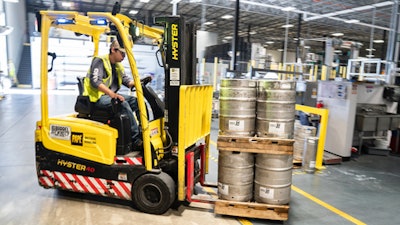
Consumers have become more environmentally conscious in recent years, and are looking for corporations to do the same, thus driving the supply chain industry toward a growing trend in sustainability.
Fortunately, as more companies extend their commitments to responsible business practices, they’re also seeing that it’s a win-win proposition. One way that businesses are becoming “greener” or more energy efficient is by selecting the best energy source to power their material handling equipment. While there are several energy sources available to power material handling equipment, including forklifts, propane has proven to be the best option.
By managing and improving environmental and economic performance with propane, businesses can decrease their carbon footprint, enhance worker safety and comfort, increase productivity and lower operating costs.
Emissions edge over other energy sources
The energy source chosen to power a business’ equipment can have a significant impact on its sustainability efforts. Luckily, propane is a clean, low-carbon alternative fuel that can produce significantly fewer emissions than diesel and electricity in a wide range of applications.
Many material handling professionals overlook electric’s full emissions profile and assume it’s the cleanest option, so they may be surprised to learn that’s not the case. When taking into account the site-to-source emissions required for bringing electric forklifts to market, propane is actually a better low-emissions option than electric. Site-to-source emissions include all the emissions produced at power plants where electricity is generated — many of which are still coal-fired — as well as the emissions during transportation to the facility. According to an emissions analysis conducted by the Propane Education & Research Council (PERC) and the Gas Technology Institute (GTI), propane can reduce SOx emissions by 76% compared with electric forklifts.
The battery production and disposal processes are dirty, too. Many of the raw materials used to produce batteries are harmful to the environment. For example, the mining and processing of metals such as lithium, copper and nickel require a lot of energy and can release toxic compounds. Plus, for raw materials like nickel and graphite, producing countries cope with water contamination and deforestation.
And, when an electric forklift battery goes dead, facility managers can’t simply dispose of them without negatively impacting the environment. Because the Environmental Protection Agency (EPA) considers them a hazardous material, they have specific handling and disposal regulations attached.
The study also revealed that propane is far cleaner than diesel equipment. The comparative emissions analysis, which analyzed full fuel-cycle energy consumption, greenhouse gas and criteria pollutant emissions (nitrogen oxide and sulfur oxide), found that best-in-class propane forklift engines can produce 97% fewer hydrocarbon and NOx emissions when compared with similarly-sized diesel forklift engines and without any drop-off in payload or power. Plus, operating propane equipment results in cleaner air and when crews work in a cleaner environment, they’re more likely to be productive. Not to mention, toxins released by diesel equipment are proven to irritate respiratory issues like asthma.
More productivity and a better bottom line
As companies implement sustainable practices, they have to make sure it makes business sense, too. With propane, businesses can attain a sustainable operation all while maintaining performance and productivity levels — and even keeping costs in check.
Propane forklifts provide crews with long-term productivity and performance, 100% power throughout operation and the ability to push heavy loads at full capacity longer than electric equipment. Propane offers the versatility to tackle the job at hand whether it’s a small task or a heavy lift — inside or outdoors. Plus, propane saves crews downtime for recharging. Swapping out an empty propane cylinder for a full one takes just a few moments, and eliminates the need for additional expensive, heavy batteries, downtime spent recharging, or strict battery management by crews — like with electric equipment. Businesses can also set up a tailored refueling schedule with their local propane supplier to ensure that cylinder cages are always full.
Beyond maximizing productivity, businesses operating on propane can see significant savings over time compared with electric and diesel forklifts. According to a survey from PERC, fleet managers rated initial capital cost as one of the Top 5 important factors when purchasing a forklift. Propane forklifts have a 30% lower capital cost compared with electric forklifts. And, electric forklifts are costly when considering the utility costs of keeping them charged. Battery life and power output for electric forklifts also diminish over time and lead to future costs that can go overlooked, too.
On the other hand, propane forklifts have a longer lifespan. The life expectancy of a propane cylinder is three times longer than the life expectancy of an electric forklift battery and extends beyond the typical lifespan of a forklift. And, propane-powered forklifts can be refilled at any time without affecting the lifespan of the cylinder.
As companies prioritize their environmental and economic impacts, they’re finding that it makes good business sense and ultimately, is the right thing to do. And, as the shift toward supply chain sustainability continues to gain traction, many businesses are turning to propane for its low-emissions profile.