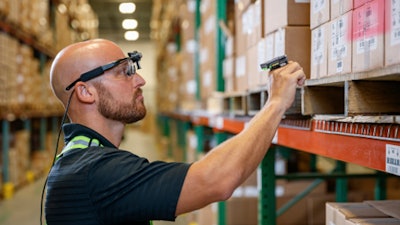
The growing desire for next or same-day delivery options has accelerated the rate at which warehouses need to move products through their facilities. Today’s consumers have grown used to these delivery choices when ordering products online, and are likely to shop with a competitor if they can more quickly receive the same item. This shift in the industry, combined with the labor shortage that still exists, can make the task of operating a warehouse more difficult than ever before. While warehouse operations managers were already accustomed to increasing demands, the Coronavirus disease (COVID-19) pandemic has furthered the strain on supply chains. Having a practical understanding of how to quickly leverage new technology to increase warehouse productivity will help keep warehouse operations at peak performance levels.
Identifying current automation capabilities
It’s important for warehouse operators to understand how automation fits into their organizations’ strategic goals before adopting any new technology. Zebra’s Warehousing Vision Study found that warehouse decision makers’ current focus is on operational outcomes that are in the early phases of warehouse modernization. This typically includes the adoption of fundamental barcoding and mobility solutions that help to gain basic control of business operations through improved individual worker productivity. As organizations begin to take advantage of their warehouse management system (WMS) with mobility, workers can access timely data for more efficient decision making and achieve significant improvement in their sensing capabilities.
This is done through aggressive data capture of assets and workflow processes to enrich WMS data. With this, workers communicate more efficiently for improved team productivity and greater workflow conformity. In these initial phases, the goal is to build a “best-in-class” mobility strategy in which technology is optimized for the ergonomics and operational tasks. Among the many ways there are to optimize the use of mobility, leveraging wearable technologies is one popular way to achieve optimization, with robotics gaining a lot of attention as it becomes more accessible to businesses of all sizes. It’s important for warehouse operators to recognize this process doesn’t happen overnight, and not all businesses will transition through the phases at the same pace or in chronological order. By breaking warehouse modernization down into smaller, manageable chunks guided by a strategic framework, warehouse operators can more easily achieve their long-term goals instead of becoming quickly overwhelmed.
Targeting paper-based processes
One of the earliest and easiest steps that warehouse operators should take in their modernization journey is the elimination of paper-based processes. The days of printing a pick list at the beginning of the shift are over. With the volume and velocity of order fulfillment today, arming staff with electronic work orders, pick lists, put-away and transfer instructions make picking, packing, staging and shipping more efficient and dynamic. The simplest way to do this is to send task assignments and step-by-step instructions via handheld mobile computers, tablets or vehicle-mounted computers. Also, many workers benefit from wearables that offer visual or voice-directed guidance paired with hands-free scanning that give workers direct access to the WMS. They also help improve individual productivity and efficiency as well as data capture and task completion accuracy.
Wearable mobile computers are ergonomically designed to be worn on the forearm and use touchscreens and keypads to aid with workflows, allowing workers to access WMS instructions to perform the right actions. This design makes the devices more comfortable to wear for extended periods of time and are less taxing on the user. There are also ring scanners that allow for easy, hands-free data capture and item verification, as well as comfortable enterprise heads-up displays that support assisted reality applications for fast, safe picking and put-away actions. The industry is seeing a growing shift in the need for these types of devices as Zebra’s most recent Warehousing Vision Study found that improving worker comfort and ergonomics are among surveyed warehouse leaders’ top labor initiatives over the next five years.
Barcode scanners can also be attached to the wearable so mid- to long-range 1D and 2D barcoding functions can be ergonomically incorporated with the worker’s natural range of motion. Wearables also provide workers with the ability to collaborate via voice and sync with Bluetooth-connected auxiliary devices such as mobile printers. This helps to reduce the amount of time workers spend walking to and from their computers for queries or to and from stationary printers to retrieve labels.
Robots augment human associates
Another technology solution receiving a lot of attention for its ability to transform warehouse operations is robotics. Smart robots come in many shapes and sizes depending on their intended use, and in some cases, are increasingly offered in the form of robotics as a service (RaaS), making it easier for companies to increase or decrease their investments based on the needs of their businesses. The most popular form of robotics in the warehouse are collaborative robots, commonly referred to as co-bots or autonomous mobile robots (AMRs), which help move assets through the warehouse to save workers time and energy. By utilizing cobots, warehouse operators can reduce the burden of manual tasks placed on their associates, freeing them up to focus on more high-value tasks. Using a cobot in place of an associate can dramatically decrease the number of steps an employee takes each day.
For example, automated guided vehicles (AGV) rely on new infrastructure to create specific pathways in the warehouse, enabling mobile workers to know exactly where the robots will travel for a repetitive workflow that rarely changes. Autonomous mobile robots (AMR), which are similar to robotic vacuums found in many households, learn the layout of their environments and typically leverage barcode markers are placed throughout the warehouse to provide waypoints that correspond to shelf locations.
Warehouse modernization: next steps
Warehouse operators with a modern WMS can take advantage of modern mobility and scanning technologies relatively quickly without a huge lift from their IT departments, and will find there is little training needed for workers to start using these devices. In fact, the productivity gains may be noticed quite quickly, especially if the solution interfaces include gamification to create healthy competition toward operational key performance indicators (KPIs). And, though it can seem a little daunting at first to make a sudden commitment to cobots, the right implementation (and partner) will make it easier to incorporate this more advanced technology solution into everyday workflows. Warehouse operators who are ready to start their modernization journeys will find there are plenty of options to suit the needs of their businesses and secure a swift return on investment.