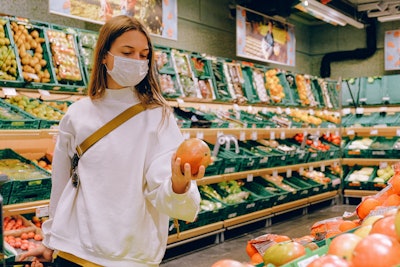
In March 2019, the Midwest was flooded for weeks. A “bomb cyclone,” an intense swirling storm, caused more than 1 million acres of cropland to be destroyed. The flooding was swift, long-lasting and without warning—the damage cost about $3 billion, according to a Reuters analysis of government and satellite data. And, that wasn’t the end. The U.S. Department of Agriculture found that 2019’s spring rains stopped U.S. farmers from planting on 20 million acres of farmland, hindering many parts of the world’s food supply chain.
Few events can devastate a supply chain faster than disastrous weather. Other business risks—such as cybersecurity breaches and product recalls—can be mitigated or prevented by a risk management program, but disastrous weather and natural disasters are generally unavoidable. They ravage businesses and their supply chains with little warning.
What’s more is, many businesses don’t plan for weather-related disasters. A report from the Met Office, UK’s national weather service, found that half of UK companies say that weather is one of three external factors that drives consumer demand, but only one-third of these companies don’t use meteorological data to assess risk in their supply chains. This is a mistake. These businesses are leaving themselves open to prolonged disruptions, critical stockouts and escalating costs amid a disaster, potentially losing millions of dollars.
While we know when it will be hurricane season, when the weather may dip into extreme cold, or when it might rise into intense heat, we can’t know when a supply chain will be hit by a disaster. Flooding, earthquakes and tornados often hit without so much as a moment’s warning. Today’s forecasting technology can predict how much rain there will be, what the weather will be and where storms are headed, but it fails to alert the industry of advanced notice of disasters. But, looking at the history of these disasters can help companies better weather-proof supply chains.
Lessons from Japan
In March 2011, the northeast coast of Japan was hit by an 8.9-magnitude earthquake followed by a tsunami. The disaster was exacerbated when a nuclear reactor in Fukushima melted down. It was one of the worst weather-related disasters in recorded history, killing 86,000 people and forcing more than 500,000 people to evacuate their homes. The disaster also harmed businesses in Japan and across the world, hitting its supply networks with $210 billion in costs. Large car manufacturers had to temporarily shut down assembly in both the United States and Japan due to a parts shortage.
We can hope a disaster of this magnitude won’t happen again, but we can’t control the whims of Mother Nature. Thus, we should prepare ourselves, our employees and our supply chains for large-scale natural disasters. One way to prepare is to look at reports on past disasters, read about what other businesses have done well (or poorly) and identify what actions are necessary for the business amid disaster.
1. Develop supply chain visibility
Managers must have visibility of their entire supply chain. With visibility, they can evaluate their suppliers’ risks of being affected by a natural disaster. This evaluation must go deeper than tier-1 suppliers—managers should also be aware of where their second- and third-tier suppliers are located. By taking this step, companies can know the risks held by each of their partners and plan for what to do if a partner is hit by disaster.
According to a study by Nick Wildgoose, global supply chain product manager for Zurich Insurance Group, 80% of corporations don’t check their supply sites for exposure to natural disasters, leaving the businesses at greater risks for disruption and loss of money.
It can be helpful to develop a map that shows what partners are located in disaster-prone areas and connect them to an early-warning communication system, which makes it easier to prepare for the next steps amid severe weather. This allows supply chain managers to check on the facilities held by the company and its partners as disaster approaches.
2. Plan for the worst-case scenario
No one enjoys thinking about what may happen if their supply chain is affected by a natural disaster. But, by thinking about worst-case scenarios, supply chain managers can be prepared for a wide range of scenarios.
Supply chain managers should write plans for preparation, mediation, recovery and redesign in the face of a disaster. If a storm hits, the value of the plan will greatly exceed the time and money spent creating it. Once managers have plans for worst-case scenarios, they can incorporate weather forecasts into their plans, giving the organization the ability to quickly prepare for disaster. Rather than being reactive to the storm, managers can take preventative measures, giving themselves a head start on mitigating risk to their supply chain.
3. Build a disaster response team
When a storm hits, managers must respond quickly. To do this, they should assemble a disaster response team comprised of versatile and knowledgeable employees. Building this team will mean training members on what to do in the case of severe weather, as no two disasters are alike.
When building a disaster response team, DisasterRecovery.org suggests using the company’s hierarchical structure to assemble the team. This clear structure will help the team quickly respond to any disaster. Organizations must define the team’s goals and objectives, clearly defining responsibilities for team members. They should also create protocols for sharing information and raising alerts with the rest of the company. Disaster response teams should be given the responsibility to modify plans and change responses to specific disastrous scenarios. The team, consisting of people trusted by the organization, should have autonomy to make decisions as they continuously learn about responding to natural disasters.
4. Build redundancy into the supply chain
Organizations must have redundancy in the supply chain. Redundancy means keeping excess capacity or backup over the entire supply chain to maintain regular functions in case an incident disrupts business.
Many businesses strive to have tightly coupled supply chains that can change with business trends. This is nice to have, but tightly coupled supply chains have a higher risk of disruption than those with redundancy.
Although redundant supply chains may cost more and be slower to change, they help supply chains become more resilient to weather-related risks.
If weather trends are any indication, natural disasters will soon worsen due to climate change. Supply managers who plan for disaster are taking an important step toward keeping their global supply chain operational, even in the worst conditions. Don’t let your supply chain be needlessly left out in the storm.