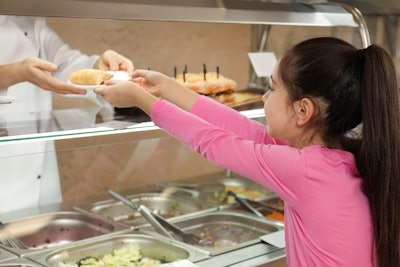
Have you finished your back-to-school shopping?
Or if you haven’t started, the last-minute dash for school supplies is met with picked over or even empty shelves.
And, this year, the rush for sneakers, backpacks, calculators and other necessities might be worse than ever.
As schools look to return to full capacity for the first time in almost two years, the National Retail Federation is estimating that the average shopper in the United States will spend $850. But, with new Coronavirus disease (COVID-19) outbreaks in countries such as Bangladesh and Vietnam causing more factory shutdowns, many retailers across the globe could be faced with a supply and demand imbalance due to low inventory levels and delayed shipments. This inability to replenish the shelves for the back-to-school surge could result in shortages and increased prices.
School food shortages – Not enough chips to go around
And, once they get to school, there is a concern about keeping children nourished, as schools are struggling to secure food, and in some cases, staff, to prepare student breakfasts and lunches ahead of classrooms’ planned reopening in the fall.
Some are cutting menu choices as food suppliers face labor shortages and transportation challenges limiting supplies and increasing costs. Food distributors and school officials say they expect to run low on everything from lettuce to lunch trays, and some worry that the lack of options will deter students from getting meals at school.
What can businesses learn from the back-to-school challenges?
Visibility across the business network into both supply and demand are key. On the demand side, in addition to tracking what customers are buying through point-of-sales data, you also need to know what they are thinking of buying by tracking market and customer sentiment analysis of what is “hot.” Visibility and collaboration on the supply side is equally important. Which shipments are at risk due to plant closures or restrictions? Which deliveries are facing delayed in-transit? Having good plans based on an accurate view of demand is important. But, equally important is the ability to respond to the expected and unexpected changes in supply and demand. This requires business systems and business process with the agility to respond to these changes.
The new 3 R’s – risk, resiliency and responsiveness. It is critical to design your supply chain to withstand disruptions and take advantage of opportunities. This requires having plans in place with the resiliency to sense and respond to supply chain risks. What are the alternate sources for a product if a supplier fails? Do I have a local supplier I can turn to? Should I keep additional inventory of key products closer to the source of demand? Can I trigger a rush delivery by air?
The pandemic has taught that the globalization of supply chains, while reducing costs, have also increased risk. Executives are now demanding more resilient supply chains that can sense, absorb and respond to these risks and come back stronger.