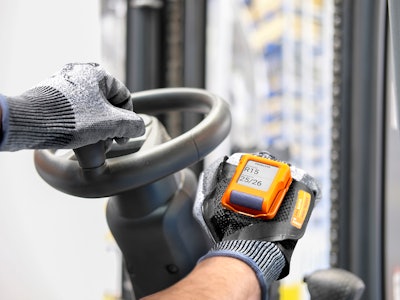
How should logistics and supply chain managers prepare for the next crisis? Flexibility is definitely a crucial prerequisite. You want to be in a position to set up, re-locate or redesign workplaces quickly. The same goes for the underlying processes. Here are considerations for both improving safety and efficiency in the supply chain.
Work-related accidents are a problem
Employers have a duty to keep the workforce safe. But, every industry comes with associated risks. Slips, trips and falls, injuries from lifting or being struck by a moving object are some of the hazards that could cause harm across the supply chain. According to the Bureau of Labor Statistics, there were 888,220 non-fatal injuries and illnesses that caused a private industry worker to miss at least one day of work in 2019.
Worker fatigue is one element that can significantly contribute to increased risk of injury at work. Some 25 million people are employed as shift workers in the United States. Badly designed shift-working patterns and long working hours that do not allow for sufficient periods of rest and recovery can result in accidents, injuries and ill health. With slower reaction time, memory lapses, lack of attention and reduced coordination, it can have severe ramifications at the workplace. The National Safety Council estimates the total cost of work-related injuries in the United States in 2019 was $171 billion.
Stop bad habits
A first key objective is to prevent employees reverting back to old habits that could endanger them. Smart wearables can play an important role in enabling social distancing on-site. Some companies provide an app that connects to the workers’ wearable scanners. The app detects when workers fall below the minimum distance for too long. In response, it generates a message that the wearable device can output as a combination of acoustic, haptic and visual warning signals. Particularly in busy or noisy work environments, combined signals are extremely helpful for attracting employees' attention. This type of technology is particularly well suited to help workers at the assembly line or in logistics by providing this uncomplicated reminder to keep the right distance.
Technology that can reduce risk
Hands-free wearable technology can benefit the safety of workers. Ergonomic workspaces aim to decrease the risk of repetitive strain injury and accidents resulting from fatigue and exhaustion. By removing unnecessary repetitive actions, such as time-consuming walks across the warehouse, wearable technology can ease the strain on the worker by avoiding extraneous tasks.
Workers could immediately be notified of the next pickup location via their wearable device, rather than having to trek back to retrieve this information. Not only does this reduce the risk of health problems and injuries from strain, but productivity is also increased as workers will have higher energy levels. By ensuring that the majority of physical movement is directly linked to necessary duties, risks can be avoided by minimizing extraneous movement and avoiding additional weight. Lightweight, ergonomic scanners provide a safeguard for employees, protecting from musculoskeletal disorders.
Making the picking process safer
Considerable potential to both increase efficiency and safety measures may lie where businesses would least expect. Order picking is a perfect example, particularly travel and picking times for employees. Travel time accounts for 30-50% of picking time, and includes the time a warehouse worker needs to reach the goods and return to the picking area. Shortening the distance significantly contributes to improved order processing time. The same applies to picking time, i.e. the interval from first contact with an item through transport to the storage location, to depositing at the storage location. It’s particularly important to ensure the item is picked accurately so that the entire picking process does not need to be repeated. This is where smart glasses or wearable devices are recommended. Scanning articles as they are picked and having access to real-time information improves both picking accuracy and efficiency.
Removing bottlenecks in the process
Bottlenecks arise within companies’ processes due to external as well as internal conditions. For example, fluctuations in demand and dynamic markets represent major challenges for production. In addition, complex structures within technical processes, process organization and logistics are also susceptible to errors and inefficiency. The more complex the internal structures, the more difficult it is to understand where and why bottlenecks occur. Long throughput times, underestimated forecast qualities regarding demand or overfilled warehouses with semi-finished goods are typical examples of the negative consequences that arise from a bottleneck, but they are often not the hurdle itself. It’s crucial to understand the original problem impacting production and logistics.
Ultimately, the aim is to optimize material flow and increase throughput times. It is clear that the time factor is often associated with faster processing. However, just looking to accelerate existing processes on a broad scale will not always deliver the desired increases in efficiency. Rather, they must be reviewed and optimized on an individual basis.
To achieve this, unnecessary processes within the value chain should be eliminated. By connecting the various departments and machines, waiting times can be reduced. Furthermore, transit times to terminals or similar workstations with industrial wearables can be avoided. The employee should receive all important information directly at the workplace and be able to share it from there.
In logistics, organization via barcodes is a common method of identifying products and their position in the warehouse quickly and easily. One of the advantages of barcodes is that any information can be stored and transferred to the warehouse management system by means of scanning.
But, this method can also be optimized. Often, information is sent to a computer terminal that the employees first have to walk to. This costs time and interrupts workflow. In addition, scanning with conventional barcode scanners is error-prone and not ergonomic.
The barcode scanner itself is a major cost factor for many companies. They are usually not very robust and susceptible to damage. There is also the risk of the scanners being inadvertently packed and sent with deliveries.
An alternative to the classic barcode scanner gun is the glove scanner, which is also available with an integrated display on the back of the hand. Employees wear the scanner directly on their work gloves and do not have to keep picking it up again and again. In addition, processing at the terminal is no longer necessary, as the information can be sent and received directly from the workplace, enabling greater flexibility and less travel time for the worker.
A more efficient, safer and connected future
As supply chain managers prepare for the future dominated by uncertainty and the Coronavirus disease (COVID-19), workplace health and safety has become increasingly important. To improve safety, there are several factors to review. This includes assessing old workplace habits and routines and updating them; using wearable technologies to help manage social distancing and other health and safety scenarios; and consider how ergonomics and wearable technologies can reduce workforce fatigue and how it can make picking processes better and remove operational bottlenecks. Technology, especially wearables, can significantly help connect the workforce and keep it safe, productive and efficient. Are wearables part of your future strategy to connect and digitize workers?