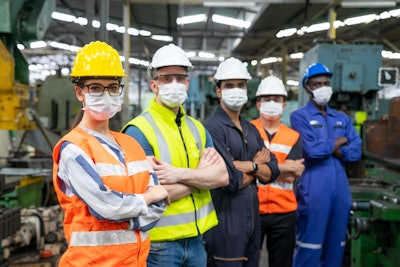
Before 2020, did your business continuity plan include pandemic preparedness? If you were like most companies, instead of being prepared, the Coronavirus disease (COVID-19) pandemic caught you and your workforce off guard.
Previously, most operations focused workforce protection measures on reducing the number of injuries on the job. Health measures were often limited to “stay home when you are sick.” In the context of this pandemic and the workplace, there is risk that the workforce will be exposed to the virus at sufficient levels to acquire infection while performing their jobs. Therefore, the response to the pandemic has required implementation of protocols and mitigation measures designed to protect the workforce against contracting the disease while at work.
The primary method of transmission of SARS-CoV-2 is through close exposure to the respiration; talking, coughing and sneezing of an infected individual. A far less common secondary mode of transmission can occur when an uninfected person touches a surface with the virus on it and then touches their face, nose or mouth. Knowing these facts and because some individuals remain asymptomatic when infected with the virus, several strategies should be considered to mitigate transmission risks and protect your warehouse workforce.
Upon entry
Before employees or visitors enter the facility, use pre-entry health checks to screen those who have symptoms and questionnaires to determine exposure, limiting the access of potential asymptomatic carriers. Once inside, all personnel should wear personal protective equipment (PPE) such as face masks, full face shields and gloves as appropriate to the operation, while maintaining implemented social distancing (6 feet or 2 meters) between individuals. Frequent handwashing and disinfecting common touchpoints should also be scheduled and required.
Facility and workforce preparation
To properly plan and prepare your workforce to maintain the best protection while at work, it is important to assess the risks in your facility. Start by determining where close contact between individuals is likely to occur and establish measures to eliminate that contact. For instance, install drop boxes for driver paperwork to eliminate a face-to-face handoff. Break rooms should be set up with fewer chairs and staggered break times to have fewer employees in these common areas at the same time. Traffic patterns should be established in the warehouse to maintain workflow while providing appropriate spacing and distancing.
A designated area to put on PPE and a separate area to remove and discard used PPE must be provided. Instructions on how to temporarily store masks when taken off for breaks should be developed to ensure that worn masks are not a source of contamination in the break room. If reusable PPE is provided, it should remain in the facility and provisions for proper cleaning between uses must be managed by the company. Third-party laundry services may be the best choice to keep this equipment clean and sanitized.
The introduction of these and other health crisis mitigation measures comes with the responsibility to communicate transparently and properly train the workforce, while then managing all measures. This will inform them of the efforts developed and in place to safeguard their health while at work. Including insights on how to protect themselves and their families while away from the warehouse will also empower them to take charge and maintain their own health.
In the warehouse
Assigning materials handling equipment, such as forklifts and hand jacks, to specific individuals for use throughout the shift is considered best practice to prevent exposure from one individual to another. Providing sanitizer wipes for sanitizing touchpoints on the equipment after handling other materials can also help prevent touchpoint transfer of the virus.
Because it cannot be ascertained who is asymptomatic and may be shedding the virus, all worn PPE must be considered as contaminated. The careful removal of masks, gloves and face shields is required to prevent dispersing the virus into the air. Disposable PPE must be discarded in designated trash containers that are effectively managed to contain the virus. Reusable PPE such as face masks and face shields must be placed in designated containers for transport to where disinfection by trained personnel will occur. While not considered a biohazardous material, control of PPE disposal is still required to prevent the spread of the disease.
If the warehouse operation has delivery drivers associated with the site, keeping this pool of employees segregated from the warehouse workforce is a best practice. The use of separate break rooms and rest rooms is considered an effective measure, while outside drivers should be restricted from accessing facility break rooms and rest rooms to mitigate potential viral transmission to company employees. Providing them and other visitors portable toilets outside the facility and restricting their access to this area only is a proven mitigation measure.
A positive test
If an employee does test positive for the virus, they should be required to notify the company, while the area that employee worked in should be quarantined and disinfected. Employees must trust that reporting illness and staying home when sick will not result in disciplinary action. It must be communicated and understood that this is for the greater good of the entire workforce.
When sick, employees should be required to stay home, with management facilitating contact tracing to identify any individuals exposed to that employee. Those with known exposure to the virus should quarantine at home and follow CDC guidelines for a safe return to work. Management should also follow protocols to report positive cases to the appropriate health agency, if required.
Planning, preparing and implementing health crisis mitigation measures in the workplace will ensure everyone that their health and well-being are priority, while ensuring that the facility is better prepared for the future.