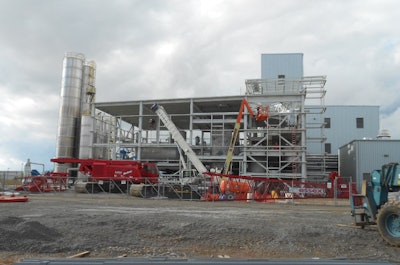
The worldwide response to the Coronavirus disease (COVID-19) continues to be dynamic. Most industries, including construction, are trying to remain as active as possible while adopting various health and safety precautions. Extra challenges attend restarting capital projects that were delayed, descoped or re-phased earlier in the pandemic. Interruptions and extended shutdowns during the construction phase of a capital project can lead to significant additional costs. To mitigate such costs, construction industry owners, contractors and suppliers must review and re-assess previous plans, safety approaches, supply chains, workforce availability, schedules and benchmarks.
The first question to be asked is—does the project still meet the business’s needs? The pandemic altered many market forces, especially those affecting food processing, storage and distribution. E-commerce, even for perishable items, is on the rise. Panic buying during the pandemic revealed challenges within the food supply chain, which in turn fueled—and continues to fuel—even more consumer stockpiling. The increase in online grocery shopping has driven a demand for more cold storage facilities, in particular—and current vacancy rates for cold storage facilities are among the lowest in the industrial real estate big box sector. These changes in the market, and others, should be carefully addressed when re-evaluating delayed construction projects, as they will significantly impact how industrial facilities are utilized. Building size, configuration, installed equipment and more—even the overall feasibility and ROI of the capital project—may need to be reconsidered.
It is a given that the schedule for a delayed project will have to be renegotiated. New goals and timelines must be determined with a careful eye kept on associated costs. Safety procedures related to COVID-19 will also affect cost and schedule. Some, such as social distancing, sanitizing, disinfecting, and cleaning requirements need to be addressed early, so a plan can be implemented to avoid any impact to progress on the jobsite. Training and health screenings will also be needed.
COVID-19-related safety requirements will affect facilities’ eventual operations, as well, and these requirements should be factored into the new round of planning. For example, space may need to be allocated for socially distanced workstations, new traffic patterns through the facility that minimize personal interactions, checkpoints for assessing employee health, and additional hygiene/sanitary stations.
The construction industry’s longstanding workforce shortage has only been exacerbated by the pandemic, so contractors and labor may be more difficult to procure. Regional labor pools will need to comply with various state and local regulations pertaining to COVID-19 such as travel restrictions, etc., potentially impairing a contractor’s ability to ramp up to meet schedule commitments. Food warehousing and distribution facilities may face special challenges, since many under-construction buildings are located in zones (such as urban lots) that have not typically experienced warehouse construction in the past and do not have an existing workforce near the location.
In addition to labor costs, the cost of materials, critical process equipment, fabrication and more may have changed as a result of the pandemic. Lead times may be longer than before. Again, urban facilities and specialty facilities, such as freezers and refrigerated spaces, may experience particular difficulty in getting specialized equipment and materials to the site.
A collaborative approach to reassessing the project
Communication, collaboration and flexibility are key to navigating the difficulties of resuming a delayed project. Having project stakeholders work together as a team was important even before the pandemic, considering the ever-growing complexity of capital projects. It is even more important now. By engaging contractors early in the re-evaluation process, owners can benefit from effective collaboration and analysis. Applying the principles of early contractor involvement (ECI), contractors and owners can work together to achieve greater certainty in terms of estimation/cost, project planning, safety, communication, constructability, and risk management. This approach also reduces errors and changes in latter project phases.
Owners and project representatives should communicate with all contractors, suppliers and vendors one-on-one, confirming that they are still available and re-examining variables. In addition to confirming the availability of previously selected contractor companies, it is wise to confirm that key individuals from the previous project team are still on board.
Assess where contracts and financials stand, including construction work that has been completed and/or paid for. New contract terms and conditions, as well as project documentation, may be required to address COVID-19-related liability. A re-examination of all parties’ insurance policies and coverage is advisable.
Before resuming construction, it is important to perform a site assessment to verify that conditions on the ground match documented work and current building models. The status of permits should also be reviewed.
Finally, don’t assume that things are on an uninterrupted path to getting “back to normal,” even with vaccinations rolling out in 2021. Continued disruptions, or even further site shutdowns, are still possible. Maintaining flexibility is critical; while it is impossible to foresee exactly what will affect the project as time goes on, multiple “if/then” scenarios can be established and accommodated. Perform cost-benefit analyses that can be used in the event of new disruptions to inform which aspects of the project should be fully stopped and which can be merely slowed. Prepare site security measures that can be quickly put into place.
For the food industry, responses to COVID-19 accelerated may changes in consumer habits, dramatically affecting product supply and demand. While it is time to carefully resume capital projects that were put on hold, the eventual success of each project depends upon proceeding cautiously and using all available data—as a team—to make changes in strategy. Future-focused planning should consider the short-term possibility of ongoing COVID-19 “hot spots” and associated slowdowns as well as the long-term changes in e-commerce and hyper-local distribution locations that are likely to remain with us.