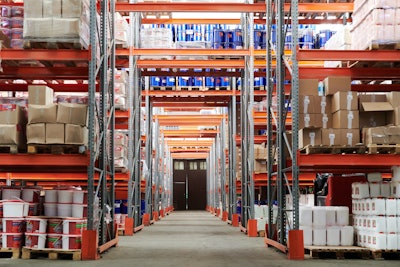
The global health crisis has created an inventory emergency for many retailers. Today’s unpredictable and volatile customer buying habits are limiting the effectiveness of using historical data to predict purchasing behavior and plan product inventory accordingly. Powered by machine learning, the new Oracle Retail Inventory Optimization Cloud Service can sit between a retailer’s forecasting and supply chain systems to help highlight the next best actions they can take to optimize inventory. This helps retailers get to answers on inventory placement and volume faster so they can better serve customers while maintaining a healthy cash position.
“Retailers are struggling to adjust decades of well-defined inventory and traditional supply chain management processes that have been thrown a curveball by COVID-19,” said Jeff Warren, Oracle Retail vice president of strategy and solution management. “With the ability to be deployed in just weeks, Oracle Retail Inventory Optimization Cloud Service does the heavy lifting and modeling to rebalance and optimize inventory so retailers can invest in the right products and automatically adapt to new consumer patterns as they occur.”
In today’s climate, the ability to respond to changing customer demands as quickly as possible is critical. Oracle Retail Inventory Optimization Cloud Service comes with pre-built machine learning models that more accurately predict overall inventory levels; recommend inventory re-distribution; balance supply and demand to free up money tied up in excess inventory; and more.
The cloud service easily integrates with existing forecasting and supply chain solutions and can be deployed quickly to reduce the burden on a retailer’s IT and development teams.
Making Inventory Work
Consumer habits in recent months have been anything but typical as shortages spurred the need for people to try new brands or stores, and the desire to go out less has led to fewer shopping trips, but often larger overall grocery purchases. As a result, inventory moves out of the stores faster, creating a strain on both the supply chain and its financial model, leading to a gross margin problem.
For example, an average grocery retailer, with 30,000 SKUs and at least 1,000 stores, will have millions of SKU-store combinations. Determining the optimal replenishment plan when things are changing so rapidly is almost impossible without the help of purpose-built, machine learning models.
With Oracle Retail Inventory Optimization Cloud Service retailers can simulate and forecast optimal inventory positions and parameters to eliminate trial-and-error. As a result, supply chain executives and chief financial officers can come together to navigate tricky terrain, manage cash flow, and determine the impact of inventory on the balance sheet. The autonomous solution self-learns and automatically tunes to optimize working capital and deliver fast value by:
- Performing continuous optimization of replenishment parameters;
- Informing replenishment strategies with service-to-inventory trade-offs;
- Translating objectives into machine learning-driven replenishment policies down to the item-location;
- Recommending inventory re-distribution to serve customers and avoid markdowns;
- Enriching the inventory movement processes with time-phased inventory projections;
- Helping increase employee productivity to maximize a constrained workforce; and
- Interacting with Oracle Retail Offer Optimization to drive better outcomes through simultaneous manipulation of supply and demand.