematic next-generation cloud native software and NVIDIA “Mega” Omniverse, this partnership will allow customers to enhance and optimize operations through modeling simulations.
Dematic
“For the food and beverage industry, and specifically cold chain, high-density storage is important to maximize your footprint and keep the temperature consistent,” says Hartman. “The more open a freezer warehouse, the more warm airflow from outside can create temperature variances. High-density storage solutions such as pallet crane-based automated storage and retrieval systems (AS/RS) and pallet shuttle technology offer scalability, multiple SKUs per put-away lane, and even higher throughput. To continue providing these solutions to customers, KION recently signed an extensive partnership with one of the leading pallet shuttle providers, Eurofork.”
In the last 12 months, ITF Group launched Robopac S7 portable stretch wrapper, which gives the flexibility to move the pallet wrapper closer to the work area, thus reducing travel and employee downtime when unloading containers and wrapping non-standard and standard pallets. It also released Proxy Click, a digital visitor log, and Conduit, which offers an advanced dock management system tailored for third-party logistics (3PL) providers. The platform provides automated dock scheduling, client-specific customization, cross-docking support, automated driver check-in and compliance monitoring.
When is automation too much?
Although warehouse automation provides a host of benefits, at what point does the automation become too much?!
“The warehouse needs people, but we need to augment them with appropriate technology, whether advanced AI or automation technology, to help them do their jobs more effectively,” says Moore. “Advanced AI is not necessarily a cure-all for the supply chain, even though some vendors tout this. Every disruptive technology has a cycle—a maturity cycle and an adoption cycle—and we are not there yet.”
“There are many AI tools that people can use to make their jobs easier, however, with AI, replacing people within the supply chain is a long way away,” he adds. “Yet, the jobs of tomorrow are going to be different. People need to prepare for the skills they need to rise above the crowd. They need to be prepared to accept technology, whether AI, or automation, or other, and learn how to work with it and alongside it.”
The cold food chain is one of the most complex and challenging areas of the supply chain, with countless variables that can impact product integrity, regulatory compliance, and operational efficiency, says Pullo.
“From temperature fluctuations to evolving customer demands and supply chain disruptions, businesses need a way to control what they can—starting with their inventory,” he adds. “For any company in the cold chain, investing in the right WMS isn’t just about efficiency—it’s about ensuring product quality, meeting regulatory requirements, and maintaining the trust of customers in an increasingly volatile supply chain landscape.”
For those in the cold food chain, automation is table stakes, Williams says.
"Increasing technology completely reduces the difficult elements of cold storage supply chains, allowing businesses to focus on other elements of the work and for customers to be more confident stores are stocked with the items they need the most, when they need them. It’s truly a win-win addition to these warehouses,” he adds.
“It's also worth noting that cold chain warehouses require a much higher capital expenditure than ambient or air-conditioned warehouses, making ‘downtime’ much more crucial,” Hartman adds. “The inventory loss due to ‘downtime’ can create significant profit losses and impacts the ability to fulfill orders throughout the entire supply chain. Because of this, preventive maintenance is even more important in this industry and requires real-time performance monitoring of equipment that can alert an engineer of impending break down.”
“With all of that in mind, companies should focus on automating highly labor-intensive or complex manual operations, such as picking cases of product to place on a pallet or conveyor belt or preparing batches of varying SKUs for e-commerce orders. Complex tasks that require manual labor often lead to reduced accuracy,” Hartman adds. “Consider increasing facility utilization or freeing up space to expand factory floor operations, as this is where value is being generated. This can be achieved by implementing high-density storage solutions for pallets or cases.”
Another element of a warehouse that should be automated is visibility and tracking capabilities, Hartman says, to provide visibility into inventory, order management, and basic functionality.
Moore advises focusing only on the parts that should be automated such as material handling, picking and packing operations and inventory tracking.
“If you’re looking to start your automation journey, ask yourself a series of questions, such as, ‘What problems am I seeking to solve? What storage and throughput capacity will I need 5-10 years from now? What is my current supply chain network, and will it change? What budget do I have available to invest?’” he adds.
FSMA 204 and warehouse automation: What gives?
Earlier this year, the newly updated Food Safety Modernization Act FSMA) 204 Rule now applies to all foods on the FDA's Food Traceability List (FTL). This list includes everything from dairy and produce to vegetables, fish and ready-to-eat salad kits.
What’s not on this list is how changes in these rules impact the cold food chain, specifically with regards to implementing warehouse automation solutions.
While this regulation does not specifically require automated solutions, it also doesn’t mean emerging technologies shouldn’t be considered as possible solutions to achieving the ultimate in food safety.
That’s because automation can focus on areas where the risks of contamination or temperature deviations are highest, such as receiving docks, cold storage zones, and loading areas, says Moore.
“Automated temperature and humidity control systems are needed to maintain product integrity and meet FSMA requirements. In shipping and receiving areas, automation needs to focus on time-sensitive guidelines to minimize the risk of improper handling,” he adds. “AutoScheduler integrates with existing warehouse management systems (WMS) and transportation management systems (TMS) to provide a unified view of inventory, orders, and storage conditions. This real-time visibility ensures that every movement of temperature-sensitive goods is accurately tracked and recorded, meeting FSMA's traceability requirements.”
Technology and automation, for instance, are often ideal options to ensure timely and consistent compliance, says Hartman. “Required Key Data Elements such as origin information, transformation information, shipping information, receiving details, and more would be highly difficult to accomplish through manual or semi-automated processes. Blockchain technologies are emerging as a powerful tool to help companies comply with FSMA requirements,” he adds.
What’s more, warehouse automation provides a more consistent and reliable digital footprint, adds Mosier.
“From receipt, storage and when it is loaded on the outbound trailer, inventory is recorded and tracked, providing companies the data needed to locate, retrieve or trace inventory at any given time,” he adds.
Regardless of where your operations stand in light of FSMA 204 compliance (which goes into effect Jan. 20, 2026), or what your company stands in terms of implementing automation, the time to automate is now.
That’s because at the end of the day, these automated systems are revolutionizing the way warehouses operate, driving efficiency, improving accuracy, reducing labor costs and increasing safety. When implemented in the right way – and in the right place – warehouse automation can be just right.
This is Part 1 of a 3-Part Series.
Check out this 3-part series on:
Part 2: Breaking down the implementation journey, and
Part 3: Curbing cargo fraud