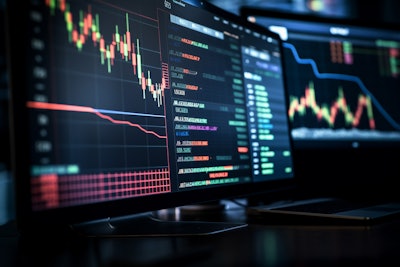
In the first three months of 2024, the number of FDA food recalls increased by 27.6% from the previous quarter, reaching 134 recalls, the second-highest level in four years. The impact on consumer confidence in food and beverage manufacturers is dwindling.
Leveraging technology for traceability and transparency will become an industry standard with the ability to quickly trace sources of contamination and isolate affected products in real-time. Food and beverage manufacturing solutions provide technicians and engineers with immediate access to data needed to make informed decisions for their everyday maintenance tasks that impact widely scaled food safety and quality control. Now more than ever, the stakes are high for manufacturers to invest in environmental monitoring of facilities through preventative, predictive and prescriptive maintenance.
Preventative maintenance
Food and beverage manufacturers need the ability to do “rounds” on their factory lines and products at all times, also known as preventative maintenance. This includes monitoring temperature, humidity, and checking assets for contamination. Scheduled routine maintenance activities can predict equipment failures before they occur – this proactive approach helps minimize disruptions in production, ensures the availability of essential machinery, and keeps products safe during the process.
For instance, an important preventative maintenance process is the routine inspection and servicing of refrigeration units used to store perishable ingredients. Regular checks on compressor performance, coolant levels, and temperature sensors help ensure that these systems maintain optimal conditions to prevent spoilage. By proactively replacing worn components, manufacturers can avoid unexpected equipment failures that could lead to product loss or safety hazards.
Not only is preventative maintenance important for the machinery itself, but also for the building automation systems where the machinery lives. Systems such as HVAC, refrigeration, and lighting directly impact the operating environment, influencing factors like temperature, humidity, and air quality that are critical for food safety and product consistency. Regular maintenance of these systems creates a stable environment that supports optimal machine performance and extends the lifespan of equipment.
Predictive maintenance
Predictive maintenance, on the other hand, is a proactive approach that uses data-driven technologies to monitor equipment performance and predict potential failures before they occur. By leveraging sensors, IoT devices, and advanced analytics, manufacturers can track critical metrics like temperature, vibration, and pressure in real-time to enable early detection of anomalies, abnormalities, and malfunctions.
For example, dairy manufacturers have an emphasis on machine vibrations, so they have sensors that help with real-time vibration analysis. This ensures that if a machine is not working properly, they can quickly address the problem and contain any contamination or affected dairy products. Additionally, real-time predictive maintenance reduces the number of rounds needed on equipment, saving valuable time and resources.
Not only is this necessary from a cost and safety perspective but also needs to be tracked for the sake of compliance. The food and beverage industries are heavily regulated, with strict standards for food safety, hygiene, and equipment maintenance. Predictive maintenance ensures compliance with these regulations by tracking and managing maintenance activities, inspections, and documentation.
Prescriptive maintenance
Prescriptive maintenance takes things a step further by providing actionable guidance on how to respond to issues effectively. This process focuses on determining the root cause, estimating the potential cost, and recommending precise remedies to mitigate the issue as quickly as possible. In the fast-paced environment of food and beverage, this approach ensures that every maintenance event is met with a clear and efficient plan of action, reducing the time spent diagnosing and resolving issues.
Using advanced technologies like AI and machine learning, prescriptive maintenance systems analyze historical data from past failures to refine response strategies continuously. Every time an issue is encountered, the system learns from it, identifying patterns and remedies that can be integrated into real-time monitoring devices. This creates a dynamic feedback loop that empowers technicians with detailed procedures, ensuring the right person with the appropriate skillset arrives prepared with the tools and knowledge needed to resolve the issue swiftly. As a result, this minimizes unnecessary downtime and reduces the risk of disruptions to production schedules.
When food safety is paramount, asset downtime can lead to contamination risks and having to issue a recall or loss of product, both of which impact consumers trust in the brand. Prescriptive maintenance directly addresses these challenges by helping manufacturers avoid costly waste and ensuring a consistently safe production environment.
Food safety is increasingly in the spotlight as advancements in technology provide better tools to address long-standing challenges in the complex supply chain. Unlike in the past, when manufacturers had to accept certain risks, modern automation and innovative solutions now allow for tighter control over environmental conditions, even during transportation. These advancements not only help mitigate risks but also enable the production of higher-quality, safer products, ensuring greater confidence for consumers and efficiency for manufacturers.