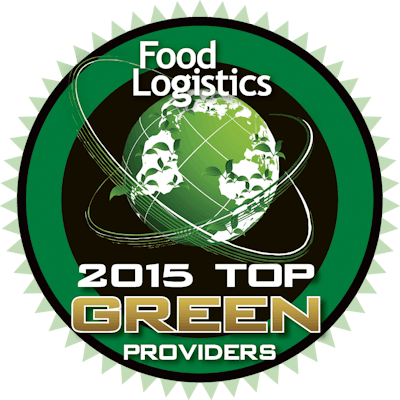
This year’s Top Green Providers represent transportation providers, 3PLs, cold storage providers, technology companies, pallet manufacturers and others key to supporting a more sustainable global food supply chain.
To see the entire list of 2015 providers, please go to: http://www.foodlogistics.com/document/12084692/2015-top-green-providers-full-list.
Following are expanded profiles of some of these companies on the 2015 list…
CaseStack (www.casestack.com)
Casestack’s consolidation protects suppliers’ resources by providing proportional, full truckload pricing instead of costly LTL rates, boosting on-time performance, maximizing in-stock rates, limiting the potential for damages/shortages and lowering total logistics costs. Collaborative consolidation programs help retailers conserve financial resources by eliminating supplier minimums, reducing supplier lead times to their DCs, increasing supplier on-time deliveries, optimizing in-stock levels, and rightsizing inventory levels. Consolidation programs help conserve natural resources by reducing dock congestion, improving warehouse efficiencies and decreasing the number of trucks on the highway. The resulting supply chain consumes less energy and produces lower amounts of carbon emissions. Fewer trucks on the road also results in fewer interactions with motorists. From energy efficient warehouse upgrades to the Retailer Consolidation Program, CaseStack’s solutions are based on a common sense model; reduce waste and maximize efficiency by streamlining processes and consolidating resources.
CHEP (www.chep.com)
As the leader in pallet and container pooling solutions, CHEP has a history of reducing environmental impacts across the supply chain. CHEP is able to leverage its expertise to extend the life of the assets in its pool, which minimizes the resources needed to maintain and grow the pool. Controlled ownership and accountability are key components of the CHEP program, which facilitates appropriate end-of-life management, maximizes material reuse and diverts residual material from landfills. CHEP also offers its food and beverage customers environmental benefits via transportation efficiency in the supply chain. The CHEP network enables more efficient transport distances between CHEP and customer locations, including both distribution and retail locations. These shorter distances save fuel, reduce transportation costs and reduce CO2 emissions throughout the supply chain. CHEP USA has been using Life Cycle Assessment (LCA) methodology to quantify and reduce the environmental footprint of its products and services since 1999.
C.R. England (www.crengland.com)
C.R. England continually looks for ways to reduce its carbon footprint in equipment enhancements. The company also works actively with customers to identify improvement areas, including adjusting appointment windows that avoid down time for drivers and excessive idling of trucks. Customers will oftentimes have drop and hook loads where C.R. England drops off one trailer and picks up another loaded trailer to further eliminate down time. In addition, the company has a designated person that reviews untethered trailer tracking loads to watch for empty trailers with the reefer running. C.R. England has invested in automatic transmissions for new tractors that come equipped with adaptive cruise, predictive cruise, and E-coast, all of which help in fuel efficiency. Initial tests have resulted in a 5 percent fuel improvement. Three quarters of the company fleet is SmartWay Tractor-approved. C.R. England also utilizes dedicated services to optimize its network with customers to create efficiencies.
DSC Logistics (www.dsclogistics.com)
DSC’s overall goal is to eliminate waste and cost in the supply chain for all of its customers. Sustainability has become a core element of the supply chain strategy: “We adopt practices that promote the responsible use of resources throughout our company and we align our efforts with your sustainability initiatives.” To achieve this at the corporate level, DSC’s Sustainability Steering Committee oversees and implements initiatives encompassing multiple aspects of overall carbon footprint reduction, energy reduction and recycling. At the local level, there is Green Team representation at all DSC logistics centers. These team members regularly review goals and company-wide sustainability communications. They also implement sustainability opportunities within the logistics centers. DSC has been tracking sustainability on five metrics (electricity, natural gas, water, propane, and recycling) across 40-plus locations for four years. Yearly goals include: further waste stream reductions; LEAN initiatives to reduce process steps and waste in the supply chain; and supply chain modeling to reduce logistics center footprints.
FST Logistics (www.fstlogistics.com)
FST Logistics employs both external and internal measurements in seeking to reduce its carbon footprint and promote sustainability. External measurements include contract commitments with customers to make measureable strides each year. FST submits the man-hours its employees contribute to green activities such as recycling, Earth Day or volunteer work in this area. The company also tracks the tonnage of cardboard it recycles and the amount of alternative fuel it uses. Internal measurements include savings on fuel usage, new lighting systems, and recycling truck oil to heat the shop. FST Logistics recently built an on-site, compressed natural gas (CNG) fueling station in partnership with US Oil in early fall of 2014. In conjunction with this, the company converted some day cabs to hybrid CNG/diesel. The station is open to the public to support CNG development.
Henningsen Cold Storage (www.henningsen.com)
Henningsen Cold Storage is one of the largest public refrigerated warehousing companies in the U.S., delivering award-winning refrigerated logistics through a national warehouse network totaling more than 53 million cubic feet of multi-temperature controlled storage (-20 to +60). The company offers a range of services, including freezer, cooler and dry storage, blast freezing, transportation management services, cross-docking, transloading, import/export services and distribution. Furthermore, Henningsen Cold Storage is committed to energy efficiency on many fronts. Two of the company’s locations have roof top solar panels and all warehouses use variable drive compressors to run the refrigeration systems. The engineering team manages these systems in real time and adjusts depending on need. Most of Henningsen’s warehouse locations have switched to energy-saving LED lighting to help conserve resources.
iGPS (www.igps.net)
The iGPS Logistics lighter pallet is approximately 20 pounds lighter than wooden pallets. This means less fuel consumption, a reduced carbon footprint, and the ability to transport more products per truckload. Using plastic pallets reduces the use of wood pallets, helping to conserve forests. In addition, because of the lower damage rates, substantially less natural resources are needed for repairs, transportation and handling. iGPS plastic pallets are cleaned as they pass through its depot network, which works well for customers using them in product-sensitive manufacturing areas. There are no protruding nails or broken boards that can injure employees or damage equipment and products. The pallets don’t absorb liquids, are impervious to infestation, are 100 percent recyclable, and are consistently uniform in size and dimension. Optimizing pallet selection leads to lower total costs throughout the supply chain. iGPS Logistics works closely with each of its clients to identify and provide effective solutions that eliminate, or significantly reduce, unnecessary costs in production and warehousing.
Johnson Refrigerated Truck Bodies (www.johnsontruckbodies.com)
JTB is committed to manufacturing the most thermally efficient, durable refrigerated truck bodies. Products are constructed of composite materials, and the company uses all-electric refrigeration systems with cold plate and cold plate blower systems rather than diesel-fueled systems. Johnson’s design and manufacturing team has proven its composite bodies are 175 times more resistant to heat penetration and 850 times more resistant than aluminum bodies. Testing also rates Johnson bodies as having the industry’s highest insulation value, and power grid plug-in refrigeration is proven to provide a clean operation.
Jungheinrich North America (www.jungheinrich-lift.com)
Jungheinrich set the industry standard for electric forklifts by developing the first 3-phase alternating current (AC) system. Today, Jungheinrich warehouse products continue to be recognized for cutting-edge technology, proven reliability and lower total cost of ownership. With advanced AC technology, Jungheinrich products are capable of running up to two shifts on one battery charge in most applications—resulting in a cleaner work environment. Grocery and food service distributor customers are able to measure the results in these efforts by counting the reduced number of battery changes per shift in addition to the number of batteries required for their operations. Jungheinrich’s AC-powered electric lift trucks also produce zero harmful emissions, providing another benefit for customers seeking to reduce their overall carbon footprint. Since Jungheinrich products have a longer run time off one battery charge, customers also benefit from an overall reduction in hydrogen gas emissions, which are emitted each time an electrical battery is charged—in addition to an increase in productivity for their operation.
Kenco (www.kencogroup.com)
Since 2013, Kenco has upgraded lighting at eight facilities in Chattanooga, Tenn., McBee, S.C., Memphis, Tenn., Dundee, Mich., Avenel, N.J., Allentown Pa., and Reading, Pa. with annual savings of over $250,000. The lighting systems have saved over 1,500,000 kilowatt hours annually and are anticipated to reduce greenhouse gas emission by over 1,000 tons annually. Currently, there are four more facility lighting upgrades in the planning stage. Kenco has also employed new sustainability dashboards. The dashboards bring together an array of data to conveniently display progress on key sustainability metrics. They also track usage of electricity, natural gas and water, plus they monitor labor costs and measure the output of both landfill waste and recyclable materials. Baseline data on each metric is monitored to set goals toward lowering costs, reducing energy use, and producing less waste in customer warehouses managed by Kenco.
nuVizz Inc. (www.nuvizz.com)
uVizz is a business solutions and services company providing complete mobile business SaaS solutions and Supply Chain consulting services. The company is headquartered in Atlanta, Ga., with offices in India and France. nuVizz boasts a strong portfolio of mobile apps and a comprehensive enterprise mobile toolkit, all supported by a team of core business process and mobile solutions experts. nuVizz solutions contribute to less paper and more efficient delivery of goods. One recent client in the food and beverage industry reported savings of 2.88 million sheets of paper over the past year alone. Furthermore, nuVizz accomplished reductions in materials purchased, improved its storage costs per usage, and achieved measureable savings in employee time.
OPEX Corporation (www.opex.com)
OPEX Corporation’s 2,077 megawatt solar array makes it a net-zero operation. As a result, every product the company manufactures at its campus in Moorestown, N.J. is made with 100 percent renewable energy derived from solar power. Additionally, its material handling automation, Perfect Pick, draws significantly less energy than competitive technologies. By eliminating complex front-end equipment-like lifts, conveyors or transfers from the design, ongoing operational expenses are reduced. Additionally, Perfect Pick’s wireless robots, iBOTs, are powered by onboard ultracapacitors, which are extremely energy efficient and charge “on the fly.” The solar installation is monitored via a Web-based dashboard, while the HVAC system is monitored by a commuter-based, programmable system that tracks and operates 100-plus rooftop units. Other sustainability efforts are monitored via utility bills, reports, etc. OPEX has implemented numerous environmentally focused improvements at its campus. These include lighting retrofits, roofing improvements, HVAC automation, and recycling initiatives.
Penske Logistics (www.penskelogistics.com)
Penske’s diversified portfolio of customers includes warehousing and distribution center operations for leading food, beverage and grocery customers in North America, Europe and Asia. Penske operates and manages eight refrigerated warehouse facilities in North America encompassing over 850,000 square feet of space. The company promotes the use of alternative fuel vehicles by providing CNG/LNG vehicle specification expertise to customers, providing training to maintenance technicians, and constructing and retrofitting maintenance facilities so they are equipped to service CNG/LNG vehicles. Through its partnership with the SmartWay Program, Penske has hosted educational events for customers via Webinars, one-on-one education, and strategy sessions. Penske actively recruits customers to join the SmartWay Program and assists them with data collection and submission of the SmartWay reporting tool for their transportation category (e.g., shipper, carrier, logistics). For the third straight year, Penske Truck Leasing has been honored by the U.S. Environmental Protection Agency (EPA) as a SmartWay Affiliate Challenge Award winner. Penske is one of seven organizations across the U.S. to be given the award at the Transportation Intermediaries Association (TIA) Capital Ideas and Exhibition Conference in Orlando, Fla.
Power Automation Systems (www.powerautomationsystems.com)
Power Automation Systems (PAS) enables its customers to go beyond the corporate responsibilities of growth—such as consistency, competitiveness, and profitability—by providing a way to also grow corporate responsibility for sustainability. It’s the environmental value that complements the economic value sought after by food and beverage companies. The warehouse automation solutions provided by PAS not only assist with economic value, but also do so in a way that helps the environment by reducing the carbon footprint of large warehouses. When efficient, precisely-sized and utilized electric servo motors replace oversized fuel guzzling fork trucks, and when lighting requirements are reduced by 80 percent due to the use of automation, the drain on planet resources is much less, making a sustainable balance more achievable. In addition, when efficient, precisely-sized and utilized electric servo motors make all the product moves in a warehouse, the energy required for those moves is recordable as kilowatt hours of electric power. This can be compared to the operational costs of fork trucks, which include fuel and maintenance costs.
Retrotech (www.retrotech.com)
Retrotech consolidated two functionally separate warehouse operations into a single warehouse control system (WCS), which enabled the entire facility to operate as a single DC. Doing so allowed the operation to run more efficiently. The company achieved 99.9 percent on-time arrival for shipments one month following the “go live” of the WCS. This predictability in arrival time allows customers to schedule their resources more accurately and receive orders on an expected time cycle. The company reduced loading time by automated stacking of pallets and increased trailer fill capacity. The increase in fill capacity allowed for a reduction of the number of trailers used for order fulfillment, which in turn lessened the overall fuel consumption and reduced the number of over-the-road miles driven to fulfill the same number of customer orders.
Reverse Solutions LLC (www.reversesolutions.com)
Reverse Solutions strives to add value to the level of service it provides its clients by incorporating the greenest approach possible to their processes. The company tracks all tonnages slated for recycling for clients and provides quarterly reports. Clients then receive rebates based on the amount of material sent to the mill for recycling. Reverse Solutions also implemented a repurposing program to add an additional option for recycling for clients. Any product that meets the qualifications for convertibility can be sent out and converted to cow feed at a fraction of the cost versus the standard landfill fee. The company has also reached out to local farmers and donates organics to be fed directly to cows or pigs.
Romark Logistics (www.romarklogistics.com)
New Jersey-based Romark Logistics prides itself as a leader in the establishment of warehousing “green initiatives.” The company considers “green” to be a core commitment that benefits its employees, customers and the communities it operates in. Romark Logistics has reduced its carbon footprint with 8,512 solar panels and achieved landfill-free status of 98.7 percent. Solar is measured with Draker utility grade meters and the landfill-free status is measured by various recycling vendors. In addition to these accomplishments, the company completed many energy efficiency reduction projects such as LED lighting, T5 warehouse lighting, motion sensors, refrigeration changes, office lighting retrofits to LED, office dimmer switches and water conservation devices.
Ryder System, Inc. (www.ryder.com)
Ryder helps food and beverage companies meet their sustainability objectives and “green” their fleets and supply chains by focusing on carbon reduction in three critical areas: network design, facilities and building use, and transportation. By designing a supply chain network with the reduction of the carbon footprint as one of its primary focuses, Ryder advises customers on factors such as the location of DCs, miles to be traveled, amount of inventory, and size and number of facilities included in the network. For the use of buildings and facilities, Ryder offers lighting efficiencies, cutting-edge energy technologies, alternative use of by-products, and other strategies to reduce waste and carbon emissions. In transportation, customers are not only able to take advantage of Ryder’s engineering expertise optimizing shipments, routes and modes, but can also tap into Ryder’s industry leading natural gas vehicle program. Ryder is also the market leader in natural gas vehicle and maintenance solutions for the commercial transportation industry.
The Raymond Corporation (www.raymondcorp.com)
As a means to help support the sustainability efforts of food and beverage customers, Raymond forklift trucks provide Eco-Performance—a design philosophy that Raymond incorporates into the design and engineering of its products for maximum economic and ecological benefits. The Raymond 4000 Series Stand-Up Counterbalanced trucks are equipped with Eco-Performance to deliver quicker acceleration and industry-leading lift and travel speeds to boost operating efficiency and maximize the number of pallets that can be moved per hour. Designed to reduce energy consumption and increase productivity in dock to stock, loading and unloading and cold storage applications, the Raymond 4250 Stand-Up Counterbalanced Truck delivers 9 percent more productivity and 17 percent more energy efficiency than competing models, based on independent third-party testing conducted by the United States Auto Club (USAC). In addition, the Raymond 4000 Series features powerful AC drive and lift that helps to increase productivity with more torque, better acceleration and less downtime; requires fewer battery changes; and reduces overall CO2 emissions—helping to support sustainability efforts in the warehouse.
Transportation Insight (www.transportationinsight.com)
Transportation Insight is an enterprise logistics solutions provider offering a bundled solution of freight bill payment and audit, carrier sourcing, transportation management and business intelligence reporting. Its sophisticated transportation management system, Insight TMS, helps food and beverage clients achieve green supply chain results through optimal mode and carrier selection. In conjunction, the comprehensive data management and logistics reporting capabilities help clients streamline supply chain networks based upon simulation with historical data to reduce energy costs, mileage and fuel usage.
Using the TI enterprise logistics solution, clients can streamline their operations by:
• Reducing freight costs on inbound and outbound shipments
• Providing transportation management systems to simplify shipment routing and execution
• Supplying actionable business intelligence reporting to help leadership monitor key performance indicators
• Auditing and paying freight invoices to significantly reduce overcharges
• Applying specific GL coding rules to freight invoices, reducing administrative time
• Assisting in the development and refining of purchasing strategies to lower costs on indirect materials, such as MRO supplies and secondary packaging
Veracity Logistics (www.veracitylogistics.com)
Headquartered in Clearfield, Utah, Veracity Logistics is a leading provider of warehousing, distribution, and transportation services. The company’s various sustainability initiatives include:
• Recycling aluminum cans
• Using alternative fuel for all forklifts
• No-idle policy for all trucks
• Best in class practices for lean operations
• Recycling plastics and broken wood
• Utilizing skylights during the day to dramatically reducing watt usage
• Receiving an alternative fuel credit each year
Witte Bros. Exchange, Inc. (www.wittebros.com)
The Witte Bros. Exchange facility uses vertical storing levelers on truck bay doors to provide a complete seal when the truck bay door is closed by removing the leveler from the opening. The savings achieved from this measure are realized in the reduction in the infiltration of outside air into the refrigerated space when the door is both opened and closed. The system involves three components, the leveler, the truck bay door, and the dock seal. Meanwhile, the company’s warehouse lighting features T-5 fluorescent lighting system and the lights are motion sensor equipped. The refrigeration system is an ammonia-based system, using recirculated liquid fed to evaporators as the design. Witte Bros. uses the Frick Opto22 control system to monitor equipment status, temperatures, pressure readings, etc. Glycol underfloor heat in the freezer is used to keep the ground from freezing. Three compressors are used in this design. Compressor-1 is used to run all the time, while Compressor-2 has a VFD to be used as the trim during peak loads. Compressor 3 is designed to be used as the backup.