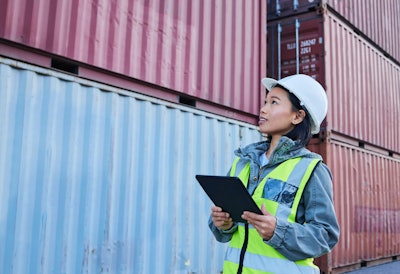
When thinking about theft, oftentimes many believe that crime is exclusive to retail brick-and-mortar locations. While retailers do lose billions of dollars from theft annually, warehouses and trucking companies also face an alarming amount of theft incidents to the tune of more than $223 million in losses last year alone.
With new products shuffling in and out of warehouses and delivery trucks, it’s not surprising to see these locations as targets. This constant movement of goods is making it easier to intercept millions of dollars’ worth of items directly from manufacturing or shipping hubs.
As theft continues to rise, so has a knowledge gap among frontline workers, with many admitting they don’t know the standard processes in place for detecting or addressing theft. In other words, there’s a greater need for stronger training in the workplace. With improved and continuous learning, supply chain and manufacturing workers can be better equipped to handle theft and similar crimes. Let’s explore what the right kind of training looks like and how it can have a significant impact on organizations’ asset protection strategies.
Warehouse and trucking workers today face increased theft and criminal activity
Theft can happen anywhere, any time, and often looks different in each instance. In some cases, it involves physical break-ins at warehouses or intercepted deliveries. Cargo theft has actually increased by 41% since last year, leaving untrained warehouse and trucking employees feeling unprepared against the rising and volatile trend.
In other scenarios, goods are obtained by using fraudulent credentials, coercing frontline workers into placing items in the wrong hands. Through social engineering, for instance, thieves can obtain a customer’s credentials, and then use those credentials to pretend to be the customer and acquire their orders. Other times, they can fake credentials to pass as a legitimate customer, taking someone else’s products along with them.
Regardless of which tactics are being used, frontline workers must be in-the-know on how to detect them, and what to do if they see it happening. When safety is at stake, like in the case of theft, it’s critical for workers to be consistently trained and reinforced in the approved process for handling these situations properly and safely.
The importance and benefits of scenario-based training
Training for theft detection and prevention is a unique challenge, especially since workers are potentially navigating dangerous or even violent scenarios. To help workers better understand what these situations may feel like in the moment, employers can look to scenario-based learning (SBL) options.
SBL allows frontline workers to put themselves in the shoes of an employee confronted with a volatile scenario by seeing, hearing and feeling how one would during that situation. Simulation training helps employees practice walking through the steps to, providing valuable exposure without putting anyone’s safety at risk.
Companies should tailor the scenarios to mirror specific challenges faced by warehouse and trucking workers—like the unique layout of individual warehouses, the types of inventory being handled and the routes truck drivers commonly drive. Feedback is also important, so organizations utilizing SBL should plan to provide feedback and/or an evaluation after each scenario, highlighting the successful strategies that were used and any areas for improvement. This hands-on training approach helps frontline workers develop the necessary skills to identify and respond to theft incidents promptly and appropriately—and safely—according to a company’s guidelines.
The benefits of SBL training methods are endless. They offer better learning engagement and knowledge retention across the board and a safe and controlled learning environment and can easily be incorporated into any existing training or enablement program. By embracing SBL, companies are empowering their frontline workers with practical experience, improving the overall security posture of an entire organization.
Continuous and relevant training is key to keeping skills fresh while also preventing gaps
Many manufacturing workers today only receive training a few times per year, with the emphasis usually on onboarding. Training is important when workers first start a new job, but in order for that training to really stick and be impactful, employers must keep up with those skilling initiatives throughout workers’ tenures at the organization. One of the best ways to ensure that is by offering routine on-the-job training and learning opportunities that are continuous and relevant.
Oftentimes, manufacturing workers are being trained on irrelevant topics that don’t necessarily help them to successfully complete their jobs. One way to guarantee training is continuous and relevant is by updating training materials in response to different industry trends and shifts. For example, if employers are seeing an increase in cargo theft, training for truck operators and warehouse workers should be updated to include content on strategies for proactively and safely detecting and addressing theft, highlighting the most recent tactics and approaches being used by thieves. Providing training at the right time on trending topics helps companies ensure their frontline workers have the skills and knowledge needed to handle the conflicts and scenarios they are most likely to encounter during their shift.
Conclusion
The need for better frontline worker training across the manufacturing industry is evident and organizations today are taking notice. To achieve stronger organizational success and reduce crime overall, implementing robust and continuous training will empower frontline workers to play an active role in responding and preventing warehouse and truck theft. Companies must also utilize different training methods, like SBL, to help workers become adept at handling any situation. A well-trained, alert and supported workforce means less risks and losses for a company, as well as a safer working environment for all.