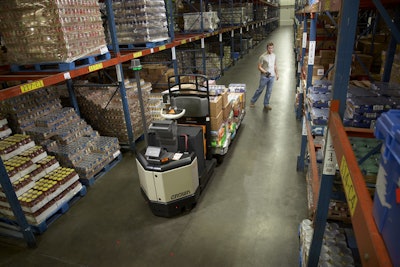
When it comes to lift trucks and safety, it’s all about the operator.
The statistics alone will tell you the story. There are an estimated 6 million lift trucks/forklifts currently in use worldwide, about 856,000 in the U.S. alone, and according to the U.S. Occupational Safety and Health Administration (OSHA) there are 100,000 accidents reported every year resulting in 94,750 injuries and 85 fatalities. Overall, one in every six workplace fatalities are forklift related.
When you factor in the statistics from the National Safety Council that state that 70 percent of those 100,000 forklift and industrial accidents per year are operator-induced, it becomes clear quite quickly that safety begins and ends with the operator. When you see a very rough estimate of $135 million of immediate costs associated with forklift accidents, and that’s not even considering insurance, OSHA fines and loss of inventory, those kind of huge costs make operator safety crucial to every warehouse that relies so heavily on lift trucks for daily operations.
Since lift trucks are the lifeblood of material handling operations, with the timely flow of goods so important to profit margins, it’s easily understandable why keeping workers and operators happy and comfortable means keeping the facility safe. A recent study conducted for Toyota Industrial Equipment illustrates the fact that operator comfort is starting to drive forklift purchases. When asked what is the most important safety feature influencing their decision, almost as many purchasers said operator comfort (95 percent) as they did stability (96 percent) and weight distribution and balance (97 percent).
Big Data a useful safety tool
Perhaps the largest trend not only in the lift truck industry, but in the global f&b supply chain as a whole, has been the expansion of software and technology applications. Facility managers can be overwhelmed by the amount of information they can glean after just a few weeks of using some of the newer fleet management software applications offered today. But when they see the impact this “big data” has on safety, it often proves to be well worth the investment.
Fleet management software offers insights into operator data as basic as which operator is on which forklift, to advanced safety features like not allowing certain operators to use certain vehicles where they haven’t passed the required safety training. They also offer real-time and actionable fleet data on vehicle impacts and crashes, as well as lots of productivity and uptime data that can get as advanced as the customer desires.
“Managers now have real data gathered by the forklift, instead of relying on operator-reported impacts, and it’s providing a holistic picture of how the equipment is being used and where and what safety incidents are really taking place,” says Andy Smith, director of product management at Crown Equipment.
Masters Gallery Foods, a supplier of cheese products headquartered in Plymouth, Wis., made it a priority to improve lift truck safety when they increased from 12 to 19 trucks and 40,000 to 110,000 square feet of warehouse space during an expansion project started in 2012. Since Masters Gallery Foods already had a fleet of Raymond Corp. lift trucks, they chose to install Raymond’s iWarehouse fleet optimization software. Within the first month, the results in safety, productivity and maintenance made a significant difference inside their expanded main warehouse.
“In our first month of using the system, we experienced a total of 45 alerts (impact alerts),” says Dan Murphy, warehouse manager at Masters Gallery Foods. “We provided additional training for the operators involved, and five months later we reduced the number of alerts to five – a reduction of 88 percent. The system plays an integral role. It encourages proper lift truck operation, reduces damage, maintenance, downtime and costs.”
Clemens Food Group, a pork producer based in Hatfield, Pa., received similar results when they installed Crown’s fleet software system called InfoLink, with an 80 percent reduction in impacts across three of their facilities totaling over 1.3 million square feet. With about 230 forklifts from many different manufacturers and 1,080 operators, Clemens originally installed the system to mine for hidden cost-cutting opportunities. Within five months the system uncovered significant improvements in regards to OSHA compliance, operator certification management, impact detection and operator performance. The system has “completely elevated and enhanced the safety culture of our facilities,” according to Kevin Shayer, the general manager of distribution and warehousing at Clemens in a case study provided by Crown.
Have a seat and get comfy
Since keeping the operator comfortable for an entire 8- or 10-hour work shift has become more of the focus in safety, it’s become more of a focus in lift truck design and innovation. Simple ergonomic designs like added suspension in floorboards, adjustable and contoured armrests, kneepads and backrests, lower operator steps and adjustable user controls have long been added to lift truck designs to increase productivity and safety. These features reduce fatigue and the amount of repetitive motions. But more and more manufacturers have noticed a growing interest in one of the most basic and simple functions on a lift truck … the seat.
Since a majority of loads in a warehouse are carried while the lift truck is in reverse for optimal visibility, seats that can swivel, or that can be adjusted to multiple angles for different size operators have become standard. This has been done to accommodate for drivers who spend multiple hours in a day in twisted positions.
Mitsubishi Caterpillar Forklift America (MCFA) recently launched a new series of Jungheinrich moving mast trucks to meet the demand for lift trucks with seats, as their new ETV 110/112 Series is one of the few sit-down moving mast trucks that have been popular in Europe but that are just starting to gain popularity in North America.
“The overall industry trend are loads are getting heavier, yet they want to maintain their skinny aisles, so they have to lift the bigger loads higher too,” says Steve Rogers, senior product marketing consultant at MCFA. “The moving mast reach truck works differently, but when operators demo the truck, they think it’s phenomenal that they no longer have to stand in the truck for eight hours a day.”
Most new lift trucks also feature all of the ergonomic comforts of new automobiles, including automotive-style driving pedals, hydraulic control levers and either power or hydrostatic steering to make the overall operation as smooth as possible to increase operator comfort. The power steering has become so advanced in many of today’s newest lift trucks that “they’re getting so easy to drive it’s like driving your car for an entire shift,” according to Rogers.
Unicarriers Americas has also seen an increase in interest in sit-down and center-rider lift truck models, especially since those models are designed to be more accommodating and customizable to fit unique operator sizes.
“We’ve had a greater interest in our center riders because of the smoother ride and the increased suspension in the floorboard,” says Mark Porwit, director of marketing and product management at Unicarriers Americas. “The step off height is the same on center riders. We’re continuing to see more female pickers in our customer’s operations, which means not only customizable features due to physical size differences, but smoother manual features that reduce the effort required to operate the forklift.”
How do you take the idea of operator fatigue one step further? Don’t even make them get up and down and in and out of a seat at all.
“We’ve talked with our food and beverage customers, and the walking isn’t just what fatigues operators, but the continuous stepping off and on the truck,” says Smith.
So Crown introduced their QuickPick Remote wireless remote system that is worn by operators and allows operators to advance the truck with the push of a button to reduce the need to step onto the truck to advance it to the next pick location.
Technology evolves for visibility
Aside from the idea of keep operators safe by letting them sit down or stand more comfortably, many of today’s technological advances in lift trucks are driven by the working environment in narrow aisle warehouses that are adding racking upwards to economize space.
“Food and beverage are looking for a safe way to pick from second levels because they are trying to put more SKU numbers in smaller spaces, so they are going up versus out with their products,” says Smith.
This smaller-and-narrower trend plays right into the sweet spot for Landoll Corp., makers of the Bendi and Drexel Narrow Aisle Forklifts headquartered in Kansas. Landoll will be showcasing a brand new High Lift model at this year’s ProMat 2015 that works in an aisle as narrow as 78 inches and can lift as high as 480 inches (40 feet).
To handle these smaller spaces not only are the truck designs slim and compact for narrow aisles, but now the support arms and the mast are getting smaller for better visibility. Most manufacturers have improved the visibility either by narrower design, by offsetting the mast away from the center of the operator, or even using design features like Crown’s MonoLift Mast. This mast actually gets narrower the higher it goes up.
Yale Materials Handling Corp. took its Hi Vis Mast design on new lift truck models one step further for safety by offering mast cylinder safety fuses to “prevent a raised mast from free-falling down in the event of a hoist hose rupture,” according to Jay Costello, director of training at Yale.
As a result of warehouse racking going up and not out, one of the newest featured designs on lift trucks is increased maximum lift heights and higher capacities. The latest models to leave the manufacturer are equipped to reach heights of 23.5 feet and higher. And heavy loads at elevated heights can bring obvious safety issues, which is why the use of sensor technology to safely navigate at the upper levels of the racking is starting to become less of a customized feature and more of a necessary safety requirement for operators and facility managers alike (see sidebar on sensor technology).
“When you get up high operators can quickly lose perspective of where the forks are at, so it’s difficult to stop them at the right (rack) position,” says Ed Campbell, sales manager at Landoll Corp. “Our new High Lift model will be equipped with a shelf-level selector that uses a camera and a shelf sensor, so the operator can just program in what level they want the forks to go to and they automatically stop at the right position.”
With more lift trucks in tighter areas, the market for presence warning devices like blue lights, self-adjusting back up alarms, and flashing and strobe lights have almost become must-have add-ons on any truck in the fleet.
“Instead of 10 beeping horns in a facility, you install a blue light on the overhead guard and it shoots out a stream of laser-like, blue light that alerts workers on the floor and on mezzanines to the presence of a forklift,” says Jim Chesla, vice president of business products at Starke ForkLift. “That’s one of the biggest after-market safety products in the forklift industry today.”
Sensor Technology Offers Integrated Stability Control To Eliminate Tip Overs
The Industrial Truck Association (ITA) estimates that there are nearly 856,000 forklifts currently in operation in the U.S., with other industry associations estimating a worldwide total of over 6 million. The U.S. Occupational Safety and Health Administration (OSHA) records about 100,000 lift truck accidents per year, with a surprising total of 85 fatalities annually. Out of those 85 deaths, 42 percent occur when the driver of the forklift tries to jump off a tipping vehicle in a crash.
So it’s a simple proposition … eliminating lift truck and forklift tip-overs in the warehouse is a major focus for manufacturers and warehouse managers.
Not only can mistakes on a lift truck be deadly, they are costly as well. The damage to inventory when a tip-over occurs often results in the cost to replace the lost inventory exceeding the salvage value of the damaged goods. In the case of food and beverage producers and wholesalers where single percentage profit margins are common, it can have devastating effects.
One of the ways used to reduce tip-overs in lift trucks and forklifts is through the use of sensor technology integrated into several critical points on a vehicle. The use of sensors allow constant monitoring of a forklift’s operation, such as speed, turns and forward and reverse travel. This will detect conditions that might lead to instability and an increased risk for a tip-over.
The data is collected on an on-vehicle unit and analysis is done in real time in order to automatically activate a corresponding correction to assist the operator in regaining control. The resulting actions can range from restricting the tilt angle of the mast, limiting the top speed when loaded or preventing the lifting of the fork height at certain speeds altogether. While some of these systems aren’t necessarily new technologies, the progression in sensor technology is making rapid improvement in providing integrated stability control performance more smooth.
These systems are typically offered as an add-on option on newer vehicles by the lift truck OEM or dealer. They are starting to gain in popularity, according to SICK AG, a sensor intelligence company headquartered in Germany. Here’s a look at the most popular stability control applications on a forklift according to SICK:
Fork Height: Sensors are used to set maximum height thresholds for load pickup or placement at elevated heights, such as on today’s racking systems that are going higher as space in the warehouse gets smaller and restricted. These systems not only prevent tip-overs by restricting the height loads, but the sensors also reduce the risk of damage to pallets when picking because of the inherent accuracy of the pre-determined fork height. A sensor attached to the highest pallet spot on a rack is reflected back to the sensor mounted on the mast. Through laser triangulation, it stops the fork height literally within one millimeter of the maximum height allowed for safe handling.
Travel Speed: Tip-overs often happen when the lift truck is traveling too fast with a load and turning sharply, or if the load is at an improper height or tilt. Using a closed-loop feedback sensing system, the sensor determines if the vehicle’s speed exceeds a safe threshold and automatically imposes acceleration limits to prevent a tip-over.
Steering Angle: Using a similar closed-loop incremental encoder and sensor system like with speed control, safe steering angles can be verified based on the number of turns of the steering wheel. A sensor near the steering shaft can relay unsafe steering angles instantly to the control system and restrict the operator’s ability to steer the forklift into “unsafe” situations.
Mast Tilt Angle: Sensors can determine if the mast is tilted past a safe range for optimum load stability in two ways. This is done either by determining the distance a mast travels away from a set point (or sensor) or an inductive sensor which actually detects the proximity of metal objects without touching them. The inductive sensor detects when the metal mast is within range when its electromagnetic field has been interrupted. Should the mast pass outside of the detection range, the information is relayed to the forklift’s control system in order to trigger the corresponding stabilizing action.
Load Presence: Two types of sensors mounted near the base of the forks or on the mast can help detect loads when they are out of view. Using a photoelectric sensor, the absence or presence of a load is detected when a beam of light is reflected off the load (or pallet) back to the receiver. An ultrasonic sensor generates a high frequency sound wave off the load and back to the sensor, alerting the driver it can safely be loaded onto the forks.
Load Weight: By measuring the amount of hydraulic pressure exerted by a load on the vehicle’s forks, pressure sensors can offer a primary or secondary verification of the weight of the load by an on-board forklift scale. The data is transmitted by the sensor to the control system, which can automatically trigger stabilizing actions needed for heavier loads.
Location Sensors: Forklift tip-overs also often occur when a vehicle comes in contact with overhead obstacles, beams, fire-protection sprinkler heads or even doorways. To restrict access, or trigger speed or mast height limitations in certain areas of the facility, RFID tags are placed on walls, floors structural uprights and other areas of the warehouse so that when a sensor on the forklift detects a tag, it can implement the appropriate stability measures.
Source: Reduce Accidents on Manned Forklifts with Integrated Stability Control, SICK AG, 800-325-7425 or www.sick.com.
Can Hydrogen Fuel Cells Be Called A “Safer” Alternative?
One of the recent trends in lift trucks and material handling in general is the emergence of the hydrogen fuel cell (HFC). In the case of lift trucks, HFCs are being touted as a safer alternative for power in a lift truck or forklift than the current widespread use of lead-acid batteries.
But that brings up an interesting question … is the adaption of hydrogen fuels cells in lift trucks a safety feature? Will the safety of the entire fleet of lift trucks improve with a conversion to hydrogen fuel cell technology?
The answer depends on who you talk too, with the outlook toward fuel cell technology in general ranging from highly skeptical to positive, with a healthy dose of wait and see.
“We’re not seeing much interest (in HFCs) from our customers; it’s sort of stalled in my point of view,” says Jim Chesla, vice president of business products at Starke ForkLift based in Canada.
“In a lot of lift trucks, the battery is used for stability and balance, so replacing that with a single HFC, it causes stability and balance issues,” says Steve Rogers, senior product marketing consultant at Mitsubishi Caterpillar Forklift America (MCFA). “To make up for that weight requires a lot of redesign and it becomes a very specialized lift truck.”
Since the only byproduct of a hydrogen fuel cell is heat and water, proponents of the fuel cell movement like Plug Power, the Latham, N.Y.-based producer of hydrogen fuel cell technologies, have always touted the environmental benefits of the fuel cell over the lead-acid battery. But since you can’t just drop a fuel cell into any old lift truck, lift truck manufacturers have yet to fully embrace fuel cell technology.
But that changed in December of 2014 when NACCO Materials Handling Group (NMHG), the parent company of Hyster Co. and Yale Materials Handling Corp., upped the ante on the hydrogen fuel cell trend by announcing they acquired Nuvera Fuel Cells, Inc.
The addition of Nuvera makes NMHG the first lift truck OEM to offer on-site hydrogen generation and refueling capabilities, addressing the type of hydrogen “infrastructure” issues that crop up time and time again as the main stumbling block to full-scale fuel cell technology adaption by lift truck manufacturers and warehouse owners.
“With fuel cells, there are still a number of ROI considerations that have yet to be fully resolved with the technology,” says Andy Smith, director of marketing product management at Crown Equipment. “The complexity of the technology, reliability issues in performance, the total cost of ownership and the absence of refueling infrastructure continue to limit widespread adaption.”
For the record, NMHG is realistic that their acquisition and entry into the HFC sector will reap profits and market share. Plug Power is still struggling to profitable, and leaders at NMHG acknowledge the addition of Nuvera will cause “significant operating losses” while it works to commercialize the HFC technology to achieve a break-even bottom line.
Then there’s this finishing note, courtesy of Mark Porwit, director of marketing and product management at Unicarriers Americas ... what about the next best technological trend for lift trucks? “It’s not out of the question that HFCs could be leapfrogged by anther technology altogether,” speculates Porwit.
For More Information:
Crown Equipment Corp., 419-629-2311, www.crown.com
Landoll Corp., (800) 428-5655, www.landoll.com/mhp
Mitsubishi Caterpillar Forklift America (MCFA), 713-365-1000, www.mcfa.com
Plug Power Inc., 518-782-7700, www.plugpower.com
Raymond Corp., 800-235-7200, www.raymondcorp.com
Sick AG, 800-325-7425, www.sick.com
Starke Material Handling Group, 877-435-4352, www.starkecanada.com
Toyota Industrial Equipment, 800-2260009, www.toyotaforklift.com
Unicarriers Americas Corp., 800-971-5438, www.unicarriersamericas.com
Yale Materials Handling Corp./NACCO Materials Handling Group (NMHG), 440-449-9600, www.yale.com