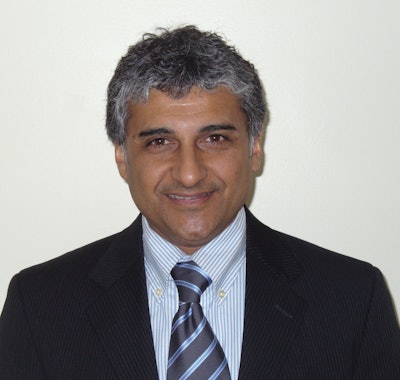
At the Georgia Tech Integrated Food Chain Center, we recently introduced FIRM, the Food Integration Reference Model, to provide a framework for developing and maintaining standards. FIRM consists of three levels: A supply chain view showing how produce items are distributed from the farm to retailers, including all the sites visited in between; a site view that shows the value chain of the produce items within each site; and a process view that details the implementation of each step in the value chain. Standard specifications for safe and effective operations are generally specified at the site level, whereas the implementation of the standards occurs at the process level.
In addition to providing ways to specify and implement standards, FIRM also provides an integrated framework for managing and evaluating the food supply chain. The figure (right) shows how shows how FIRM can be used in practice to manage operations, monitor performance, analyze compliance, and improve the supply chain.
At the heart of FIRM is the value chain of the produce from farm to retail and the different integration zones where the product goes from one site to another. The integration zones include activities such as load/unload, retrieve/put away, the waiting periods between these activities, and the transportation between the sites.
It is estimated that produce items spend up to 50 percent of the time between the farms and the retailers in the integration zones. It is also generally agreed that these zones are the major risk points in the supply chain as numerous issues can arise in these areas (e.g. poor loading configuration, poor air flow, failure to pre-cool, refrigeration units malfunctioning or turned off, temperature set wrong, product too long on loading dock, no documentation of product origin, etc.) that may result in a loss of information, in product contamination, or a degradation in quality and shelf life. Most of these problems are due to the fact that there are no generally accepted standards or even a standard vocabulary that can be used to communicate best practices to the numerous partners in the global food chain.
In its first version, FIRM will attempt to provide standards and a standard vocabulary for the integration points. The standards will be derived from best practices that are generally known by experts in the field. They will be vetted by a group of core users and voted into standards. For example, in the guide Refrigerated Trailer Transport of Perishable Products, published by University of California Agriculture and Natural Resources Communication Services, Thompson et al. describe the processes for selecting and using boxes for shipments, load planning that includes selecting compatible produce items for shipping based on temperature needs, ethylene sensitivities, relative humidity needs, odors or chemical treatments, airflow characteristics, and use of ice. They also give an 8 point process for loading a refrigerated transport trailer with details on how to brace loads with airbags, keeping a space between the walls and the loads, and give names such as pinwheel, staggered, centerline and others to the various loading patterns of pallets in the trailer. This provides a starting point for the standards and vocabulary.
Next, we need to specify minimum clearance by product type for airflow, how and where to place temperature recorders, how many should there be, and derive standards, specification, and best practices by produce items for the various activities involved in the integration points that can be understood, translated, and accepted globally.
The specifications will also include key data elements that should be captured or measured at critical points throughout the supply chain for safety monitoring, performance evaluation, and traceability. Once this data is available, a standard set of metrics can be computed and the supply chain evaluated for compliance and performance. The latter is then used to enable traceability, certification, and audit, and provides a feedback loop for continuous improvement of supply chain performance through enhancements at the process level.