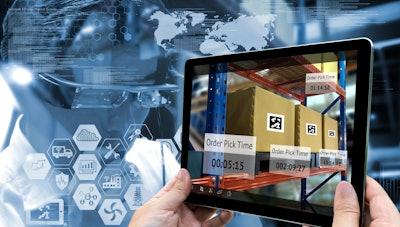
If there is one thing food and beverage companies want to avoid, it’s a food recall. However, despite the severity of recalls and warnings from the Food & Drug Administration (FDA), they remain a common problem for U.S. food and beverage companies, many of whom still burdened with manual processes and on-premise data.
Already this year, the FDA has enforced a recall of more than 11,000 containers of ice cream due to potential metal contamination. While many assume that blame solely falls on food distributors, recalls are most often best described as supply chain problems that have made their way to consumers. Fortunately, in almost all cases, these problems are entirely preventable with a technology-driven strategy that optimizes supply chain transparency.
Mitigating the risk of expensive supply chain problems and ensuring that customer faith can be quickly restored after an incident depends on deep visibility into all events along the supply chain that could impact food safety — from raw materials right through to consumers’ tables. While most U.S. food and beverage companies seek to continuously improve their food handling operating procedures, it’s virtually impossible to manually predict every possible event that could lead to a food safety issue or recall. It’s therefore critical that food and beverage companies prioritize technology-driven transparency for their supply chain.
When deployed strategically, modern cloud-based supply chain management (SCM) systems can dramatically improve supply chain transparency. Not only can these cloud SCM systems offer food and beverage companies a real-time look into all operations, materials, outputs and partner relationships, they also can boost operational agility and help them stay on top of consumer habits and regulatory changes. Cloud-based SCM solutions can also boost mobility, accessibility and communication to let manufacturers, farmers and distributors more effectively collaborate and detect potential issues before they reach grocery store shelves. These SCM solutions can also incorporate artificial intelligence (AI) capabilities to help businesses predict and prepare for potential problems ahead.
In addition, modern cloud-based SCM systems can also ensure precision by providing detailed information to quickly isolate and recall all finished goods and raw materials associated with any suspected product quality or safety issue. This is crucial, as it does not take much to nullify a company’s traceability efforts. For instance, if a specific lot is allocated for production, transfer or shipping, but another lot is instead pulled and that change is not manually entered into an enterprise resource planning (ERP) system, the company’s tracking will prove inaccurate. For food and beverage companies, this accuracy afforded by modern cloud-based SCM systems is needed to protect brand integrity, consumer confidence and the bottom line.
Equally important to preventing issues from arising in the first place is the ability to swiftly and precisely handle any critical situations that may occur. Customers, consumers and regulators all expect food and beverage companies to take a proactive and responsive approach to quality and food safety, so when something goes wrong, it is imperative to quickly find the root cause, identify which customers were impacted, notify regulators and rapidly contain the issue. Companies leveraging a cloud-based food traceability software architecture will be well prepared and able to pinpoint these issues, quickly communicate the right information to the right stakeholders, minimize production downtime and cost and ultimately reduce damage to their brands.
As part of a technology-driven strategy to optimize transparency, food and beverage companies should also consider the benefits of data and information sharing beyond the walls of their organization to broadly reach consumers. For example, QR codes on packages can share critical messages with today’s information-hungry customers — from food origins for traceability to ingredients for nutritional guidance. This deep visibility helps companies safely track the quality and safety standards of their products at every link of the supply chain—mitigating risk and keeping customer experiences positive. Cloud technology also can help companies keep track of when, where and how their products are reaching consumers, so marketing efforts can be continuously improved.
A product recall is a reactive measure and does not bring the organization forward — except to potentially learn from the issue to avoid an even bigger recall in the future. Most times, there is no advance warning that a recall is going to occur, and any recall an organization experiences can be “the one” to bring down the whole company, crippling trust in the quality of products. Being a step ahead is the only viable option. By prioritizing supply chain transparency via a cloud-based, technology-driven strategy, businesses can start moving forward with confidence that the risk of crippling recalls is reduced.