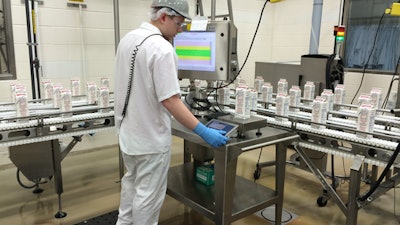
Quality is a top priority for manufacturers in every industry. After all, trustworthy products earn the loyalty of buyers and consumers alike. But, when defects lead to a recall, it costs companies big-time. They often lose millions of dollars in direct costs, and perhaps even more in the long run from damaged brand reputation.
The stakes are particularly high in the food and beverage space, where quality issues also put consumers’ health at risk. As such, food and beverage manufacturers must adhere to strict regulatory safety requirements, performing routine quality and compliance checks throughout the production process.
But, with so much on the line—and so much legal complexity to navigate—it may come as a surprise that many facilities still rely on paper checklists and manual methods to collect and analyze their quality data.
Pen and paper problems?
Paper-based data collection is not only time consuming, it’s also fundamentally susceptible to human error. That’s not to say that shop-floor employees are to blame. It’s the process itself that is cumbersome, with too many opportunities for mistakes. Just consider the steps involved.
Employees first write the information on a piece of paper. Once the paper form is complete, the values are entered into a computer spreadsheet. The data is eventually reviewed at the end of a shift or batch, and then paper forms are stored away with a mountain of other records. Now imagine repeating this over and over, and it’s plain to see how errors (like transposed numbers, misinterpreted handwriting, miscalculations, etc.) could be made by even the most diligent employee.
Moreover, this method also makes it nearly impossible to anticipate quality problems before they occur. Instead, operators and quality professionals end up basing decisions on only the most recent data, spending their shifts reacting to one problem after another. Even then, some production issues are only detected after it’s too late to take corrective action, meaning wasted resources, lowered profits and damaging recalls. Predictive trends and signals are completely lost when focusing only on data from the moment.
So, if today’s food and beverage companies want to be successful, they should retire the pen and paper. It’s time to embrace a more modern solution, perfectly suited for their quality needs—statistical process control (SPC) software.
Meet the modern solution
What is SPC? It’s an industry-standard methodology for measuring and controlling quality during the manufacturing process. Essentially, SPC software allows manufacturers to collect and chart quality data against pre-defined control limits to identify product variations or process problems in real-time.
Food and beverage manufacturers can thereby:
1. Speed up response times. Because we don’t live in a perfect world, deviations from product safety, quality and consistency are bound to happen. As soon as a problem is detected, SPC software sends immediate alerts to notify operators and responsible parties of the issue. Unlike paper forms, software also provides insight into the root cause of—and solution to—the defect. Operators can then take corrective action early on, preventing unsafe or defective goods from ever entering the supply chain or reaching consumers.
2. Ensure accountability. Quality and production teams have good intentions, but their attention is often split between putting out fires and performing daily tasks. Routine quality checks could fall by the wayside as more pressing crises take precedence. Moreover, manual data collection makes it hard to confirm that compliance to required timeliness and accuracy were met. But with SPC software, manufacturers can verify these activities are performed in a timely manner, validate the identities of individuals collecting the data, and guarantee the accuracy of recorded values.
3. Streamline audits. On top of the daily demands of safety regulations, audits add another layer of complexity for quality and production teams (and not to mention stress since a failed audit can mean fines and extended suspensions). Auditors require manufacturers to provide a lot of data encompassing a wide timeframe, and those that rely on paper records can struggle to locate, piece together, and report that information. As a result, audits may take several days or even weeks to complete.
Conversely, SPC software organizes, centralizes, and stores historical data organization-wide. Manufacturers can easily verify ongoing compliance with industry regulations, and in the event of an audit, provide requested data to auditors in hours or even minutes.
4. Refine critical processes. SPC solutions can be used to improve in-spec processes—further reducing scrap, waste, defects and re-work. A great example is net content. Because manufacturing processes are complex and variable, it’s nearly impossible to make sure a precise quantity of product fills each package that speeds down the production line. To err on the side of caution, many manufacturers will fill their packages more than what the label states. While this strategy keeps consumers and regulators happy, the cost of overfilling builds up fast by way of product giveaway.
SPC software offers precision to ensure net content consistency over time. Organizations can monitor differences in fills from one machine to another, from one product to another, and from one plant to another—and adjust as necessary to reduce waste and giveaway. Overall, such process refinements result in significant savings over time, lowering productions costs and supporting a profit-positive business model.
5. Transform data into insight. Though all manufacturers collect quality data, many lack the tools to pull any meaningful information from it. It’s here that SPC software really shines. It can aggregate and analyze historical data, highlight opportunities to improve product quality, and mitigate safety risks. With this insight, manufacturers can implement preventative safeguards and quality measures. This proactive approach not only preserves brand image and protects profits for manufacturers, but also guarantees safe, trustworthy goods for consumers—which is what’s most important in the food and beverage industry.
Change can be scary—but don’t let it hold you back
In an increasingly digitized world, manufacturers that fail to adopt new technology to meet industry standards will fall behind the competition. What seems to deter most food and beverage manufacturers from moving forward with an SPC solution is concern over learning a new system in an already-complex environment.
While it does involve a learning curve, SPC ultimately simplifies the jobs of quality and production teams. And with the benefits of SPC software realized almost immediately—namely, reduced risks, greater profitability and consistent adherence to food safety and quality standards—it’s no wonder SPC is an industry best practice.