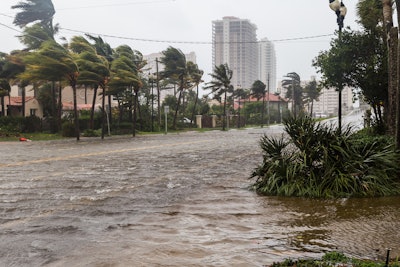
Over the last decade, the United States has experienced over 200 natural disasters, including winter storms, flooding, wildfires, and tropical storms, causing more than $1.4 billion in damage
Dealing with disruption by disaster is not new for shippers, especially when it comes to hurricanes. Last year, Hurricane Ian caused $109 billion in damages when it hit Florida as a Category 4 storm. Freight delays were expected, of course, mainly due to power outages and flooding. These forced interruptions affected both roadways and distribution centers, but ports and airports preemptively closed as well. As a result, recovery took months.
Experts are reporting above average activity for this year’s hurricane season, despite predictions of “near normal” just a few months ago. Fluctuations like these serve as reminders that we cannot predict the future entirely. However, as of now, we are looking at a total of 18 named storms, with nine becoming full-blown hurricanes and four becoming major storms.
On a high level, the most important thing for shippers to do is plan. Shifting operations for proactive continuity will not only lift up business, but improve resilience for the entire supply chain in the face of disaster.
Shore up preparedness plans with data
Some shippers don’t focus on how hurricanes will affect their warehouses until a major disruption actually happens. But by the time disaster strikes and the warehouse is flooded, it’s too late.
Small shippers, in particular, often don’t have the best preparedness plans. They might rely too heavily on a single transportation mode – often trucks – that leaves shipments in a lurch when hurricane damage happens. Consider alternative options like rail or air freight. Shippers should also be aware of transportation regulations and restrictions that may be enforced during hurricanes. Neglecting to follow these policies can lead to non-compliance issues, further delayed shipments or legal problems.
Most often, shippers struggle with the way their data is fragmented and siloed, with information distributed across multiple spreadsheets. There is virtually no way to gain a comprehensive, real-time understanding of what is happening and how one failing in the system will affect another part.
But with the right tools, leveraging data and predictive analytics can help shippers become proactive instead of reactive. They are able to cull data together from the previous years – or even the past decade – to reflect on disruptions and figure out where to bolster operations and move ahead of time.
For example, data can help spot weaknesses from the previous season to resolve them before the next happens. Common problems tend to be a lack of robust tracking and monitoring for shipments during hurricanes or a limited assessment of risk when it comes to transport routes.
With data informing their preparation plans, shippers can turn their attention to catching challenges as they happen and preventing new ones.
Strengthen communication and relationships with carriers
Both shippers and carriers want to secure great rates and move more product. But it takes the right carrier partners to collaborate effectively and promote each other’s businesses. Shippers should look into accessing a diverse network of proven, trusted carriers to establish a relationship with during, and beyond, the season.
Communication methods with carriers will also define the impact of the upcoming hurricane season. Shippers will likely not have more than one week at best to know for certain whether a storm will disrupt warehouses; sometimes they might not know precisely until right before landfall.
Each distribution center should have localized contingency plans, especially in hurricane-prone areas like Florida. Shippers may need to run leaner operations in affected areas depending on how much response time you receive when a storm approaches. Pay attention to where and when shipments should be rerouted and create a list of alternative paths, depending on where the storm is heading.
Additionally, work with carriers to ship cargo earlier than normal and more efficiently. Solutions like digital PTL offer a more efficient way to move packages and consolidate shipments. Make sure there’s a plan with carriers in place in advance so that when the storm actually hits, no one is scrambling to find solutions.
Invest in modern operations tools
Digital infrastructure tools can help accelerate the growth of capacity, while ensuring it is optimized and speedy. They also help procure accurate, proactive rates so that there is guaranteed capacity behind the price.
Consider phasing out manual processes for a more modern option that provides holistic visibility, such as a “virtual warehouse.” In a traditional warehouse, orders have to be picked up and manually consolidated. In an algorithmic virtual warehouse, there’s real-time, centralized visibility into people, cargo, and end destinations. Similar commodities can be combined into one shipment, which helps optimize rates and reduce excess costs.
It’s time to ditch outdated tools. You can’t afford to rely on manually transferring data and communicating mainly through phone calls. You need to move faster than your competition and – against all odds – faster than a hurricane.
We often call natural disasters like hurricanes “Acts of God” because the reality is that they’ve happened since the dawn of time and will always be around. But with the right methods, shippers can improve their side of the supply chain to weather the storms and bounce back even quicker.