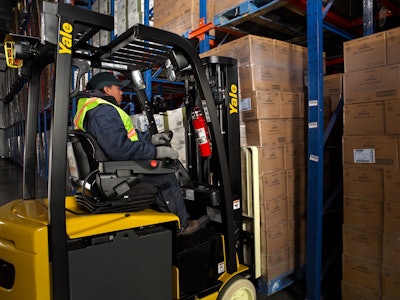
In 1917, the beginnings of the forklift started when the Clark Company first released its tructractor, which was known as the first internal combustion-powered industrial truck. From there, the Yale Materials Handling Corporation created the first battery powered high-lift platform trucks, leading to the modern forklift.
Lift trucks of today look very different from their predecessors, but complete the same task. One of the more noticeable differences is the advancement of robotics, pushed by not only the advancement of technology, but also a lack of workforce, unfavorable working conditions for human in cold warehousing where temperatures are extremely uncomfortable, and as of late, the need for social distancing.
The food and beverage sector sees the most use of robotic lift trucks, according to Kevin Paramore, emerging technology commercialization manager at Yale Materials Handling Corporation, in tandem with the consumer packaged goods sectors.
Cold warehousing becomes more efficient with technology-enabled lift trucks.Yale Material Handling Corp
“Getting to that stage of actually transferring to robotic lift trucks requires a true picture of forklift operations,” he says. “While it sounds simple, this accurate baseline isn’t something most facilities have–they have gaps in the understanding of exactly what forklift operators do. For example, while obvious jobs like unloading pallets may be accounted for, tasks like labeling pallets or latching trailers may not be recorded.
“As more types of lift trucks are available as robotic solutions, that opens up greater opportunity for lift truck fleets to be automated. For example, Yale offers four types of robotic lift trucks—an end rider, tow tractor, counterbalanced stacker and robotic reach truck. The robotic reach truck is the newest option, and breaks new ground for a robotic lift truck solution. Rather than just handling floor-level load transportation tasks, the robotic reach truck is capable of autonomously depositing and retrieving loads from locations as high as 30 feet and reaching into double-deep storage.”
The ability for a robotic arm to lift as high as 30 feet paves the way for a wider range of sophisticated tasks, which maximizes use of these solutions and achieves a faster return on investment.
Bridging the labor gap
Partners now look for faster and faster lead times, making the need for automation exceedingly necessary for cold warehousing partners that want to deliver high-quality customer service. Because the job is sometimes so physically demanding and working temperatures are so cold, new technology is necessary to not only fill the labor gap, but also create an enjoyable work environment for employees.
“Difficulty finding and retaining labor is a common challenge in the supply chain,” Paramore says. “Annual turnover in the warehousing sector in 2019 was 46.1%. Working in the warehouse can be a challenge–operators take thousands of steps and move tons of weight shift after shift. But, businesses also face extreme cost pressures and razor thin margins, with consumers demanding lower prices, faster service and high-quality products.
“Success requires setting up operators for success, equipping them with the right tools (lift truck solutions) and putting them to work in the proper workflows. For cold applications in particular, operator comfort is an important consideration, and there are options available to create a good work environment and help operators cope with cold temperatures. For example, heated grab handles, floors and cabins, along with controls designed for use with gloves can help increase employee comfort, productivity and retention.”
Cold warehouses can buy packages for lift trucks geared specifically to the cold chain, equipping vehicles with technology to help employees keep warm. For instance, Yale offers a sub-zero freezer package for areas where temperatures can reach -40°F that includes low viscosity hydraulic fluid, sealants, heater on steer feedback potentiometer and heated multifunction display.
Battery life
In addition to comfort, the lift trucks themselves need to operate in such cold conditions, making power source an important part.
“For cold operations in particular, selecting the proper lift truck power source requires special consideration of operating temperature, as different power sources perform better than others in extreme temperatures,” continues Paramore. “For example, lithium-ion batteries are a strong choice for cold temperature food handling operations. As an electric source, they avoid the emissions of internal combustion engines, but unlike other electrification options, they can operate in a broad temperature range, from -40°F to 113°F.”
The Raymond Corporation recently launched a new generation of lithium-ion batteries for its lift trucks for faster charger power solutions and allows for greater insight to battery life and health.
“Energy Essentials distributed by Raymond enables complete and unique integration between the truck and battery, giving full visibility to operational data elements that include state-of-charge and fault codes,” says Jennifer de Souza, senior director of energy solutions, procurement and leasing, The Raymond Corporation. “Engineered to excel in the toughest material handling applications, these lithium-ion solutions provide our customers with significant productivity enhancements, including increased uptime and reduced electricity costs.”
Similarly, GNB Industrial Power released a new lithium-ion battery that allows for greater insights, wall charging and better efficiency.
Maintenance insights
These batteries don’t have the stronghold on maintenance and health insights. This type of data is now available from the lift trucks themselves as well.
“Lift truck telemetry is another opportunity to monitor fleet size and structure and help optimize maintenance–especially important for assets working in tough environments like refrigerated and frozen food facilities,” says Paramore. “With the ability to evaluate utilization and maintenance information alongside expected demand and specific truck applications, fleet managers can make quick and informed decisions about fleet size and composition. This helps them continuously improve operations and maintain a right-sized fleet composed of equipment tailored to meet their specific operational challenges. With telemetry system data, operations can right-size fleets to eliminate the cost of running excess trucks.
“While a lean truck fleet eliminates idle time and reduces cost, it leaves businesses with a low tolerance for downtime,” he says. “With insufficient fleet availability to serve demand, operations can endure significant costs such as delayed shipments and lost revenue, placing a premium on preventive maintenance and fault code monitoring. Properly utilized telemetry analytics can help refine preventive maintenance schedules to ensure sufficient support while avoiding overspending.”
The lift truck of today is able to last for quite longer, complete more complicated tasks as well as a wider range and even operate itself. As technology grows, the lift truck will only grow with it. Right now, this material handling equipment will help to fill in the gaps where COVID-19 and other factors leave holes, and will likely remain long after the pandemic is over.