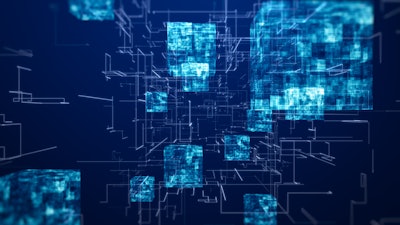
The global pandemic has changed the way goods are made, sold and purchased, creating global supply chain problems that persist to this day. New cars can no longer be obtained just by visiting the nearest dealer – in all but the rarest of circumstances, they must be ordered months in advance. Peanut butter and baby formula are just a few of the everyday consumables that have been hampered by widespread shortages in recent months.
Just like consumers, businesses have been affected by these recent dynamics and are looking for better answers. As of 2020, when the pandemic was new and businesses were most fearful, approximately 75% said they planned to build factories closer to where their customers are located.
This makes sense on paper – after all, the CHIPS Act was signed into law on the need to bring strategic semiconductor manufacturing back to the United States, which has been at the heart of the automobile shortages. But can – and more importantly, should – all businesses, across all industries, do the same? Will local manufacturing solve their current and future problems? Let’s take a closer look at what this really means and what enterprises need before their next move.
Let data power your competitive advantage
Organizations initially offshored their manufacturing operations with limited information compared to what’s available today. The initial wave in the 1970s was driven largely by lower labor costs in developing markets. In more recent years, with Americans focusing more heavily on knowledge work, businesses may have found it difficult to kickstart manufacturing operations locally without a significant capital investment. Talent shortages already exist for current manufacturers, and according to a report by Deloitte, there could be 2.1 million unfilled U.S. manufacturing jobs by 2030. Given this, it may be hard for businesses to initiate reshoring plans with confidence.
But no issue is as simple as it seems on the surface. The Suez Canal blockage was a warning shot for how bad things could get, but it's far from the only challenge. Another, comparable incident could further escalate price pressures and eviscerate revenue opportunities. To keep up with a world that is dealing with constant crisis and disruption, businesses need to be able to blend multiple data sources and run scenario planning. This is a huge asset in the quest for certainty and may prove to be the catalyst for bringing manufacturing back to the U.S. while incorporating real-world data and synthetic data for what-if scenarios could make the case for onshoring.
Actionable insights are critical
In a global economy, businesses mainly rely on a complex and often fixed set of third-party suppliers, a system that works quite well when things are going as planned. The last few years have highlighted what happens when they don’t – and without the necessary data to make quick changes, many businesses struggled to fulfill customer expectations.
And although the supply chain problems over the past few years have subsided, there are concerns that new ones will continue in 2023. A report by KPMG shows that nearly three-fourths (71%) of global companies believe that raw material costs will be their number-one supply chain threat this year. Talent acquisition could also remain a problem within the supply chain. According to American Trucking Associations, there will be a shortage of nearly 100,000 truck drivers in 2023 – and more than 160,000 by 2030. Manufacturers may struggle to acquire new talent as well, with the aforementioned Deloitte report noting that U.S. manufacturing execs feel it is now 36% harder to recruit talent than it was in 2018.
Instead of making inferences (ex: assuming that everything current is forever the new normal) based on a catalyst (ex: COVID-19), businesses should build in strategic flexibility based on data to reveal demand forecasts that pinpoint exactly when stockouts happen, and where fluctuating inventory costs might occur. No organization can prepare for these and other “what if?” scenarios – nor would they be able to plan for demand volatility and constraints around suppliers or materials – without actionable insights.
Future actions should be guided by data
Contrary to popular belief, local manufacturing still exists – but while it used to be the norm, it is now often the exception. For every automobile or snack food produced within the United States, there are hundreds of products – from electronics and cookware to tools, diapers, storage units and beyond – that are produced overseas.
Locally made goods are now pieced together using an assortment of materials from around the world. By first chasing a better price through offshoring whenever possible, and by turning to Just-In-Time inventory to reduce warehousing expenses, organizations were able to transform into leaner operations. But now they need to transform once more, and the degree to which that transformation will take place should be entirely guided by data.