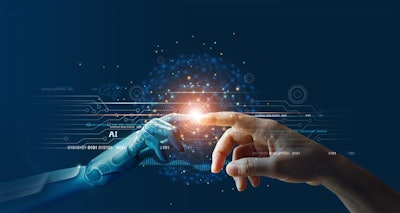
Before the Coronavirus disease (COVID-19) pandemic, U.S. food supply chains were assumed to be well-oiled machines. As everyone undoubtedly noticed, the pandemic has revealed a need for repairs.
Take, for instance, what happened with Smithfield Foods. When COVID-19 spread through its South Dakota plant, the largest pork supplier in the Unite States was effectively shut down — causing major concern over meat shortages. On the other hand, the demand for foods fell in certain places as hotels, restaurants and schools closed their doors. At the same time, the demand for groceries skyrocketed. The U.S. food supply chain was not equipped to handle this kind of disruption, and food suppliers had nowhere to send their goods. A number of farmers even had to dump their milk supplies.
But, is the pandemic entirely to blame for these supply chain issues? No, the lean food supply setup — driven by economists and financial analysts — was designed to balance supply and demand carefully to make businesses more profitable. This reliance on Keynesian economic models rather than statistical process control models has brought the food industry to its knees as it struggles to adapt to changing market conditions.
It’s COVID-19 today, but it could be something else entirely tomorrow. Food supply chains were bound to fail, and they will fail again unless we rethink the process.
Supply chain changes during abnormal times
During “normal” times, food supply chains are optimized with cost and price considerations at every node. This often requires siloed teams to create “local optimals” — negotiating the best prices for bulk deals, maximizing economies of scale, and relying on demand forecasting to set boundaries for expected sales targets. This method reduces costs for suppliers, who can then pass those savings along to consumers.
When business is good, organizations focus on maximizing sales and minimizing costs. Pragmatic organizations, however, use the good times to optimize for the fastest throughput (speed) of material flow from the end-to-end supply chains. This sort of prioritization is not common, though, due to accounting systems and the inability to move inventory from asset to liability as the economy changes. This is further exacerbated by the “duality of inventory,” when a good is both a liability and an asset at the same time at certain points in the supply chain.
Now, as sales have plummeted, businesses can only reduce costs so much. Some have relied on loans, but those are not viable or sustainable solutions. One of the only remaining factors a business can control is throughput. After all, reducing the amount of time that inventory is on hand minimizes any risk to cash positions.
Steps for optimizing supply chains now and in the future
Companies that can adapt their processes to overcome changing market conditions will be best positioned to thrive once business returns to “normal.” Consider the following steps as you rework and upgrade your food supply chains:
1. Identify your largest constraints quickly. Starting with the greatest “output-limiting” point is the most time-critical step. Focus on bottlenecks while developing a strategy that focuses on removing any restrictions that might prevent you from quickly adjusting.
2. Shorten your supply chain. A supply chain is like a garden hose: The longer it is, the more time it takes for the water (or product) to come out, the more likely it is to get tangled and impact flow. If you pinch one end of the garden hose, water flows faster. Likewise, you might introduce a pinch to your supply chain to speed things up.
3. Isolate cost-cutters in your organization. It’s common to consider cost-cutting measures like layoffs in times of disruption, but businesses that rely on these measures lack imagination and management. It is far better to devote time and resources to a workforce dedicated to optimizing product delivery times and levels of output at margin.
4. Eliminate excess capacity. If you don’t have enough orders to maintain full capacity, eliminate the excess. Sell floor space or machine time to other businesses to obtain new revenue streams from idle resources.
5. Be demand-driven. Forecast-driven operations are subject to inaccuracies that force businesses to react rather than act. Instead, focus your business strategy on current consumer spending habits. By switching to demand-driven operations, you can become more profitable — switching to demand-driven operations can reduce inventory by more than 30% and increase supply chain performance by up to 20%.
6. Secure cash. In good and bad times, it’s prudent to protect liquid assets with cash buffers. Even if your operations are under control, that doesn’t mean the same is true for your customers or suppliers.
7. Rethink your supply and delivery strategies. Now is the perfect time to re-plan third-party logistics and distribution arrangements. Suppliers should be as close to consumption points as possible to optimize lead times.
There are ample resources to make food prices near-zero — absent of economic models and constrained markets. The world has never had a food shortage; it has a distribution problem. Food supply chains are man-made, and artificial bottlenecks in our supply chain mean that price will remain king while good food goes to waste.
By designing for flow optimization instead of profit maximization, more of the world could eat — and businesses could better accommodate disruptions. There is no better time to rework food supply chains than while vulnerabilities are revealed, and COVID-19 has given us that opportunity. We just need to seize the moment.