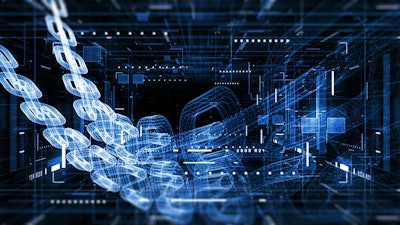
When the goods needed to stock a freezer or feed an assembly line don’t arrive as expected or workers must be sent home, equipment sits idle and revenue falls. Everyone suffers. That’s why all of us breathed a huge sigh of relief when COVID-19 appeared to be in our collective rearview mirror. Finally, it looked as though a return to normalcy was in sight.
Or was it? The past year has shown us that supply chains are far more fragile than any of us thought. Pandemic aside, a military invasion in Europe had drastic global ramifications on supply chains. There have been rising fuel costs, container shortages, weeks-long port backups and a cargo ship run aground in a crucial waterway. Each disruption caused delays in shipping everything from lumber to pet food, computer chips to toilet paper.
Worse, these disruptions have further increased transportation and logistics costs, adding insult to the inflation-driven injury felt over recent months. It seems that manufacturers and service providers —not to mention the suppliers, truckers, ports and distribution centers who support them— can’t catch a break.
According to a recent survey from IDC, 70% of companies are looking for ways to improve supply chain visibility. These might include an automaker concerned over the aforementioned chip availability. It could be an appliance manufacturer wondering whether stamped components will arrive on time, or a produce processing facility worried about droughts in the Southwest.
Sharing is caring
The White House has stepped in to help, launching the Freight Logistics Optimization Works (FLOW) initiative intended to “pilot key freight information exchange between parts of the goods movement supply chain.” Together with a small but representative group of key stakeholders and led by the Department of Transportation (DOT), the Administration will develop a proof-of-concept model designed to “ease supply chain congestion, speed up the movement of goods, and ultimately cut costs for American consumers.”
Perhaps your company is fortunate enough to be part of this initiative. If not, don’t despair. Nor should you wait to see its results, because the industry already has access to tools that address the initiative's primary goal of improved information exchange between supply chain members. It's called the virtual twin, and it not only increases visibility into events that might negatively affect a supplier's ability to deliver products on time but gives all involved the power to predict and avoid such problems.
Digital links are strong links
Whatever the scenario, each represents an opportunity for digitalization. For example, a produce company can gather real-time production information from its suppliers and data from cloud-connected sensors in the field, then use it to more accurately predict when foodstuffs will arrive and in what quantities. These same sensors can also be placed in shipping containers and semi-tractor trailers to notify the company that something has gone awry— that a truck is sitting on the side of the road somewhere, a refrigeration unit has malfunctioned or that the shipment will arrive early and it's time to call in extra workers.
Similarly, through virtual twins, automakers feeling apprehensive about shutting down a production line due to missing components can gain visibility and clarity through continuous monitoring of their suppliers’ factory floors and raw material inventory levels. They can use the industrial internet of things (IoT) to track machine tool output and see well in advance that it’s trending downward (and in the not-too-distant future, they might even apply AI to identify the cause). If there’s no chance to remedy the situation, they can then either re-source the missing product or, worst case, notify other suppliers to back off on their deliveries until the bottleneck is resolved.
Information sharing like this is a small part of the FLOW initiative, but the benefits are far more significant than knowing whether a truckload of potatoes will arrive on time. By integrating these and other data sources with a virtual twin of the supply chain that includes all potential failure points and— conversely— areas for improvement, companies gain a comprehensive tool that helps them avoid disruptions, reduce costs and optimize every link in the chain.
The supply chain virtual twin enables inclusive collaboration and decision-making between all stakeholders, whether they are driving rapid innovation or reacting to disruptions. These stakeholders exist in diverse internal departments, such as design and engineering, as well as externally across contract manufacturers and suppliers. By using this connected platform, stakeholders can design supply chains at the same time as the product and mitigate supplier shortages with real-time changes to product engineering. In fact, every aspect of the supply chain can be analyzed and optimized against the product lifecycle to positively impact critical business KPIs.
But hold on: sensors in shipping ports and tractor trailers? Remote monitoring of a supplier’s machine tools? Beaming data from farm fields to the cloud? Sounds farfetched, right? Not really. Samsung Corp., for instance, says telematics technology for trucking fleet management is commonplace. Machine shops and sheet metal fabricators have begun gathering data from the production floor and using it to increase productivity. The Stars Project, sponsored by the Bill and Melinda Gates foundations, uses satellites, drones and remote sensing technology to monitor crop health in remote areas. This information and much more is accessible via cloud-based platforms and can easily be incorporated into digital modeling systems like the virtual twin.
The time has come. These and other Industry 4.0-related tools are ready for prime time. They’re eminently deployable, cost-effective and boast robust interoperability with existing technology. All can integrate with and feed information to the virtual twin, giving companies unprecedented visibility to their supply chains and the ability to drive positive change within their organizations. The FLOW project should enjoy clear weather and favorable winds, if only its members choose to leverage digital technology including virtual twins throughout the supply chain management process.