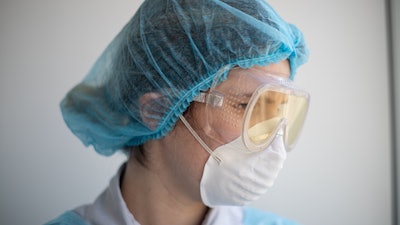
According to John Hopkins University, over 73 million people worldwide have tested positive for the Coronavirus disease (COVID-19), many of whom are essential supply chain workers. We have seen just how difficult it can be to prevent the spread of this virus, as this airborne disease is often undetectable within asymptomatic carriers. However, there are measures to implement today to ensure companies are taking all possible precautions to keep essential workers safe for tomorrow.
What precautions farmers take against the spread of disease
Farmers depend on their livestock for a living. If an animal gets sick and spreads disease to other animals, the farmer can lose everything. The process farmers utilize to protect their animals from this threat can also be leveraged to protect humans.
First, before entering a farm, you must dip the soles of your shoes into a solution to ensure no disease is being brought in by foot. This process is repeated every time you step into a new area of the farm and is important in preventing cross contamination between different areas and livestock. Before entering the farm, you must also be sprayed down with a disinfecting mist. This helps kill any bacteria or virus that may be living on your skin, hair or clothing. Similar protocols can be deployed into every phase, facility and area of the supply chain to protect workers from contracting and/or spreading COVID-19 this winter.
Find alternatives to using antimicrobial soap
Antimicrobial soap actually eliminates both the bad and the good bacteria on your hands. This means that the more you use it, the greater the potential for dangerous microorganisms to adapt and for healthy bacteria to lose its ability to protect your skin. To counter this phenomenon, it is recommended that you stick to regular soap and water when washing hands. Using these solutions will eliminate proteins and contaminants on the skin and on surfaces better than the traditional anti-bacterial wipe. It is also important not to over-use sanitizer, as Australian researchers have raised some concerns about superbug resistance to hand sanitizer in hospital settings. To avoid virus adaptation, choose natural, non-toxic solutions.
While simple dish soap and water can work to clean surfaces, it is important to remember that COVID-19 is still primarily an airborne virus that is most transmissible in poorly ventilated indoor environments and/or in close proximity to others. This means that it is essential for the safety of workers in factories and distribution centers to regularly and properly ventilate, filter and clean the air that circulates around them. Simply opening as many windows as possible can help keep the air fresh and flowing. It is also possible to implement non-corrosive, non-noxious treatments capable of cleaning the air and eliminating the virus from the premises without having to relocate any workers or disrupt production. The benefit of this type of solution is that it will not adapt to the virus or bacteria it is cleaning, so no superbug can be formed.
Make it mandatory to wear gloves and masks
Another way to protect employees is to make it mandatory to wear gloves and a mask simultaneously.
First, employees should know how to use gloves appropriately. According to Allure, changing gloves every time you change settings is imperative. This means if you’re going inside a grocery store, you’ll want to put on a fresh pair of gloves before entering and taking them off before entering your car.
It’s also important to pair correct glove use with correct mask use. Similar to gloves, you’ll want to be diligent about changing masks and cleaning them, if possible, after trips outdoors. When the two are combined together, you lower the risk of contamination. If you are only wearing gloves (without a mask) when exposed to COVID-19, touching your face can greatly increase the likelihood of infection and transmission. To take extra precautions, employees should be trained on how to properly remove gloves, so they aren’t exposed in the process. Remove the gloves (inside out) and place them inside a bag. Then, dispose of the bag in a designated area. This process may be tedious, but significantly decreases the risk of contamination.
Why these steps are important
Implementing these extra measures does more than just ensure the health and safety of supply chain workers — it also helps maintain their job security. Not every state guarantees paid sick leave for COVID-19 infections, and a known COVID-19 outbreak during any point of distribution can lead to an entire shutdown of the factories involved. These shutdowns can vary in length, as deep disinfection measures must be taken to ensure all traces of the virus have been eliminated from these locations (which often requires emptying the facility of any and all personnel to complete). Without compensation protection, this can dramatically impact the livelihood and well-being of each of your employees.
Ultimately, keeping your essential employees safe and working should be the No. 1 priority. After all, they are risking their health every single day to keep businesses and the economy running smoothly. Implementing these solutions and protocols to ensure their health and safety is an important step toward eradicating this virus from the supply chain and production lines, reassuring teams that their health is at the forefront of your consideration and protecting those vulnerable who may come into contact with your facility, employees or products.