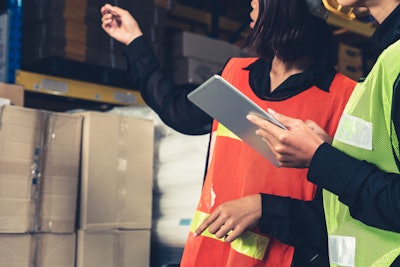
Warehouse optimization is the process of maximizing the efficiency and productivity of a warehouse operation. It involves evaluating and improving various aspects of warehouse operations, such as inventory management, space utilization, equipment utilization, labor utilization and order fulfillment.
When done correctly, warehouse optimization increases throughput, reduces costs, improves customer satisfaction and minimizes waste. By optimizing warehouse operations, companies can improve their bottom line, increase their competitive advantage and provide better customer service.
Most companies use a Warehouse Management System (WMS) to automate warehouse or distribution center operations. A WMS is stellar at ensuring execution happens, but ineffective at orchestrating activities. WMS systems are good at managing inventory, inventory age and space; managing a work queue; zoning a distribution center; and effectively cataloging and visualizing all receipt, shipment and order information. However, what if there are labor issues and adjustments need to be made? Or, what if there are questions about who is working in a zone and what work is being done in that zone?
A WMS cannot:
- Understand labor, space, and task constraints to optimize entire site operations.
- Intelligently allocate inventory and manage cuts.
- Create chained tasks that factor in proximity-to-task for all associates.
- Manage receipts and shipments simultaneously to ensure the right inventory movements are optimized.
- Transfer inventory across multi-building campuses.
Although the WMS provides critical data throughout the warehouse, this data needs to be visible and usable. This is where optimization kicks in.
Many companies are adopting a new breed of technology called a "data replica," which creates an easy-to-access database that pulls real-time WMS data for querying, visualization and alerting. Then, the data can be used to understand the future state of the DC. This is often called "what-if" planning and leverages digital twin technology. A digital twin is a mathematical warehouse model that analyzes all future-facing activities to predict what is likely to happen. An excellent digital twin will account for labor, shipments, inventory availability, tasking and space/resources.
Prescriptive software ties together all your different software, capabilities and constraints to create a single unified plan for everybody and everything to execute against. Also known as Warehouse Resource Optimization, the tool will tell you when to release work, to whom, how long it should take and where that flow will output into the following process. This results in completely optimized sites, all operating against a single picture to maximize output and minimize costs. Trailers turn faster, inventory is touched less, there are fewer disruptions and problems in the flow are called out well ahead of time.
Optimization Technology and Warehouse Resource Planning
Being able to fulfill orders quickly and accurately is the primary goal of any warehouse. Companies must automate all operational warehouse decision-making in a capacity-considerate way, freeing people to fight the fires that pop up. Many companies employ specialized software to assist with warehouse optimization efforts.
For example, an autopilot planning system leads to indirect labor savings, increased fill rate, increased load on time and productivity improvements across direct labor by optimizing the work historically released and executed by warehouse operators.
By augmenting workflows with artificial intelligence (AI), machine learning (ML) and digital twins, distribution operations can become more agile and responsive to changing market conditions and better adapt to customers' needs. These technologies can help distributors make more informed decisions, reduce costs and improve operational efficiency, improving customer satisfaction and profitability.
Using intelligent warehouse orchestration that works with a WMS, warehouse managers can look across the fragmented operations in a warehouse and optimize labor, touches and inventory to drive efficiency and create value. Often called WMS Accelerators, Warehouse Resource Planners or Warehouse Optimization Planners, these tools integrate data from across the enterprise, creating a unified view of the operations. The digital twin, artificial intelligence and machine learning technologies can be applied to determine what must be done to meet schedules and create optimal plans.
WMS accelerators adapt and rebalance activities based on what happens inside a warehouse in near-real time. WMS accelerators rearrange schedules, review labor requirements, schedule replenishments, cross-dock orders and ensure shipments arrive on time and in full. They ensure the right amount of labor shows up at the correct dock with the inventory needed to fill orders.
What problems does intelligent warehouse orchestration solve?
- It allows work to be released intelligently, to maximize automation productivity.
- It optimally sequences inbounds and outbounds to expand cross docking and interleaving proactively.
- It chooses the optimal dock door to minimize travel.
- It releases work and dynamically updates the work queue to increase order fill.
- It systematically releases work to case and layer pick based on labor capacity, inventory availability and demand.
- It sends proactive warnings about capacity shortfalls and missed OTIF.
- It eliminates repicks by replenishing to schedule.
- It allows workers to load outbound orders directly off the production line.
- It positions, transfers, and relocates inventory between buildings.
- It reduces detention in the yard by managing door turn times.
- It drives capacity-constrained yard moves: what trailer, where, when.
Warehouse optimization benefits
Warehouse optimization increases efficiencies within the warehouse by better managing inventory, more efficiently managing order picking and packing, and making more effective use of the warehouse space. Products will be delivered on time and in full so that customers are better satisfied, which can increase loyalty and word-of-mouth recommendations. Warehouse optimization improves labor productivity, reduces inventory carrying costs and minimizes waste, resulting in significant cost savings.
Finally, optimized warehouse operations help companies become more agile and flexible in responding to changing customer demands. Companies stay ahead of the competition and thrive in this dynamic market.