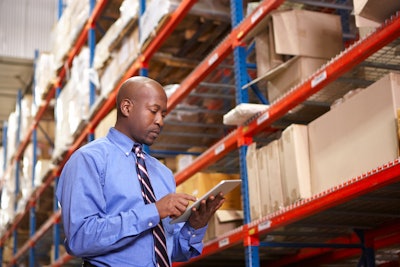
“Enterprise mobile management” and “mobile device management” are terms that describe the way businesses are now using smartphones, tablets and PCs to manage their operations. The tools give both managers and employees real-time feedback and direction. They work on a range of operating systems and they can improve performance in nearly every type of work environment.
While these mobile networks are largely in their infancy, the food and beverage (f&b) supply chain is finding they facilitate many important functions. Growers, processors, wholesalers, distributors, retailers, carriers and 3PLs are all finding mobile management makes them more productive
Smartphones and tablets are already enabling many tasks, including acting as remote controls, displaying and analyzing information, and interfacing to networks to monitor activities.
“Mobile apps are really starting to become the desired input for data,” says Joe Scioscia, vice president of sales at VAI, the Ronkonkoma, N.Y-based ERP software provider. “They’re very application focused. Mobile apps are very singular-focused and user friendly.”
As people of all ages become used to mobile apps, the Internet cloud enhances their versatility.
Cloud-based systems allow companies to access data quickly and easily compared to on-site, browser-based software.
Worker empowerment
One of the most revolutionary aspects of mobile management is its level of worker empowerment. It is a form of automation that can enhance rather than compromise personalization in the work place.
Church Brothers Produce Inc., a grower, processor and retailer based in Salinas, Calif., has found cloud-based mobile enterprise systems deliver a number of benefits, says Drew McDonald, vice president of the company’s quality, food safety and regulatory affairs.
Denver, Colo.-based Go Spot Check allows Church Brothers Produce workers to complete quality reports and take pictures in the field via Android and Apple smart phones and tablets. The software ensures the field team organizes the data according to Church Brothers Produce’s own parameters. Management creates its own checklist for various field tasks.
Church Brothers Produce uses another cloud-based software for compiling real-time reports for food safety monitoring. This software from Seattle, Wash.-based iFoodDecisionSciences comes programmed to check for certain types of data.
McDonald gives high marks to both Go Spot Check and iFoodDecisionSciences for taking into account the way a grower operates. Both software systems streamline the processes for documentation, filing and exporting data to other programs. “They’re very appropriate for what we’re trying to do,” he says.
iFoodDecisionSciences launched two years ago to help growers, packers and processors collect and analyze food safety data, according to CEO Diane Wetherington. Growers in particular are faced with an increasing demand for food safety data and collection.
In the two years since the company formed, two fortuitous technology developments have converged, Wetherington says.
One: mobile devices have become widely used. Two: cloud computing has provided an efficient and affordable way for companies to store and access data in real time.
Workers can now log data from the field, factory or warehouse. Because of real-time alerts about hazards, such as unsafe chlorine or pH levels in a water tank, “you don’t have to wait for somebody to find the appropriate supervisor to take action,” Wetherington says.
FSMA drives innovation
Wetherington says that these tools will help companies comply with the Food Safety Modernization Act (FSMA). While the FSMA rules have not yet taken effect, Wetherington’s customers are already using her company’s apps to verify compliance with Good Agriculture Practices (GAP) and Hazard Analysis Critical Control Point (HACCP) standards.
Mobile solutions are also playing a big role in f&b transportation.
Karlsburger Foods Inc. in Monticello, Minn. has found mobile apps for field sales and proof of delivery signature easier, faster and less expensive – as well as much more accurate, allowing better customer service. The company’s foodservice division upgraded this year from laptops to Vormittag Associates, Inc.’s S2K browser-based, enterprise system. Karlsburger Foods provides its drivers iPads.
Mike Maher, CEO at Karlsburger Foods, says the company’s route sales drivers were having connectivity issues with the laptops they were previously using. The mobile solution that has replaced the laptops allows sales reps to access customer sales information in real time and provide electronic receipts. The reps still carry Blue Tooth printers for those customers that want paper receipts. About half are still getting paper receipts.
The connectivity issues with the laptops were especially problematic. If a laptop could not connect to the Internet, the sales could be assigned to the wrong month, which created administrative problems. “Our reps were always having issues with the connectivity. That was always an issue for us not be ‘live,’” Maher says. It wasn’t unusual for a rep to spend 20 to 30 minutes to connect to the virtual private network.
“I want our sales people to focus on selling our product,” Maher says.
Deploying the mobile software to Karlsburger Foods’ 37 cube van drivers was easy since it only takes 30 seconds to download the app. If a driver loses an iPad, all he needs to do is get another one at Best Buy. “All the information is stored in the cloud. That’s a huge advantage for us,” says Maher.
The laptops they previously used cost between $1,000 to $1,200 and required software installation, making the total cost $1,400 to $1,800. The mobile system is about half the cost. “This system is a lot simpler and a lot less expensive,” Maher says.
In addition to making deliveries more efficient, the mobile solution makes the company “greener” and improves customer perception. “We’re on the leading edge with technology,” Maher says.
Deliveries improve
Monsanto Co., a provider of agricultural products for farmers, found a mobile enterprise solution improved its deliveries. The mobile solution from Atlanta, Ga.-based nuVizz Inc. allows drivers to complete orders faster and more accurately. It also allows the company to track deliveries and capture customer feedback from the field in real time.
Each contracted carrier has their own Monsanto portal from which they assign deliveries. Once the driver downloads the app, they can receive orders in real time. If they travel to an area without connectivity, they will still be able to execute the delivery since the app has offline capability built in. The nuVizz software integrates with Monsanto’s SAP ERP system, allowing real-time visibility of deliveries. It also allows the drivers provide electronic proof of delivery to customers.
A new LTL freight marketplace
Mobile apps have allowed a new group of freight websites to revolutionize the LTL carrier marketplace. Freight websites such as Austin, Texas-based uShip and San Francisco, Calif.-based Trucker Path allow shippers to post loads in real time and let truckers bid for them.
The carriers don’t have to pay subscription fees, which can be around $100 per month if they are accessing several boards.
“They only pay when they have a match,” says Dean Jutilla, vice president of marketing at uShip. “You don’t have to make any phone calls.”
Shippers periodically check the spot rates on uShip and compare them to their existing carrier’s contract rates, Jutilla says. “We think buying your freight services should be like buying your airline tickets.”
He says drivers find the app very convenient. “When you’re on the road, the app’s the thing,” he says.
uShip aggregates competing rates from 70 to 80 percent of the LTL market, including FedEx Freight, Old Dominion, Con-way Freight, YRC, and over 50 other carriers, Jutilla says. The result is better spot market rates, service level and delivery timeframe.
uShip initially offered a mobile web app, but found that native apps provide more location finding, sharing, tracking, and search and payment capabilities. Hence, the uShip app is available on Android and iOS platforms.
In October of 2013, Ivan Tsybaev started Trucker Path, a mobile app that truck drivers could download and have access to road information, such as the availability of weigh stations, the condition of truck stops, parking availability, washing facilities, etc. The app works on Android and iOS operating systems.
Truckers, being a closed knit community, spread the word, and in less than two years more than 400,000 of them downloaded the Trucker Path app.
Once this critical mass was reached, Tsybaev got the idea of inviting freight brokers to post carrier loads and let the truckers bid for them. The drivers place bids and the brokers accept them. Trucker Path gets a percentage of the sale. The drivers have to be licensed with the carrier.
More than 300 freight brokers have placed 30,000 truckloads. He has been testing it since March 2014 in Texas and California. He plans to release it nationwide in June.
Tsybaev estimates that more than half of his freight is f&b.
Like Wetherington at iFoodDecisionSciences, Tsybaev thinks his timing has been fortuitous. Four years ago, less than 30 percent of the truckers used mobile apps. Today, it’s about 80 percent.
Managing the DC in real time
Mobile management is also making big inroads inside the DCs.
Manhattan Associates recently surveyed DCs on mobile solutions and found that 81 percent plan to deploy such solutions for managers. The top benefit expected is increased engagement, 60 percent, followed by increased oversight, 42 percent; real-time data, 33 percent; supervisor productivity, 21 percent; and exception management, 19 percent.
The survey found that historically, managers spent more time managing exceptions (62 percent) and monitoring work (57 percent) than interacting with employees (41 percent). Lack of access to a computer was the top reason (62 percent) keeping managers off the warehouse floor.
In introducing its mobile distribution management solution, Manhattan Associates has adopted the mantra, “Ditch the Desk” to signify the importance of allowing managers to spend one-on-one time with warehouse employees.
While LMS and WMS solutions have long been integrated, sharing performance data in person with employees has been relegated to static reports run at long intervals. Mobile management, however, improves the manager/employee interaction by connecting both parties to performance reports in real time.
Managers can update information while an operational change is being made, and potentially reverse changes quickly to avoid work stoppages. Examples of active capabilities include task reprioritization, release and reassignment. Outbound tasks in particular have the potential to benefit the most due to their high complexity and rapid pace.
Dallas, Texas-based RMG Networks, one of Manhattan Associates’ software partners, recently made its InView Mobile solution available on iOS and Android phones and tablets. RMG’s labor productivity improvement tool provides real-time, highly visible metrics and data that enable employees to see how they are performing against goals. By receiving this information in real time, employees they can adjust their behavior and maximize their productivity.
Supervisors can send real-time metrics (e.g., picking and packing rates by team or individual members; rankings; actual versus goal performance) via display screens and desktop dashboards to employees on the manufacturing or warehouse floor. This enables them to better make decisions in real time. The data also can be pushed to mobile devices, enabling management to monitor activity from any location or through pre-set, threshold alert notifications.
The RMG software can pull data from a customer’s LMS, WMS and TMS system, says Steve Chang, senior vice president of strategy and solutions.
Yard management improves
Columbian Logistics Network, the Grand Rapids, Mich.-based 3PL, has found mobile technology helps integrate yard performance into overall supply chain metrics.
Yard management that utilizes mobile communication benefits from lower hardware costs and oftentimes, faster training. Nowadays, many if not most employees are familiar with how to use smart phones and tablets.
When requesting a trailer to be moved from one yard location to another, a mobile device can receive real time request and identification information, says Blair Thomas, director of customer care at Columbian Logistics Network. The mobile device using the YardView software can capture the metrics as the task is being executed.
In the case of a certain bread manufacturer, the mobile connectivity improved communication among buildings that send and receive trailer shipments.
The trailers do not follow a static delivery pattern. Columbian Logistics Network configured YardView, the yard management system from Castle Rock, Colo.-based Cypress Inland Corp., to send an email to a defined distribution list in the receiving warehouse saying, “Hey, a trailer is coming your way, and it’s headed to the yard.” At that point, the person(s) in warehouse can change that move to another location. When the trailer arrives at the warehouse, the driver sees a big red flashing screen that indicates a change has been made. The driver checks the alert message, sees that the destination has been changed, and completes the move accordingly.
All facilities in this customer’s campus are now using commonly available iPods to get the emails in case they are away from the desk when the notification arrives. The iPods are wifi connected in the buildings, so there is no ongoing cost.
“It’s all about having connectivity to the device, and the program is hardware agnostic,” Thomas says.
Mobile technology brings Internet connectivity to every task in every stop of the f&b supply chain. The real time connection empowers both managers and employers.
Mobile apps: native, web-based and hybrid
When introducing mobile apps, companies face the choice of using a web-based app or what is called a “native” app. The web-based app is device neutral, while the native app has functionality built into its operating system.
A mobile web app works across all mobile platforms and operating systems. They don’t need a different mobile web app for iOS, Android, Blackberry, and Windows devices. Even if another operating system becomes popular in the next few years, that same mobile web app will work on that platform as well.
Sal Stangarone, product consultant at MRC, the Oak Brook, Ill.-based provider of web application software, says both app types can allow a worker to access and record data while disconnected from the Internet.
“Mobile apps will do everything most businesses need,” Stangarone says.
While both app types can access all functions, a native app will provide more seamless integration for accessing a camera or a microphone than a web app, he says.
In addition to mobile and native apps, there are also “hybrid” apps. The hybrid is a mobile web app wrapped in a platform-specific shell. This shell provides native qualities, such as full device integration, native installation, and app store/market distribution.
For more information:
Columbian Logistics Network, 888-609-8542, columbianlogistics.com
Cypress Inland Corp., 303-781-3430, yardview.com
Go Spot Check, 844-359-2502, gospotcheck.com
iFoodDecisionSciences, 206-384-4679, idsfoodsafety.com
Manhattan Associates, 770-955-7070, manh.com
MRC, 630-916-0662, mrc-productivity.com
nuVizz Inc., 404-937-1971, nuvizz.com
RMG Networks, 800-827-9666, rmmgnetworks.com
Trucker Path, truckerpath.com
uShip, 800-698-7447, uship.com
VAI, 800-824-7776, vai.net